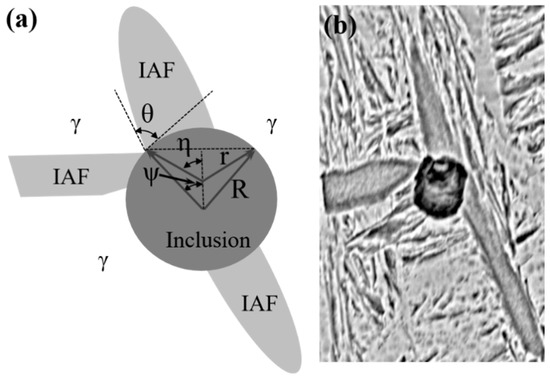
Heat treatments are useful methods to change the matrix microstructure for the improvement of impact toughness and wear resistance for numerous cast iron materials. These treatments provide relatively few benefits in improving the impact toughness of the HCCI with even larger amount of hard consecutive eutectic chromium carbides [ 8 ].
Does heat treatment affect mechanical properties and microstructure change of selected specimen?
In this study EN 31, EN 24 and EN 8 (alloy steel) are selected as specimens for testing various mechanical properties and microstructure change. The effects of heat treatment on the mechanical properties and microstructure characteristics change of selected specimen are analyzed.
Do heat treatments affect ODS steel microstructure?
Microstructure Differences Induced by Heat Treatments Various heat treatment conditions including temperature and cooling rate usually affect the microstructure and mechanical properties of ODS steels. In this study, 10Cr and 12Cr dual phase ODS steels mainly underwent three kinds of heat treatment.
What are the mechanical properties of heat treatment?
The heat treatment develops hardness, softness , and improves the mechanical properties such as tensile strength, yield strength, ductility, corrosion resistance and creep rupture. These processes also help to improve machining effect, and make them versatile. How does heat treatment affect mechanical properties?
What are the advantages of heat treatment in machining?
The heat treatment develops hardness, softness, and improves the mechanical properties such as tensile strength, yield strength, ductility, corrosion resistance and creep rupture. These processes also help to improve machining effect, and make them versatile.
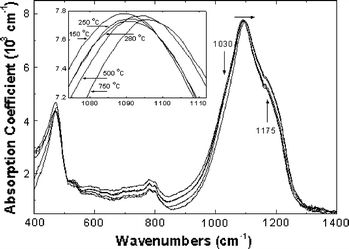
How does heat treatment change microstructure?
1:403:32Effects of Heat Treatment on the Microstructure and Mechanical ...YouTubeStart of suggested clipEnd of suggested clipWhen the specimen is subjected to an ailing process the ferrite grains undergo completeMoreWhen the specimen is subjected to an ailing process the ferrite grains undergo complete recrystallization due to the slow cooling in annealing austenite is transformed to soft pearlite.
What effect does heat treatment have on steel microstructure?
This is due to the formation of huge amounts of martensite, from austenite, as observed in the microstructure. Tempering after heat treatment of EN 8 steel always leads to a reduction in hardness. The reduction in surface hardness is the most in normalizing (almost 48%), while it is the least in annealing (17%).
What happens to the microstructure during tempering?
Changes in Martensite Structure The martensite itself also changes during tempering. One change that occurs is that the “tetragonality” of the martensite is reduced as the martensite becomes more and more like cubic ferrite as the carbon leaves the martensite.
How does heat affect grain structure?
Grains in metals tend to grow larger as the metal is heated. A grain can grow larger by atoms migrating from another grain that may eventually disappear. Dislocations cannot cross grain boundaries easily, so the size of grains determines how easily the dislocations can move.
What happens to the microstructure during annealing?
Annealing is a heat treatment process which alters the microstructure of a material to change its mechanical or electrical properties. Typically, in steels, annealing is used to reduce hardness, increase ductility and help eliminate internal stresses.
How does heat treatment affect steel?
Heat Treating of steel and other metals can lead to: Improved wear resistance. Increased resistance to deformation and warpage and. Increased strength or toughness.
Does tempering change the microstructure?
As the last process of heat treatment, the tempering process can significantly affect both the microstructure and the mechanical properties of the steel, including the recovery of martensitic lath, reduction of dislocation density, reduction of hardness and yield strength, etc.
What does tempering do to metal structure?
tempering, in metallurgy, process of improving the characteristics of a metal, especially steel, by heating it to a high temperature, though below the melting point, then cooling it, usually in air. The process has the effect of toughening by lessening brittleness and reducing internal stresses.
