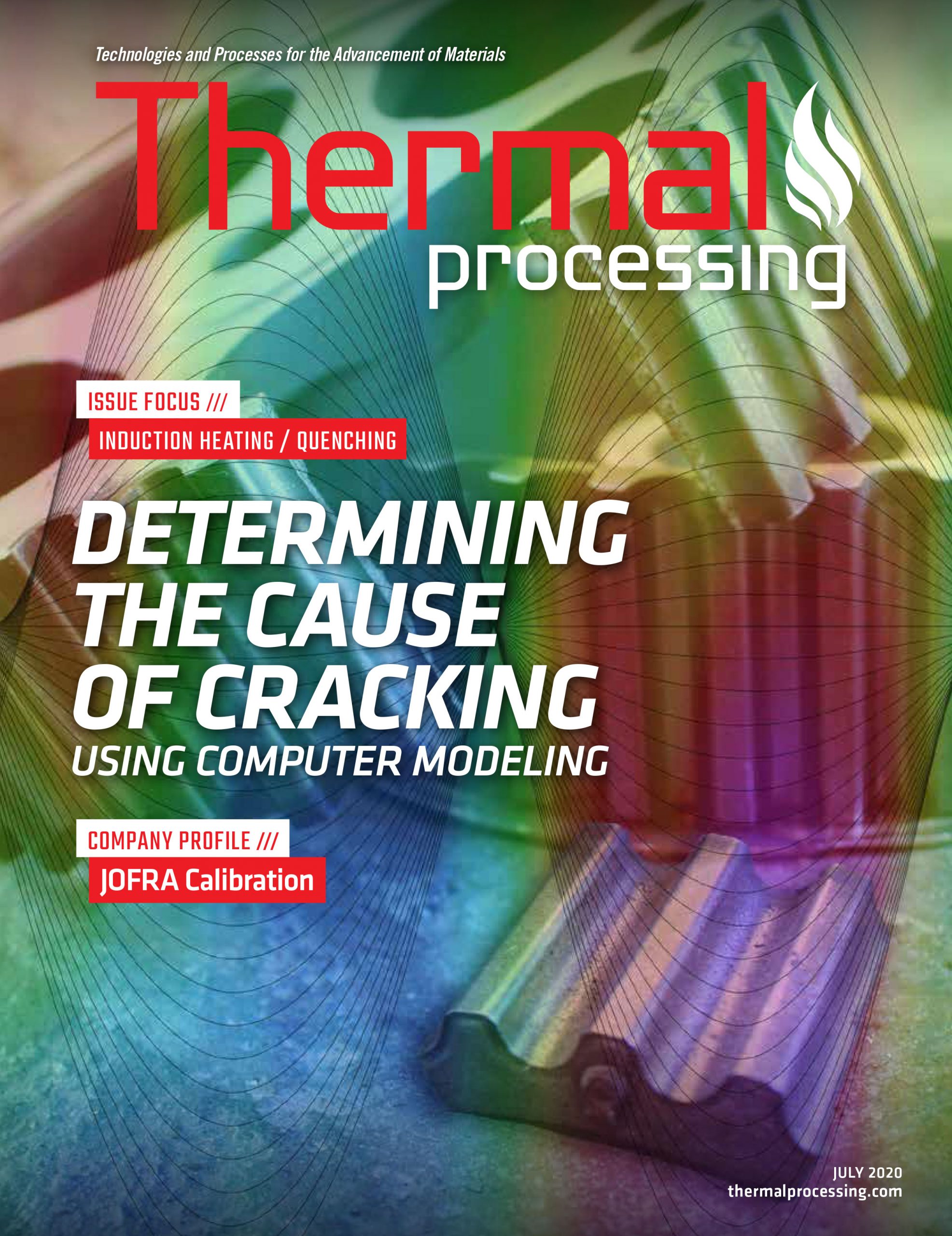
Can aluminum be heat treated?
The process of aluminium solutionizing treatment is slightly different to that of steel heat treatment. It is different in so much as the solution as treatment which involves heating the aluminium alloy up to its appropriate solution temperature followed by quenching rapidly, this makes the alloy extremely soft.
What is the most common defect during heat treatment of aluminum?
· The aluminum-copper system is the basis for the wrought 2xxx and cast 2xx.x alloys, and many other heat-treatable alloys contain copper. Most contain other alloying elements such as magnesium. The main benefit to adding magnesium to aluminum-copper alloys is the increased strength possible following solution heat-treatment and quenching.
How do I prevent distortion when using heat-treated aluminum parts?
