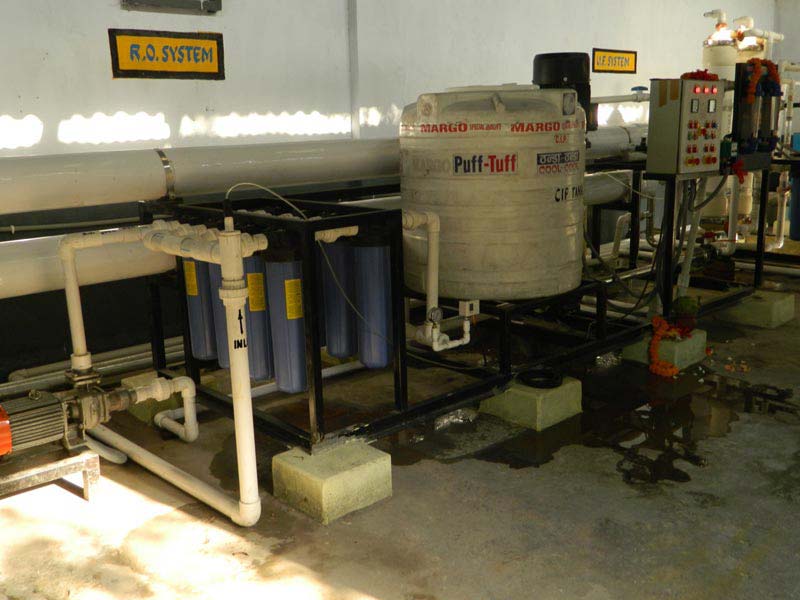
For wastewater tanks, epoxy coatings offer a high degree of chemical resistance and ease of application. More specifically, the standard liquid bisphenol A epoxy with polyamine hardener has proven to be very durable in wastewater tanks.
What is the best coating for wastewater tanks?
More specifically, the standard liquid bisphenol A epoxy with polyamine hardener has proven to be very durable in wastewater tanks. Other coating technologies such as polyureas, urethanes and vinyl esters also offer a high degree of chemical resistance but often are not easily applied.
What are coating coatings used for in aquariums?
You’ll find coatings used in tanks, troughs, aerators, filter beds, and even clarifiers – pretty much anything that comes into contact with a combination of chemicals or water.
Which coating technology has the best chemical resistance?
Other coating technologies such as polyureas, urethanes and vinyl esters also offer a high degree of chemical resistance but often are not easily applied. While epoxies generally have excellent chemical resistance and are user-friendly, they need to be applied under the right conditions.
What is the best type of epoxy for a wastewater tank?
For wastewater tanks, epoxy coatings offer a high degree of chemical resistance and ease of application. More specifically, the standard liquid bisphenol A epoxy with polyamine hardener has proven to be very durable in wastewater tanks.
What are the chemicals that can be used to protect concrete?
What is epoxy coating?
What is coal tar epoxie?
What are the different exposure conditions for floor coating?
Does polyurethane cure fast?
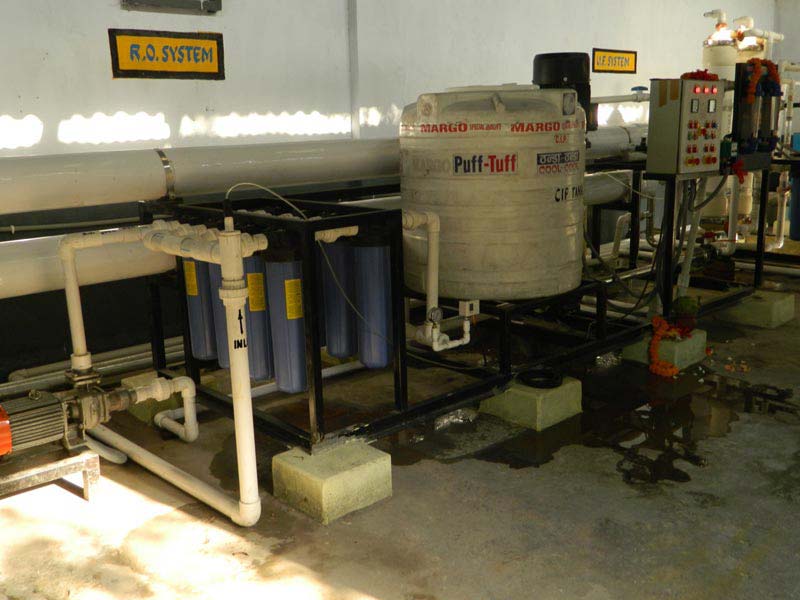
What material is used in sewage treatment plant tank construction?
Bolted, powder-coated-epoxy-steel tanks are some of the most widely used in wastewater storage and treatment operations. Their low initial cost compared to field welded and bolted, glass-fused-to-steel tanks often give them an advantage.
Which chemical most commonly used in wastewater treatment?