What happened to the grain structure after quenching process?
After the metal is heated, we need to rapidly cool the steel. As material is quenched, the austenitic grain structure created during the heating stage transforms to different grain structures such as martensite, ferrite, pearlite, and cementite.
How does temperature affect grain size?
Yes, the grain size increases with increasing the annealing temperature. This is because increasing the annealing temp. leads to increase the crystallinity of the material and hence increases the number of crystallites.
How heat treatment can change the properties of metals?
The temperatures metals are heated to, and the rate of cooling after heat treatment can significantly change metal's properties. The most common reasons that metals undergo heat treatment are to improve their strength, hardness, toughness, ductility, and corrosion resistance.
What happens to structure of metals when they are heated and how is this related to corrosion?
Metal expands when heated. Length, surface area and volume will increase with temperature. The scientific term for this is thermal expansion. The degree of thermal expansion varies with different types of metal.
What is the hardness of a martensitic microstructure?
The hardness values are characteristic for a martensitic microstructure. With increasing austenitizing temperature the hardness is rising from 648 (for 1000°) to 754 HV1 after an austenitization at 1100 °C due to the increasing amount of dissolved carbon and chromium in the lattice matrix. A higher ratio of dissolved carbides cause a higher effect of strengthening because of solid solution.
How does tempering affect stainless steel?
Stainless steels are widely used in engineering, where corrosion resistance is mandatory. Quenching and tempering is a well-known procedure to improve the hardness of stainless steel by several micro structure changes. The effect of austenitizing temperature on the mechanical properties is well understood – the dissolution of carbides at high temperatures leads to a higher amount of carbon in the crystal structure and thus to a distortion of the lattice structure. This distortion results in the tetragonal body centered martensite structure. 1 1. A. F. Candelaria and C. E. Pinedo, “Influence of the heat treatment on the corrosion resistance of the martensitic stainless steel type AISI 420,” J. Mater. Sci. 22, 1151–1153 (2003). https://doi.org/10.1023/a:1025179128333
How does austenitizing affect corrosion?
The dissolution of chrome carbides increases the amount of dissolved chrome and carbon. On the one hand, a higher chrome content leads to a passive layer richer in chrome as well and thus to a better corrosion resistance. 5,6 5. R. F. Steigerwald, “The corrosion behavior of some Fe-Cr alloys,” Metall. Trans. 5, 2265–2269 (1974). https://doi.org/10.1007/BF02644005 6. C. Pallotta, N. De Cristofano, R. C. Salvarezza, and A. J. Arvia, “The influence of temperature and the role of chromium in the passive layer in relation to pitting corrosion of 316 stainless steel in NaCl solution,” Electrochim. Acta 31, 1265–1270 (1986). https://doi.org/10.1016/0013-4686 (86)80146-3 On the other hand, a higher carbon content results in lattice distortion which can lead to a more defective passive layer. 1 1. A. F. Candelaria and C. E. Pinedo, “Influence of the heat treatment on the corrosion resistance of the martensitic stainless steel type AISI 420,” J. Mater. Sci. 22, 1151–1153 (2003). https://doi.org/10.1023/a:1025179128333
How does pitting potential decrease with increasing austenitizing temperature?
The pitting potential decreases with increasing austenitizing temperature (for sample T0 and T = 1000 °C–1100 °C) because of an increase of internal lattice stress due to higher carbon content. A further increase of the austenitizing temperature (1150 °C and 1200 °C) does not increase the carbon content since all carbides are dissolved; instead it enhances the grain size. With increasing grain size, lattice defects due to grain boundaries decrease and the material shows less starting points for pitting corrosion and a higher Epit, while on the other hand the corrosion rate seems to increase.
What happens to stainless steel after austenitizing?
Austenitizing of stainless steel results in different microstructure changes, namely the release of chromium from carbides to the alloy matrix, the release of carbon to the alloy matrix and the growth of grains. The right choice of cooling phase after austenitizing leads to martensite microstructure which shows significant improvements in hardness.
How long does it take for chromium carbide to dissolve in steel?
It should be noted that ThermoCalc calculations are based on the assumption of equilibrium conditions. After 2 hours of austenitization all carbides that dissolve at the given temperature are dissolved. Considering this the phases should be in equilibrium but as the chromium atom is slow, a complete homogenization is not given even after hours.
What temperature is used to austenitize chromium carbides?
