
Record times that parts are removed from furnaces to document that objects have attained specified temperatures for specified times. Determine types and temperatures of baths and quenching media needed to attain specified part hardness, toughness, and ductility
Ductility
In materials science, ductility is a solid material's ability to deform under tensile stress; this is often characterized by the material's ability to be stretched into a wire. Malleability, a similar property, is a material's ability to deform under compressive stress; this is often characterized b…
Full Answer
What is a heat treatment furnace?
Mar 15, 2022 · It is important to distinguish the difference between a temperature controller and recorder. Section 3.2.3.2 does not require a furnace to control with decimal precision, only record to it. However, best practice lends itself to controllers supporting this ability as well. Figure 1. Maximum permissible leak rates.
When is a Class 1 heat treatment furnace required?
Tempering. Tempering is a process that is often used after a material has been quenched. A heat treatment furnace tempering a material would help to reduce the brittleness and remove any stresses caused by quenching. In this process, the steel is heated to a specific temperature and then cooled. If the material is heated to 300 – 750 o C ...
What are the common heat treatment techniques used in industries?
Furnaces are one of the most versatile types of industrial appliances that span many different areas of use. This article discusses the classification of various furnaces used in heat treating based on the mode of operation (batch-type furnaces and continuous-type furnaces), application, heating method, mode of heat transfer, type of materials handling system, and mode of waste …
What is a charts and tables used for in a furnace?
It is the combination of thermal, industrial, and metalworking processes to alter the mechanical properties and chemical properties of metals. In simple words, heat treatment is a process of heating the metal, holding it there for some time, and then cooling it back. During the whole process, the mechanical properties get changed due to changes ...

What is furnace heat treatment?
Heat treating (or heat treatment) broadly refers to a group of thermal processes in industrial and metalworking applications used to intentionally alter the physical, and sometimes chemical, properties of a material (usually a metal).
What is heat treatment process?
What is the purpose of heat treatment?
What are the 3 stages of heat treatment process?
- Heating: Heating is the first stage in a heat-treating process. ...
- Soaking: Soaking is the stage at which the complete part of the heated metal completely changes in its structure. ...
- Cooling: The third stage of heat treatment is cooling.
What are the three types of heat treatment?
- Heat Treatment Steel: Annealing.
- Heat Treatment Steel: Normalizing.
- Heat Treatment Steel: Hardening.
- Heat Treatment Steel: Tempering.
What is heat treatment process and types?
What are the five basic heat treatment process?
What is annealing in heat treatment?
What is soaking time?
What is heat treatment?
Heat treatment involves heating of metal in the solid-state and then subsequently cooled at varied cooling rates. It is very important manufacturing process that can not only help the manufacturing process but can also improve the product, its performance, and its characteristics in many ways. By Heat Treatment process, Example: The plain carbon ...
What temperature does annealing take place?
Annealing consists of heating of steel parts to a temperature at or near the critical temperature 900 degree Celsius hold it at that temperature for a suitable time and when allowed to cool slowly in the Furnace itself. The heating done during annealing affects the metal in two stages of recovery and recrystallization.
What is annealing in metal?
Annealing is carried out for accomplishing one or more of the following: Softening of a metal or alloy. This may be done due to improving machinability. Relieving internal residual stresses caused by the various manufacturing process. Refining the grain size of the metal or alloy.
What is recrystallization in steel?
This causes complete recrystallization in steel to form New grain structure. This will release the internal stresses previously the strip in the steel and improve the machinability.
What is normalizing steel?
Normalizing is a heat treatment process similar to annealing in which the Steel is heated to about 50 degree Celsius above the upper critical temperature followed by air cooling. This results in a softer state which will be lesser soft than that produced by annealing.
What is the purpose of hardening steel?
Hardening is carried to accomplish the following: To reduce the grain size. Obtain maximum hardness.
What is nitriding used for?
Nitriding is generally employed to Steel parts which are moving like engine parts such a cylinder, crankshaft, etc. 6. Cyaniding: Cyaniding is also a surface hardening process in which the heated parts to be surface hardened are immersed in a bath of molten sodium or potassium cyanide.
What is heat treatment?
Heat treatment is a heating and then cooling process using predefined methods to achieve desired mechanical properties like hardness , ductility, toughness, strength, etc. It is the combination of thermal, industrial, and metalworking processes to alter the mechanical properties and chemical properties of metals.
What is the first step in heat treatment?
The first step in the heat treatment process is heating the metal. The temperature depends on the types of metal and the technique used. Sometimes you need to heat the outer surfaces of the metal, and sometimes you need to heat the whole body. That depends on what kind of alteration you want in the mechanical structure.