Certain basic or alkaline chemicals used to raise wastewater pH are below: CaO (calcium oxide or lime), MgO (magnesium oxide), Ca (OH) (calcium hydroxide, a hydrated form of lime) or Mg (OH) (magnesium hydroxide) are the most commonly used chemicals because of availability, low cost, and high capacity.
Which coagulant is widely used in water treatment plant?
Ferric chloride is widely used for sewage treatment and Alum is widely used for water treatment.
Which type of screen is mostly used in advanced wastewater treatment plant?
Three common types of fine screening in wastewater treatment are: Drum Screens (rotating cylinders in the flow channel) Step Screens (fixed and movable plates across the width of the channel) and Static Wedge Wire Screens (used by large treatment plants with ample floor space)
What chemicals are used at a water treatment plant?
The most commonly used chemicals for water treatment process are:Algicide.Chlorine.Chlorine dioxide.Muriatic acid.Soda ash or Sodium bicarbonate.
Which chemical is used to purify water in the waste water treatment plant?
A chemical that is also present in wastewater treatment plant is ferric chloride. Ferric chloride is a corrosive chemical used in water purification and sewage treatment. The function of ferric chloride is to remove metal substance from the waste that highly possible will harm environment as well as living being.
What is the most used coagulant?
Aluminum sulfate (alum)Aluminum sulfate (alum) is the most common coagulant used for water purification. Other chemicals, such as ferric sulfate or sodium aluminate, may also be used. Coagulation is usually accomplished in two stages: rapid mixing and slow mixing.
Which coagulant used top mostly?
Aluminium sulphateExplanation: Alum or Aluminium sulphate is most commonly used as coagulants in water treatment.
Which of the following is best coagulant?
The best Coagulant for removing the color of water isAlum.Lime.Iron sulphate.Copper sulphate.
What is the difference between coarse screen and fine screen?
Coarse screens remove large solids, rags, and debris from wastewater, and typically have openings of 6 mm (0.25 in) or larger. Fine screens are typically used to remove material that may create operation and maintenance problems in downstream processes, particularly in systems that lack primary treatment.
What are the various types of screens used in screening process?
Screens are generally classified into three based on the size of their openings in the screening element and mechanism of removal.Coarse screens.Fine screens.Microscreens.
What is coarse screening?
Coarse screens remove rags, sticks, large solids and other debris ranging from 0.25 to 6 inches. They can be as simple as a trash rack or as complicated as a mechanically cleaned bar screen.
Coatings for water and wastewater processing - Tnemec
Series 431 | Perma-Shield PL Modified Polyamine Ceramic Epoxy. A 100% solids, abrasion-resistant lining specifically designed for wastewater immersion and fume environments and exposure to corrosive soils.
Concrete Construction | ConcreteConstruction.net
t ro u g h s, aera t o r s , filter beds, and c l a ri f i e r s Moist atmospheric exposure in tank exteriors and we t w a l l s Mo d e r ate industrial service on
Wastewater Treatment Plants: Coating Selection Guidelines for Changing ...
Copyright ©2001, Technology Publishing Company ydrogen sulphide (H 2S) generation in munici- pal wastewater treatment plants has always been present. It causes ...
Writing successful paint specifications
This is your project’s most crucial document. Here are the keys to getting it right.
Product Catalog
Interested in viewing our full product catalog? Download a PDF version here and browse it at your own speed.
Why do wastewater treatment facilities need durable flooring?
Concrete, for example, is one of the strongest and most durable flooring options available. Builders have relied on it for centuries, and after the invention of steel-reinforced concrete in the mid-1800s, it became the go-to building material for wastewater treatment plants.
What is CPC floor coating?
CPC Floor Coatings can recommend and install flooring that will resist chemical corrosion and reduce the risk of slip-and-fall accidents. We install both weatherproof coatings for exterior surfaces as well as chemical-resistant floor coatings for interiors.
What is the substance that floats around in wastewater?
Solid material floats around in your wastewater. Ice, salt, rocks, sand, and silt in the water make tiny insults against concrete that over time create a completely smooth surface due to abrasion.
Water & Wastewater
For more than 50 years, we’ve been working with communities, developers, and other construction partners to deliver the highest standard of corrosion protection.
Product Documents
Download our helpful application guides, construction detail guides or system guides.
Contact Your Rep
Reach out to one of our knowledgable and reliable representatives near you.
How to determine if a concrete tank is resistant to wastewater?
The best way to determine if a particular coating is resistant to the wastewater in question is through laboratory analysis . This option often is not economically feasible for the job at hand. When this is the case, the owner or engineer should ask for reference projects from the coating manufacturer (preferably projects with similar exposure conditions).
How can concrete be protected from water?
Concrete can be protected from these root causes by preventing the contained water from coming in contact with the concrete. For obvious reasons, this may not be so easy to accomplish inside a water tank. However, it can be done with the use of protective coatings.
