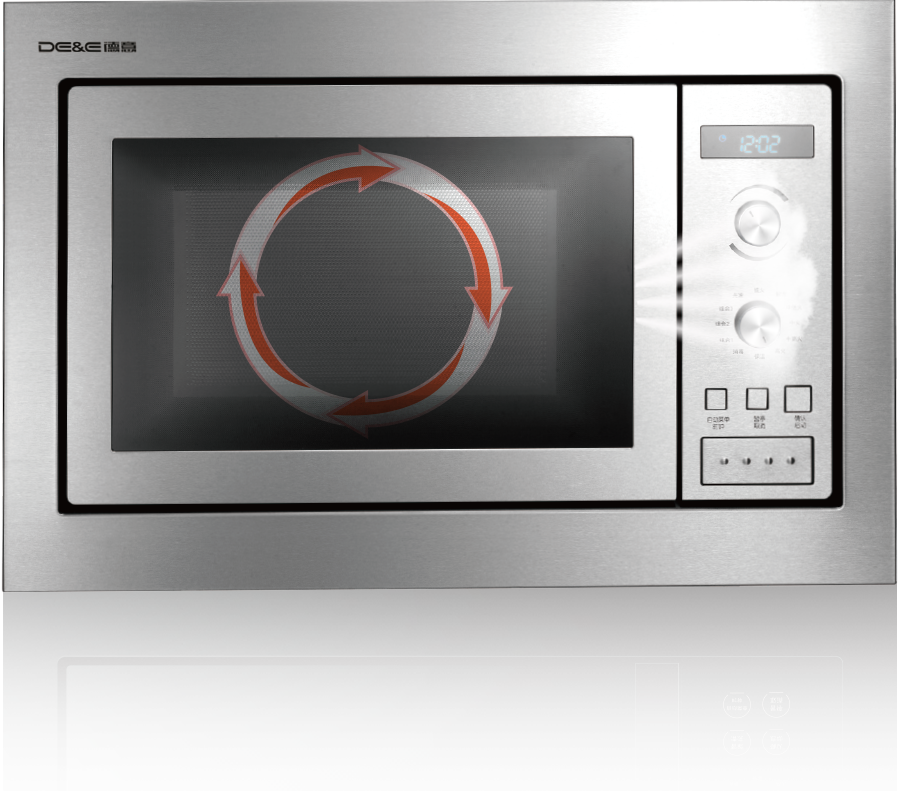
Heat treating for the Aerospace Industry
- More Strength, Longer Life. Heat treating is the application of heat or cold to alter the metallurgical properties of a metal part.
- Materials and Methods. Meeting the heat treating needs of the aerospace industry requires the ability to treat multiple materials and use variety of heat treatment methods.
- Contact the Heat Treating Experts. ...
Why heat treat for aerospace applications?
To enhance strength and meet the precise demands and specifications required by aerospace applications, heat treating is an essential step in the production process. For more than a decade, Jones Metal Products has been a go-to source for aerospace industry heat treating.
What are the benefits of heat treating?
In addition to increasing the strength of a metal part, heat treating can also be used to improve machining, improve formability, or restore ductility after a cold forming operation, such as hydroforming services , block forming , fluid cell forming, or deep draw stamping.
What is the best book on heat treating aluminum 7075-t73?
Bates, C.E., "Quench Factor-Strength Relationships in 7075-T73 Aluminum" Southern Research Institute 1 (1987). [23] Wilm, A., Metallurgie,8(1911) 225. [24] Totten, .E., GHandbook of Quenching and Quenching Technology (ASM: Metals Park OH) 1987. Title ASM Heat Treating Aluminum for Aerospace Applications.PDF Author smackenzie Created Date
What are the common defects in heat treatment?
Solution heat treating defects include oxidation, incipient melting and under-heating. Defects occurring during quenching are typically distortion or inadequate properties caused by a slow quench, resulting in precipitation during quenching, and inadequate supersaturation.