· Racking of Parts. Of all the possible “defects” occurring during the heat treatment of aluminum, distortion during quenching is the most common. It is probably responsible for …
What happens when you heat treat a metal?
· One of the questions all Heat Treaters are asked is, “How much, if at all, will my part change (i.e. shrink or grow) during heat treatment?” While the heat treater would love to be …

Does aluminum soften with heat?
Even if the maximum temperature is 400 degrees, the answer is probably not. Just like steel, aluminum alloys become weaker as the service temperature rises. But aluminum melts at only about 1,260 degrees, so it loses about half of its strength by the time it reaches 600 degrees.
Does heat treatment make metal softer?
Referred to as allotropic phase transformation, heat typically makes metals softer, weaker, and more ductile. Ductility is the ability to stretch metal into a wire or something similar. Heat also can impact the electrical resistance of metal.
What happens to aluminum when overheated?
Precipitation-hardened materials such as 6061-T6 aluminum can undergo a process known as overaging when overheated. The precipitates in the aluminum alloy can grow from overheating, which in turn results in them being too large to block dislocations.
Does heat treatment always decreases the hardness of a material?
Which statement is false? Explanation: Heat treatment can increase or decrease the hardness of a material. Quenching improves the hardness of a material by generating internal stress. Some other heat treatments soften the material as annealing or normalizing.
What does heat treating do to metal?
Heat treating can soften metal, to improve formability. It can make parts harder, to improve strength. It can put a hard surface on relatively soft components, to increase abrasion resistance. It can create a corrosion-resistant skin, to protect parts that would otherwise corrode.
How does heat treatment affect metal properties?
Annealing changes a metal's properties by altering and realigning the grain structure using heat, making the metal softer and more ductile. In this process, the steel is heated to just above its re-crystallization point, allowing it to cool slowly. A full anneal involves leaving the metal to cool in the furnace itself.
Can you heat treat aluminum?
To anneal a work hardened aluminum alloy, the metal must be heated to somewhere between 570°F to 770°F for a set amount of time, ranging from just thirty minutes to a full three hours.
Does welding aluminum weaken it?
Welding aluminum generally will weaken it, and for a few different reasons. The main reason is that heat will affect the temper of the aluminum, which can result in a loss in yield strength of roughly half in many cases if measures aren't taken to correct it.
Can you heat straighten aluminum?
When straightening aluminum, there are some temperature ranges that can be very effective. The general repair temperature guidelines are to heat the aluminum to a temperature range of 200-300°C or 400-570°F. Exceeding this range can approach the annealing temperature, which could compromise the strength of the metal.
Why does hardness increase after heat treatment?
The reason for this increasing hardness is the formation of a finer pearlite and ferrite microstructure than can be obtained during slow cooling in ambient air. In principle, when steel cools quickly, there is less time for carbon atoms to move through the lattices and form larger carbides.
What is the effect of heat treatment on hardness of material?
Although the hardness decreases, the heat-treated hardness is still greater than the as-cast state. After destabilisation treatment at 1130°C, tempering at 200 to 250°C for 3 hours leads to the highest impact toughness, and secondary hardening was observed when tempering over 400°C.
What is the effect of heat treatment?
The heat treatment develops hardness, softness, and improves the mechanical properties such as tensile strength, yield strength, ductility, corrosion resistance and creep rupture. These processes also help to improve machining effect, and make them versatile.
What is the purpose of heat treating aluminum?
When used in conjunction with aluminum alloys, the term ‘heat treating’ is generally restricted to solution heat treatment, quenching, and subsequent aging of aluminum alloys to increase strength and hardness . These usually are referred to as the ‘heat-treatable’ alloys to distinguish them from those alloys in which no significant strengthening can be achieved by heating and cooling. The latter, generally referred to as ‘non-heat-treatable’ alloys, depend primarily on cold work to increase strength.
What is a non-heat treatable alloy?
These usually are referred to as the ‘heat-treatable’ alloys to distinguish them from those alloys in which no significant strengthening can be achieved by heating and cooling. The latter, generally referred to as ‘non-heat-treatable’ alloys, depend primarily on cold work to increase strength.
Is zinc a good addition to aluminum?
Zinc confers little solid solution strengthening or work hardening to aluminum, and no significant technical benefits are obtained by the addition of just zinc to aluminum. However, the addition of copper and/or magnesium with zinc results in attractive compositions for heat treating or natural aging. Usually, other elements, such as chromium, are also added in small quantities.
What is an Al-Mg alloy?