What is concrete used for?
Special methods and materials must be used to protect concrete tanks from the harsh environment in water and wastewater facilities. Concrete is an excellent building material. Man has been using concrete to build all types of structures for many centuries. It has proven to be very durable and very strong in compression.
How to prevent corrosion of reinforced concrete?
A strategy that can be implemented to slow down the corrosion process is the use of penetrating corrosion inhibitors. A corrosion inhibitor, as defined by the American Concrete Institute, is "a liquid or powder that effectively decreases corrosion of reinforcing steel." In the case of existing concrete, a liquid amino alcohol-based corrosion inhibitor can be sprayed onto the surface of the concrete where it will penetrate through the hardened concrete down to the depth of the rebar. When the penetrating corrosion inhibitor reaches the rebar, it forms a protective layer around the steel. Such a method has been shown in independent laboratory tests to reduce corrosion in reinforced concrete by as much as 60 to 70%. This technology requires no special equipment and is easy to apply, making it ideal for plant maintenance crews. This type of corrosion inhibitor also may be used as an admixture to protect rebar in new concrete.
What are the problems with concrete tanks?
Other problems that affect the durability of concrete in water and wastewater tanks include abrasion, chemical attack and freeze-thaw. These destructive forces can significantly reduce the service life of the structure. This article highlights some methods and materials that can be used to protect concrete tanks from the harsh environment in water and wastewater facilities.
When were concrete tanks built?
Unfortunately, there are thousands of concrete tanks that were built in the '70s and '80s that were not adequately protected. As these tanks enter their second and third decade of service, the effects of all those years of unprotected exposure start to become apparent in the form of cracks, spalls and leaks.
Does steel corrode if not protected?
In the presence of moisture and oxygen, steel will corrode if not protected . Under normal circumstances, the high alkalinity of new concrete (pH 12p;13) creates a natural protective oxide layer around the steel known as a passivating layer. As long as this layer stays intact, the steel is protected from corrosion.
What are the chemicals that can be used to protect concrete?
Coating systems are designed to help protect concrete by providing a barrier to various chemicals, such as sulfuric acid, sodium sulfates, ammonium, and moisture penetration.
What is epoxy coating?
Two-Component Epoxies. Epoxy coatings are suitable for immersion service on both concrete and steel and are easy to clean. Because of their high solids content, they comply with strict air quality regulations and are extremely hard and durable.
What is coal tar epoxie?
Coal Tar Epoxies. Coal tar epoxies are economical and are commonly used on concrete and steel to protect against mild chemical attack and abrasion. Coal tar adheres well to bare concrete and is relatively easy to apply with spray, brush, or roller.
What are the different exposure conditions for floor coating?
Understanding that not all coating systems are created equal, consider (4) different exposure conditions of the equipment: immersion service, moist atmospheric exposure, industrial exposure, and interior dry exposure. And, as with any coating application, surfaces must be carefully prepared for maximum service life. Read more about the 7 Important Steps For a Perfect Floor Coating Application .
Does polyurethane cure fast?
Polyurea and polyurethane coatings perform well in immersion service at treatment plants. They dry fast and aren’t temperature dependent for curing. However, the installation process does require additional equipment at an added cost.
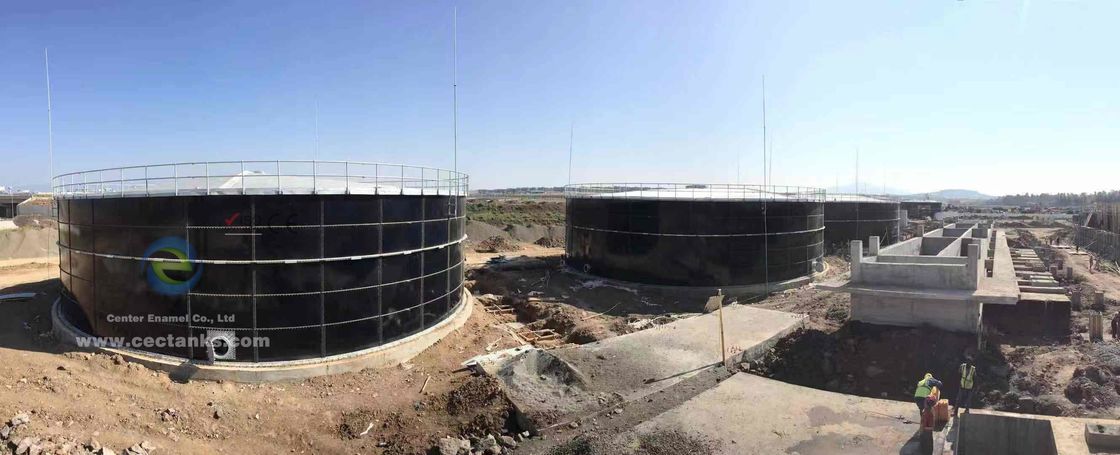