What is process annealing?
Process annealing is done when metal is heated below the critical temperature, keep it for a suitable time, and then cool it slowly. This process is suitable for low carbon steel like sheet metal and wires. No phase transformation occurs during process annealing, and it’s considerably cheaper than full annealing.
What is the process of hardening metal?
After that, the metal piece is cooled into lime water so that cyanide salt is sticking to the outer surface of the metal. This cyanide salt is responsible for hardening the outer surface of the metal.
What is the process of cooling a metal piece quickly after it is heated?
Quenching is a process of cooling a metal piece quickly after it was heated. Quenching helps metals to become harder or softer depending upon whether it’s a ferrous or non-ferrous alloy. In the case of ferrous alloy, quenching helps to make it harder, but it becomes softer in the case of non-ferrous.
What happens after holding a furnace?
After the holding process, cooling starts. The cooling must be done in a prescribed manner. During cooling, there are some structural changes occur. Different media such as water, oil, or forced air is used to aid in cooling. You can also use furnaces for cooling purposes as the control environments help inefficient cooling.
How is annealing done?
Annealing is done by heating the metals at the above critical temperature , hold them there for some time and then cool it at a very slow rate in the furnace itself. Annealing is usually done on ferrous and non-ferrous metals to reduce hardness after the cold working process.
What are the different types of heat treatment?
Monitoring and/or controlling the heat-treatment process is accomplished by use of sensors and measurement devices. The most common of these are: 1 Oxygen (carbon) probes 2 Non-dispersive infrared analyzers (NDIR) – single- or multiple-gas 3 Dew-point analyzers 4 Oxygen analyzers 5 Combustion analyzers
What is a carbon probe?
1) is an in-situ device that looks similar to a thermocouple for measuring temperature and typically sits inside the furnace, inside the generator (typically above the catalyst bed or in a separate heated “well” into which the furnace atmosphere is pumped).
Is atmosphere control manual or automatic?
In one form or another, atmosphere control has been around for decades, and the control method may be categorized as either manual or automatic. There are benefits and limitations to both (Table 1).
Where is the oxygen probe located?
1) is an in-situ device that looks similar to a thermocouple for measuring temperature and typically sits inside the furnace, inside the generator (typically above the catalyst bed or in a separate heated “well” into which the furnace atmosphere is pumped). In whatever location, the oxygen probe measures minute changes in oxygen concentration of the furnace atmosphere.
What is the purpose of carbon probes?
Carbon (oxygen) probes, shim stock or carbon analyzers and dew point are typically used to measure the carbon potential of the endothermic atmosphere in a heat-treatment furnace. An infrared analyzer can also be used.
Who is Dan Herring?
Dan Herring is president of THE HERRING GROUP Inc. , which specializes in consulting services (heat treatment and metallurgy) and technical services (industrial education/training and process/equipment assistance). He is also a research associate professor at the Illinois Institute of Technology/Thermal Processing Technology Center. tel: 630-834-3017; e-mail: [email protected]; web: www.heat-treat-doctor.com
First variation: temperature decimals
Decimals have been added to the class list, so we have to get used to writing 6.0°C and not 6°C.
Second variation: the classes of heat treatment furnaces 2 and 3
Confirmed ±5.0°C for Class 2 and ±7.0°C for Class 3, in fact the new AMS2750F has accepted the declaration in force of Nadcap Task Group of Heat Treatment (HTTG).
Third variation: types of instrumentation of heat treatment plants
When it comes to the Type of instrumentation of Heat Treatment plants, in practice it indicates the type of equipment of the system, therefore the number of temperature sensors and the number of instruments connected to them.
What is thermal mapping?
Thermal Mapping is taking an oven or furnace and profiling the temperature at different locations. If it's a long furnace line, you would choose multiple 'essential' points and monitor the temperature at each point. If it's a temperature chamber (such as a closed oven) you measure different points within the oven.
What is thermocouple wire?
A thermocouple is two pieces of special wire which are welded together. There are different types each of which is for a specific temperature range. The ends of these wires are attached to a measurement device which measures electrical potential.
Do they put thermocouples in blenders?
Yes, they are putting the thermocuple (3 of them) through each lot. The product is a shaft for a blender blade. Having never seen a thermocouple, I would think that it is recording the temperture in the differant locations. Right?
What is process qualification?
Process Qualification#N#I am referring to 'Measurement of uniformity of Temperature across the cross-section as well as in the depath, particularly in 'PIT TYPE' Heat Treatment Furnaces -say, a Gas Carburising Furnace or even a Salt bath furnace.
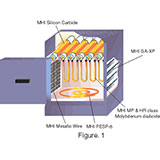