The Al-Mg system is the basis for the wrought 5xxx and cast 5xx.x non-heat-treatable aluminum alloys. The addition of magnesium provides solid solution strengthening without unduly decreasing the ductility. The Al-Mg alloys offer an excellent combination of solid-solution strengthening, corrosion resistance, and the strengthening of wrought alloys by work hardening.
Is magnesium good for aluminum?
The main benefit to adding magnesium to aluminum-copper alloys is the increased strength possible following solution heat-treatment and quenching. In both casting and wrought alloys, as little as 0.05 percent magnesium is effective in changing aging characteristics.
What is the percentage of Cu in aluminum?
Most commercial Al-Cu alloys contain other alloying elements. Aluminum-copper alloys containing 2 to 10 percent Cu, generally with other additions, form important families of alloys. The aluminum-copper system is the basis for the wrought 2xxx and cast 2xx.x alloys, and many other heat-treatable alloys contain copper. Most contain other alloying elements such as magnesium.
What is age hardening alloy?
Age-hardening alloys are precipitation strengthened indicated by heat-treatment tempers (T-tempers). Depending on the alloying elements, strengthening of aluminum can be achieved by heat treatment or by solid solution strengthening (often in conjunction with work hardening).
What happens when aluminum is cast?
When casting aluminum alloys, the outside edge in contact with the mold cools first, forming a skin of aluminum crystals, also known as grains. As the cooling process continues towards the center, the casting has regions of pure aluminum near the skin and other regions near the center, where the alloying element (s) precipitate out and lock crystal regions in place. This results in areas where the casting is soft and others that are strong.
What temperature to heat treat alloy?
Solution heat treatment occurs at a range from 825°F to 980°F, with the specific temperature depending on the alloy.
What is the process of shaping aluminum alloys?
Annealing. The process of shaping aluminum alloys causes the grain structures to slide against one other, along areas known as slip planes. After a while there are less easy slip planes, and increased force is required to shape the part. This state is referred to as work hardened.
What is the process of hardening an alloy?
Some alloys require heat to fully precipitate out the dissolved elements and reach their maximum hardness. This process is called precipitation hardening. These alloys will harden some at room temperature, with the amount depending on the specifics of the alloy.
How long does it take for an alloy to harden?
The elements that dissolve during the solution heat treatment process precipitate out over time after the quench and lock the grains into position, increasing the strength of the material. For naturally aged alloys, this happens at room temperatures and takes four or five days to reach full strength, but 90% of the hardening happens in the first 24 hours. The process starts immediately after the quench, but because it is a slow process there is a window to shape the alloy with relative ease immediately after quenching.
How long does it take to soak metal?
Soaking time is another key component of solution heat treatment, and it is a measure of time from when the coldest metal reaches the minimum limit of the desired range until quenching. For thin parts, the soaking time may be 10 minutes, while a heavy part may need 12 hours to soak.
What is solution heat treatment?
In solution heat treatment the elements that cause age hardening dissolve, undissolved elements become spheroids, and the whole structure becomes homogenized. The quench traps dissolve elements in the solution that will later precipitate out and create the age hardening effect. Right after the quench the alloy is usually easy to work with, but as time passes, it will harden and become difficult to work.
What are the problems with aluminum heat treatment?
Of all the possible “defects” occurring during the heat treatment of aluminum, distortion during quenching is the most common. It is probably responsible for most of the non-value-added work (straightening) and costs associated with aluminum heat-treating.
Why does aluminum grow faster when heated?
If the parts are tied to the steel support too rigidly, the aluminum will grow at a much greater amount than the steel during heating. Upon cooling, the aluminum will contract more than the steel. Allowing movement of the aluminum by loosely attaching the parts to the rack will allow movement of the aluminum and reduce distortion.
Is AQ Temper ductile?
Immediately after quenching, AQ Temper alloys are nearly as ductile as the “O” or annealed condition. Because of this, as-quenched alloys are often formed after quenching, but before artificial aging.
Why is it important to have a higher quench rate?
Much higher quench rates are necessary in aluminum to prevent premature heterogeneous precipitation occurring during quenching, and to maintain supersaturation of the solute. In steel, there is a coupled phase transformation of austenite to martensite. This causes a 3 percent volume change during quenching.
Do water-quenched parts need to be straightened?
This is particularly true for water-quenched parts. Parts must be straightened. This is often much easier in the as-quenched condition before aging. However, there are certain things that must be understood to achieve straight parts.
Can quenching cause distortion?
and the effect of forming or straightening on the final aged part. After quenching, depending on the quenchant used, distortion of parts can occur. This is particularly true for water-quenched parts. Parts must be straightened. This is often much easier in the as-quenched condition before aging.
Why should aluminum parts enter the quenchant?