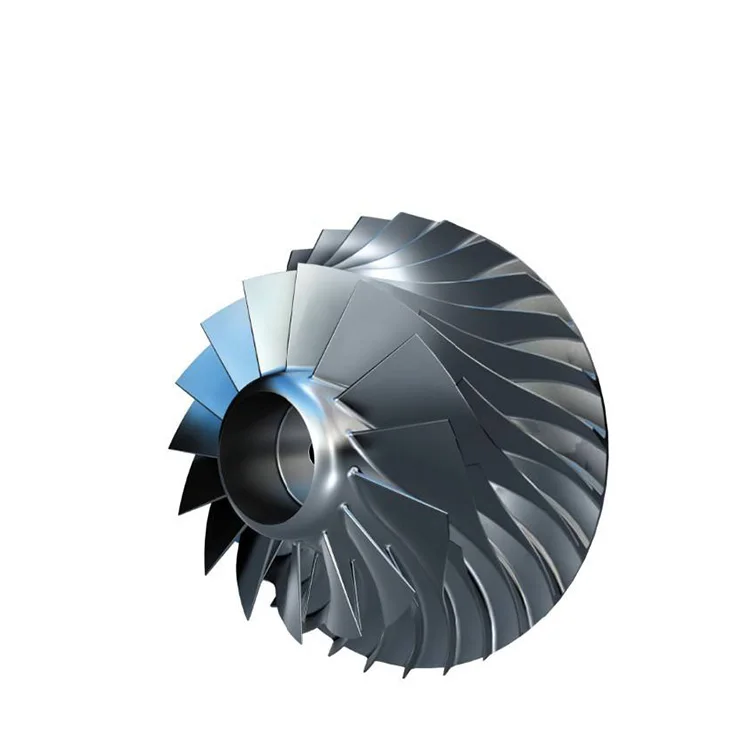
What is heat treatment?
Heat treatment is the process of heating metal without letting it reach its molten, or melting, stage, and then cooling the metal in a controlled way to select desired mechanical properties. Heat treatment is used to either make metal stronger or more malleable, more resistant to abrasion or more ductile.
Why heat treatment is necessary for an aerospace component?
Vacuum heat treatment of aerospace alloys. Complex aerospace components require complex heat treatments. Vacuum furnaces are ideal for hardening and strengthening aerospace components because: Parts cannot oxidize or become otherwise contaminated when atmosphere is removed from the chamber.
What is heat treatment in casting?
Heat treatment, which involves putting the casting through one or more thermal cycles, allows you to manipulate the grains and alter these properties. Heat treatment is carried out in a highly controlled manner in specialised furnaces to ensure that the casting retains its original shape without cracking.
What are the two types of heat treatment?
What are the 4 Types of Heat Treating Processes? Common types of heat treating methods include annealing, hardening, quenching, and stress relieving, each of which has its own unique process to produce different results.
What are the benefits of heat treatment?
WHAT ARE THE BENEFITS OF HEAT TREATMENT?It can change a material's physical (mechanical) properties and it aids in other manufacturing steps.It relieves stresses, making the part easier to machine or weld.Increases strength, making the material ductile or more flexible.More items...•
What is heat treatment and types?
Heat treatment involves the use of heating or chilling, normally to extreme temperatures, to achieve the desired result such as hardening or softening of a material. Heat treatment techniques include annealing, case hardening, precipitation strengthening, tempering, carburizing, normalizing and quenching.
What is tempering and annealing?
Annealing involves heating steel to a specified temperature and then cooling at a very slow and controlled rate, whereas tempering involves heating the metal to a precise temperature below the critical point, and is often done in air, vacuum or inert atmospheres.
How does heat treatment affect strength?
Grain characteristics are controlled to produce different levels of hardness and tensile strength. Generally, the faster a metal is cooled, the smaller the grain sizes will be. This will make the metal harder. As hardness and tensile strength increase in heat-treated steel, toughness and ductility decrease.
What is annealing heat treatment process?
annealing, treatment of a metal or alloy by heating to a predetermined temperature, holding for a certain time, and then cooling to room temperature to improve ductility and reduce brittleness.
What are the 3 stages of heat treatment process?
The stages of the heat treatment process include heating, soaking, and cooling.Heating: Heating is the first stage in a heat-treating process. ... Soaking: Soaking is the stage at which the complete part of the heated metal completely changes in its structure. ... Cooling: The third stage of heat treatment is cooling.
What are the three main methods of heat treatment?
The 4 Types of Heat Treatment Steel UndergoesHeat Treatment Steel: Annealing.Heat Treatment Steel: Normalizing.Heat Treatment Steel: Hardening.Heat Treatment Steel: Tempering.
When to use furnace brazing?
Furnace brazing is commonly used when large batches of parts are to be processed at one time. We provide a reducing atmosphere to help you produce higher quality joints, with controlled heat temperatures and improved production rates.
