Check the + 24 Volts DC Supply of the Flame Detector between + and – terminal of the Flame Detector. Take UV / IR Testing Torch for testing of Flame Detector. Before applying UV / IR rays to the Flame Detector, clean the detectors display by cotton cloth.
Full Answer
What are the disadvantages of a flame test?
repeatability of a flame test means that the scientist carrying out the test can be more confident in the results that they observe. Disadvantages: o Basic flame tests rely upon the individual scientist to observe the colours produced (they are subjective). Therefore, the results for one
How do you improve the results of a flame test?
Well, there are 3 points to it :
- Platinum doesn't impart any color to the flame.
- It is not oxidised under the high temperature of the flame from a bunsen burner.
- It is almost chemically inert. Even at high temperatures, it remains unattacked by free radicals / acid radicals.
What are the practical applications of flame test?
Flame tests use simple equipment, making them ideal for fieldwork. Geologists use the flame test to identify the presence of metals. Forensic scientists can use flame tests at crime scenes for quick analysis of elements present. Miners use the test for analysis of samples, particularly when prospecting. Flame tests provide a good teaching tool ...
How can you identify an unknown using a flame test?
the color that we can see with our naked eye can help us to identify the wavelength of light produced. We will then identify an unknown element by comparing the color of the unknown with the flame color of our known samples. If you miss anything, additional information and a virtual flame test can be found
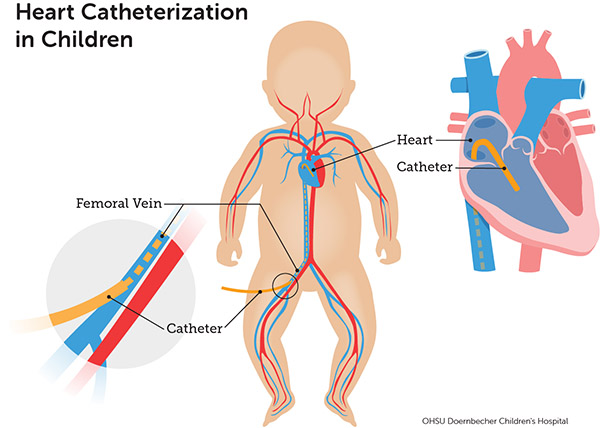
How long does flame treatment last?
A Flame Treating process consists of exposing the surface to a suitable oxidizing flame for a period in the range 0.2 to 3.0 seconds.
How does flame treatment work?
Flame treatment uses a carefully controlled blend of natural gas and air to create a hot, oxygen rich plasma. First, the heat removes contaminants. Then, after contaminant removal, the oxygen rich plasma activates the surface by partial oxidation.
How do you treat a flame?
1:403:38Flame Treatment Updated - YouTubeYouTubeStart of suggested clipEnd of suggested clipCool before proceeding. Test the effectiveness of your flame treatment of the surface by wetting itMoreCool before proceeding. Test the effectiveness of your flame treatment of the surface by wetting it with water if the water beads up like on a freshly waxed. Car the treatment was not effective.
How do you flame treat polypropylene?
To flame-treat the plastic, hold a propane torch about 15cm above the surface so that the flame just touches the plastic. Move it across the surface very quickly, at a rate of about 30-40cm per second.
Why are bottles flame treated?
Flame Treating is the most commonly used means of rendering a molded bottle surface receptive to suitable inks, paints, etc. In this method, a hot oxidizing flame (2000 degrees to 5000 degrees) is applied directly to the intended label or decorated area.
How do you flame treat plastic?
Flame Treating Plastic to Improve Adhesion Flame treatment is applying the exhaust from a gas flame to the surface of a material to improve adhesion. To flame treat a plastic surface, hold a propane torch so the flame just touches the surface and move it across the surface at a rate of 12 to 16 inches per second.
Flame treatment
Flame treatment is a method of treating the surface of a material, making it possible in particular to paint specific surfaces, such as vehicles. It involves using a burner that produces a suitable flame that allows better adhesion of the coating that is applied.
How does flame treatment work?
The burner used for flame treatment produces a gas flame with excess oxygen which is directed onto the material to be treated for a short time. This treatment causes the molecular connection to break down and allows the active ions present in the flame to be bound to the surface.
The characteristics of the flame
The objective is to produce a very different flame from that of a blowtorch which is too hot and too concentrated. A specific torch type burner with a round or triangular shape that uses propane or butane should be used.
What are the uses of flame treatments
Flame treatment can be adapted to many functions ranging from very small objects, such as a perfume bottle, to large areas in the building industry or in car bodywork.
The implementation of flame treatment
Flame treatment requires the adjustment of several parameters depending on the parts to be treated: distance from the sample to the base of the flame, number of passes, speed of the sample under the flame, nature of the gas (air/propane or air/methane), as well as the temperature setting.
What is a laminar flame?
A laminar flame (which is ordinarily employed by flame treaters) is defined as a mixture of a fuel and an oxidiser, thoroughly premixed before combustion. The term ‘premixed laminar flame’ is interchangeable with the term ‘deflagration’ to indicate the propagation of the combustion process accompanied by a decrease in both density and pressure together with an increase in velocity (contrary to the propagation known as ‘detonation’). Within a laminar flame profile, three main zones can be observed ( Fig. 2 ), which correspond to specific reactions. As a consequence, different thermal gradients and reactive species can be encountered. These zones are briefly described here.