Because of the poor strength of the heat-treated aluminum parts, distortion of the parts can occur as they enter the quenchant . Generally, parts should enter the quenchant aerodynamically to avoid distortion to the part before it even enters the quenchant. It should enter the quenchant smoothly — it should not “slap” the quenchant.
Homogenization (Ingot Preheating Treatment)
The initial thermal operation applied to castings and ingots (prior to hot working) is referred to as homogenization, which has one or more purposes depending on the alloy, product and fabricating process involved.
Annealing
Annealing can be used for both heat treatable and non-heat treatable alloys to increase ductility with a slight reduction in strength. There are several types of annealing treatments dependent to a large part on the alloy type, initial structure and temper condition.
Precipitation Hardening
Heat-treatable aluminum alloys contain amounts of soluble alloying elements that exceed the equilibrium solid solubility limit at room (and moderately higher) temperature. The amount present may be less or more than the maximum that is soluble at the eutectic temperature.
Solution Heat Treating
The purpose of solution heat treatment is the dissolution of the maximum amount of soluble elements in the alloy into solid solution. The process consists of heating and holding the alloy at a temperature sufficiently high and for a long enough period of time to achieve a nearly homogenous solid solution in which all phases have dissolved.
Quenching
Rapid, uninterrupted quenching in water or polymer is, in most instances, required to avoid precipitation detrimental to mechanical properties and corrosion resistance.
Aging (Age Hardening)
Age hardening is achieved either at room temperature (natural aging) or with a precipitation heat treatment (artificial aging) cycle. The same general rules used in solution heat treatment (temperature uniformity, time at temperature) apply for precipitation hardening.
Why do dimensions of heat treated parts undergo changes?
Dimensions of heat-treated parts undergo changes because of uneven temperature and structural phase transformations. On the basis of X-ray measurements of lattice parameters (Table 1) the specific volume (V) of the important phases and phase mixtures present in carbon steels can be calculated using the following equation:
What factors affect the size of a heat treater?
These factors included: the steel supplier (both mill and service center); chemistry; condition of the steel (i.e. grain size, cleanliness, mill treatment practice); manufacturing sequence; heat treatment, and required hardness. Within the heat treatment process, the heat treater committed to precisely controlling the parameters for load size, load configuration (spacing/racking/fixturing), ramp rates, soak times, pre-heat temperature, austenitizing temperature, quench rates and tempering temperature.
What happens after tempering?
After tempering, more dimensional changes will occur with D-2 tool steel (Fig. 3). The dimensional changes on hardening and tempering must be added together when trying to estimate total size change. Final part hardness is determined by tempering temperature. Figure 3 demonstrates why the hardness requested by the customer will have a drastic effect on size change.
How does austenite affect the contractive effect?
The higher the carbon content of the austenite prior to quenching, the lower the Ms point, and therefore, the greater the amount of austenite retained after quenching to room temperature. Increasing the amount of retained austenite of a given carbon content tends to increase the contractive effect .
Can heat treaters predict part size?
While a precise forecast of a part’s size change cannot be expected, by considering each of these potential factors, a heat treater can provide a reasonable estimate that can help manufacturing prepare for final machining operations.
Does heat treating affect part size?
In addition, heat-treating itself adds its own unique set of variables, which also may influence part size change. These are:
How much will my part shrink during heat treatment?
shrink or grow) during heat treatment?” While the heat treater would love to be able to give a precise answer to this question, in most situations volumetric size change during heat treatment cannot be accurately predicted, at least not accurately enough to allow for final machining and/or grinding to close tolerances prior to heat treatment.
Why do metals need heat treatment?
The most common reasons that metals undergo heat treatment are to improve their strength, hardness, toughness, ductility, and corrosion resistance. Common techniques for heat treatment include the following: Annealing is a form of heat treatment that brings a metal closer to its equilibrium state.
How does heat affect metal?
Effects of Heat on Metal. Subjecting metal to extreme heat causes it to expand in addition to impacting its structure, electrical resistance, and magnetism. Thermal expansion is pretty self-explanatory. Metals expand when subjected to specific temperatures, which vary depending on the metal.
Why is tempering used in steelmaking?
Commonly used in steelmaking today, tempering is a heat treatment used to improve hardness and toughness in steel as well as to reduce brittleness. The process creates a more ductile and stable structure.
How long does it take for precipitation hardening to take place?
It can take anywhere from an hour to four hours to carry out the process. The length of time typically depends on the thickness of the metal and similar factors.
What is the process of quenching metal?
The quenching process stops the cooling process from altering the metal's microstructure.
What is annealing metal?