What is annealing steel?
Annealing. Annealing is the process of heating steel above the transformation temperature and slowly cooling it to increase the workability of the metal. Nitrogen or hydrogen-based atmospheres are also required to achieve a bright annealed surface finish. Learn more about annealing.
What is heat treating in aerospace?
Aerospace heat treating includes the processing of materials such as titanium, aluminum, and high-alloy steels as well as composites, ceramics, carbon/carbon, and other high-strength, lightweight materials. Many aerospace heat treat processes take place in a vacuum due to the need to protect the metal alloys from damaging oxygen, nitrogen, or hydrogen. If not in vacuum, processes are typically carried out under highly protective atmosphere gases. Heat treating processes including annealing, degassing, brazing, nitriding, normalizing, and stress relieving to name a few. Below is a collection of aerospace related news and technical articles.
What is aerospace heat treatment?
Aerospace heat treating includes the processing of materials such as titanium, aluminum, and high-alloy steels as well as composites, ceramics, carbon/carbon, and other high-strength, lightweight materials.
Why do heat treat processes take place in vacuum?
Many aerospace heat treat processes take place in a vacuum due to the need to protect the metal alloys from damaging oxygen, nitrogen, or hydrogen. If not in vacuum, processes are typically carried out under highly protective atmosphere gases.
What is solution heat treatment?
Solution heat treatment is a complicated process. Overheating and underheating can cause a loss in tensile strength, fracture toughness, and ductility. Precipitation heat treatments – Precipitation heat treatments provide hardening by precipitation constituents from solid solution.
What is the process of annealing aluminum?
Annealing – Annealing is a process used to relieve stresses, to stabilize properties and dimensions, to increase ductility, and to soften strain-hardened and heat treated superalloys — but at a loss of strength.
How does age hardening work?
Age hardening – Age hardening can be achieved in two ways: naturally and artificially. Natural age hardening refers to the hardening that occurs naturally after quenching. The degree of hardening depends on the alloy. Artificial age hardening refers to the process of reheating quenched materials to around 212 degrees Fahrenheit ...
What is heat treated bolt?
Heat treated bolts are put through one of the following processes to achieve optimal performance in their given applications: Quenching – Quenching can be called the most essential step in heat treatment. It is designed to create a super-saturated solid solution at room temperature.
What is aerospace bolt?
Aerospace bolts are one of the most critical components in any aircraft, rotorcraft or spacecraft. They must meet incredibly demanding requirements in order to perform in such extreme environments.We create aerospace bolts from many superalloys and exotic materials.
Is aluminum alloy heat treated?
Numerous aluminum alloys exist, and some like aluminum 7075 are nearly as strong as steel. All aluminum alloys are classified as either heat treatable or not heat treatable. Heat treated bolts are put through one of the following processes ...
What is the primary material used in aerospace?
Aluminum has been used in the aerospace industry since the original Wright Flyer. While there have been inroads made by composites and plastics, the primary structural material for aerospace is heat treated aluminum. In this paper, a brief overview of the application of aluminum to aerospace will be discussed.
Why is aluminum used in aircraft?
Aluminum in many forms has been used in aircraft since the early beginning. This is because aluminum alloys can be heat-treated to relatively high strengths, while maintaining low weight.
What alloys harden at room temperature?
Some heat treatable alloys, especially 2XXX alloys, harden appreciably at room temperature to produce the useful tempers T3 and T4. These alloys that have been naturally aged to the T3 or T4 tempers, exhibit high ratios of ultimate tensile strength/yield strength.
What is controlled precipitation of the solute in finely dispersed particles at room temperature?
Controlled precipitation of the solute in finely dispersed particles at room temperature (natural aging) or at elevated temperatures (artificial aging) is used to develop the optimized mechanical and corrosion properties of these alloys.
What is sheet used for?
Some extrusions of 2024, and 2014 are also used. Sheet, both clad and non-clad sheet of 2024, 7475 and 7075 is used for wing and fuselage skins. Sheet is also formed and built-up to form bulkheads and other structural requirements. For heavy used, particularly in military aircraft.
Is aluminum a heat treatable material?
Aluminum alloys are classified as either heat treatable or not heat treatable, depending on whether the alloy responds to precipitation hardening. In the heat treatable alloy systems like 7XXX, 6XXX, and 2XXX, the alloying elements show greater solubility at elevated temperatures than at room temperature.