What is the molar ratio of a gas to an oxidizer?
The molar ratio of the fuel to the oxidiser is probably the most important parameter within the flame treatment process. For this reason, particular care must be paid to setting it adequately before the flame treatment is started. For each gas there exists a specific and well-defined amount of oxidiser at which the fuel is completely burnt. This precise ratio is known as the stoichiometric ratio, which relies on the chemical structure of the gas. For example, the stoichiometric ratio methane/air by mass is equal to 1:17.2, whereas for a propane/air flame it is 1:15.5, i.e., 15.5 kg of air is needed for the complete combustion of 1 kg of propane. However, in practical applications it is unlikely that the stoichiometric ratio can be verified. Most probably, the flame obtained will be below or above this value. Therefore, the concept of the equivalence ratio ( ϕ ), defined as the actual mass gas/air ratio used during treatment divided the stoichiometric fuel-to-oxidiser ratio [43], is widely accepted: (28) ϕ = m fuel / m oxidizer ( m fuel / m oxidizer) stoichiometric where m is the mass. The most common parameter is the reciprocal of the equivalence ratio, which is called the lambda factor and is expressed by the formula: (29) λ = ϕ − 1
What is a flame treater?
For 3D objects, the plant typically consists of ( Fig. 5 a ):#N#(1)#N#a conveyor belt, which allows a continuous loop of material, i.e., the polyolefin objects, which are normally mounted on heat-resistant holders;#N#(2)#N#a cleaning device, such as a stream of compressed air or a brush-like system. This is normally placed a few centimetres in front of the burners to assure the removal of all small particles (e.g., dust) that might negatively affect successful flame treatment; and#N#(3)#N#a burner, i.e., the basic part of the equipment that produces the oxidising flame.
What is the gap between a flame and a web surface?
It is widely recognised that the gap between the flame and web surface (i.e., the distance between the tips of the luminous flame cones and polyolefin surface) is a key factor in determining the extent of activation accomplished by the treatment. As a general trend, it has been observed that when the film passes through the flame, a rapid depletion in the wettability of the treated surface occurs. As the distance between the cone of the flame and film surface increases, surface activation decreases, although a beneficial effect arising from the treatment is still appreciable up to approximately 20 mm.
What are surface properties?
Surface properties play a pivotal role in defining the performance of materials . Among these properties, wettability and adhesion are sought after in several industrial fields such as automotive, aerospace, building, engineering, biomedical, and biomaterials [1]. For this reason, they have been extensively studied by different branches of science such as polymer chemistry, physics, and rheology. Adhesion and wettability are of critical importance for polymers intended for packaging applications, since they can greatly affect relevant and practical attributes such as the printability of a film, the strength of a laminate, and the anti-fog property of boxes, as well as the processability, convertibility, recyclability, and biodegradability of the final materials. Worldwide attention has long been focused on those applications requiring the deposition of a layer or coating (e.g., adhesives, paints, and varnishes) onto a polymeric substrate, especially when the adhesion at their interfaces is difficult to accomplish due to the inherent chemical surface differences of the two contacting polymers. As a consequence, the establishment of both interatomic and intermolecular interactions governing the adhesion phenomenon at the substrate/coating interface is totally frustrated [2]. To make these surfaces prone to printing and coating processes, different strategies have been developed including using an adhesion promoter (e.g., chlorinated polyolefin, CPO) [3], blending ethylene-propylene rubber to form thermoplastic polyolefin (TPO) [4], and exploiting physical-chemical phenomena at the base of plasma [5], corona [6], laser [7], and flame treatments [8]. Although all of them have been suggested as suitable approaches for enhancing polymer adhesion strength, which is the most effective and feasible one is still the subject of debate [9]. However, it is generally agreed that flame treatment, together with corona discharge, is the most widely used for the surface activation of polyolefin substrates [10].
What is the formula for polyolefins?
The term polyolefin encompasses all those polymers produced by an olefin as a starting monomer, whose general formula is C n H 2n. Most common polyolefins in the packaging field are polyethylene (PE) and PP. Although they have different specific properties, it is recognised that both polymers are inherently hydrophobic, which is in turn responsible for their typical poor wettability, especially to waterborne systems. For this reason, polyolefins generally need to be surface-activated before the deposition of inks, paints, adhesives, metals, and coatings. Flame treatment is a valuable technique to improve the surface energy of polyolefins, although it has been exploited to a minor extent with respect to corona treatment so far. However, because of improvements in safety conditions as well as in some technical aspects, it is receiving renewed attention, especially by those sectors (e.g., packaging) that historically lagged behind in the exploitation of the technique.
What is the coldest region of a flame?
This region, also called the ‘dark zone’, has a typical dark bluish colour. It is the coldest region of a flame because even though some of the hydrogen formed is oxidised to water the combustion process has not yet reached the explosion condition, and thereby the amount of net energy released is negligible. In this region, the only abundant free radical is the hydrogen atom, which reacts quickly with hydrocarbons and oxygen, thereby impeding the formation of the radical pool. For this reason, this zone is also known as the ‘reducing zone’. This is an ineffective and unimportant region for surface activation purposes, since it in no way contributes to the oxidation of the plastic substrate.