Annealing is a form of heat treatment that brings a metal closer to its equilibrium state. It softens metal, making it more workable and providing for greater ductility. In this process, the metal is heated above its upper critical temperature to change its microstructure. Afterward, the metal is slow-cooled.
What is heat treatment?
Heat treatment is the process of heating and cooling metals to change their microstructure and to bring out the physical and mechanical characteristics that make metals more desirable. The temperatures metals are heated to, and the rate of cooling after heat treatment can significantly change metal's properties.
Why are metals heat treated?
But basically, the process for heat treating of metals involves the controlled application of heat to alter the physical — and sometimes, chemical — properties of the material.
How to heat treat metal?
Depending on the method used, heat treated metals become harder or softer, more or less brittle, or stronger or weaker. Based on the desired end results, the method may involve: 1 Using several treatments 2 Altering the temperature at which the metal is heat treated 3 Varying the length of time heat is applied 4 Controlling how quickly or slowly the material is cooled
Why is low carbon steel annealed?
Low carbon steel can be annealed in a carbon-rich environment to case-harden the steel with a high carbon surface layer that has good fatigue and wear resistance. This technique is used to improve the hardness and durability of products such as carbon steel wire springs and forgings.
Can you heat treat tungsten?
For instance, if you heat treat tungsten in a normal atmosphere, it will produce oxidation that makes the surface finish porous. However, working in a controlled environment — such as a vacuum or a sealed nitrogen, argon, or hydrogen atmosphere — allows you to heat treat the metal without oxidation.
How long does a metal stay hot?
The material is held at high temperature for anywhere from several hours to several days and then allowed to cool (in the case of steels and other ferrous metals, very slowly).
Can stainless steel be annealed?
For example, as 316 stainless steel is worked, it can pick up undesirable magnetic properties; however, annealing the stainless steel can restore it to (or very close to) its original nonmagnetic condition. Annealing is performed using specialized furnaces in which conditions are tightly controlled.
What is annealing metals?
Often used interchangeably with the term heat treating , annealing is a specific method used to soften metals, with the goals of increasing their ductility and decreasing brittleness . Annealing can also be used to increase the homogeneous nature of metals, as well as to restore their ductility prior to further handling.
How to stop aluminum hardening?
The aluminum hardening process can be stopped by placing aluminum parts in a freezer until they’re ready to be hit on the press again. After this secondary pressing, the parts go through an aging heat treatment process.
What is the most common temper for aluminum?
In general, T6 is the most common temper for aluminum, and because 6061 aluminum is often used in heavy-duty structures, the strength and limited formability of metal at that temper is important.
How long does it take to age aluminum 6061?
Aging aluminum 6061 is done between 350 to 500 degrees Fahrenheit, and—depending on thickness and other factors—the parts stay in the oven for 12-24 hours. Following this aging, the parts are now at a T6 condition.
How long does it take for 6061 T4 aluminum to harden?
Because time and room-temperature air can also have a hardening effect, setting these newly treated aluminum parts in the open on the workroom floor for 96 hours will bring the parts to T4 hardness. 6061-T4 aluminum is part way to the hardest that this aluminum alloy can be.
How to make 6061 aluminum stronger?
The process of taking a 6061 aluminum part in O condition to a stronger, more durable condition begins by heat treating the parts at 985 degrees Fahrenheit for an hour in a drop bottom furnace. At that point, the basket containing the parts is dropped into a quench tank.
Is 6061 aluminum ductile?
6061 aluminum is a ductile metal that can be stamped, cut, deep drawn, drilled, tapped, bent, welded, hydroformed and more. Magnesium and silicon are the major alloying elements in this metal, and 6061 is generally strong and corrosion resistant. It is heat treatable and crack resistant when stress is removed.

Homogenizing
Annealing
Solution Heat Treatment
Natural Aging
Artificial Aging/Precipitation Hardening
Conclusion
- While not all aluminum alloys benefit from heat treatment, we can heat-treat several alloys to increase the ease of forming or the strength of the finished product. Unlike steel or iron, aluminum requires rigid heat control to achieve optimal results, so special equipment is often required. Attention to detail results in aluminum alloys that are ea...
Sources and Further Reading
Types of Heat Treatment
- Heat treatments applied to aluminum and its alloys are: 1. Preheating or homogenizing to reduce chemical segregation of cast structures and to improve material workability 2. Annealing to soften strain-hardened (work-hardened) and heat-treated alloy components, to relieve stresses and to stabilize properties and dimensions 3. Solution heat treatmen...
Homogenization
Annealing
Precipitation Hardening
Solution Heat Treating
Quenching
Aging