Besides, a nearly complete homogenization of the dissolved elements in the material matrix occurs. High austenitizing temperatures T A are often needed to dissolve precipitates. For chromium carbides the needed temperatures are 930 °C for Cr 23 C 6 and 1120 °C for Cr 7 C 3. 16 16. K. Bungardt, E. Kunze, and E. Horn, “Untersuchungen über den aufbau des systems eisen-chrom-kohlenstoff,” Arch. Eisenhüttenwes. 29, 193–203 (1958). https://doi.org/10.1002/srin.195802238 At these temperatures the chromium and carbon elements dissolve in the matrix lattice of austenite. Thus, this thermal energy is necessary to develop the hardenability-enhancing effect.
How does heating and cooling affect the microstructure of steel?
The heating and cooling treatment of the steel specimens have a great effect on the phase of the microstructure of the steel specimen. The addition of alloys or coarsening of the austenitic grain structure increase the hardenability of steel.
What is the purpose of heat treating steel?
The purpose of heat treating is to analyze the mechanical properties of the steel, usually ductility, hardness, Yield strength, tensile strength and impact resistance. The heat treatment develops hardness, softness, and improves the mechanical properties such as tensile strength, yield strength, ductility, corrosion resistance and creep rupture.
How does hardenability affect steel?
Hardenability is used to describe the ability of an alloy to be hardened by the formation of martensite as a result of a given heat treatment. One standard procedure that is widely utilized to determine hardenability is the Jominy end quench test. The heating and cooling treatment of the steel specimens have a great effect on the phase of the microstructure of the steel specimen. The addition of alloys or coarsening of the austenitic grain structure increase the hardenability of steel. Any steel that has low critical cooling rate will harden deeper than one that has a high cooling rate of quenching. The size of the part that is being quenched has a direct effect upon the hardenability of the materialThe jominy test was performed as per the instructions using jominy test specimens of different samples of EN8, EN24 and EN31 steel. The specimens were heated in muffle furnace as per the instructions and quenched with water The hardness of the samples of Jominey test was measured as a function of the distance from the quenched end to demonstrate the different hardenability of the two steels with Vicker Hardnessl machine. The results are plotted in the graph as shown in Fig. 6, Fig. 7, Fig. 8 .The alloy steel EN 31 clearly has the highest hardenability, forming martensite to a greater depth than EN 8 and EN 24. High hardness occurs where high volume fractions of martensite develop. Lower hardness indicates transformation to bainite or ferrite/pearlite microstructures. As the distance from quenched end increases, the percentage of martensite decreases. It is because of difference in the cooling rate.
Why is annealing harder than normalizing?
The function of hardening is to increase the hardness of the specimen and so its Vicker Hardness number is larger than annealing and normalizing because here carbon cannot get more time to react with oxygen (for quick cooling rate), so carbon is trapped with the specimen and formed martensite. But in annealing process, carbon particles get enough time to react with oxygen due to slow cooling rate. It resulted in formation of pearlite and ferrite phases in steel specimens. Normalizing does not soften the steel to the extent it is done by annealing and also it does not restore ductility as much as is done by annealing. Its Vicker Hardness Number is less than hardening but greater than annealing.
What is the purpose of mechanical testing?
Mechanical tests are also employed in investigational work in order to obtain data for use in design to ascertain whether the material meets the specifications for its intended use. Heat treatment is defined as an operation or combination of operations involving heating and cooling of a metal or alloy for this case involving the mild steel in the solid state in such ways as to produce certain microstructure and desired mechanical properties (hardness, toughness, yield strength, ultimate tensile strength, Young’s modulus, percentage elongation and percentage reduction). Annealing, normalizing, hardening and tempering are the most important heat treatments often used to modify the microstructure and mechanical properties of engineering materials particularly steels. Annealing is defined as a heat treatment that consists of heating to and holding at a suitable temperature followed by cooling at an appropriate rate, most frequently applied in order to soften iron or steel materials and refines its grains due to ferrite-pearlite microstructure; it is used where elongations and appreciable level of tensile strength are required in engineering materials. Hardening is the heat treatment processes in which increases the hardness of a steel piece by heating it to a certain temperature and then cooling it rapidly to room temperature. Tempering is the process of imparting toughness at the cost of its hardness to an already hardened piece of steel by reheating it to a certain temperature and then cooling it rapidly. The temperature of heating depends on the toughness to be imparted and hardness to be reduced. In normalizing, the material is heated to the austenitic temperature range and this is followed by air cooling. This treatment is usually carried out to obtain a mainly pearlite matrix, which results into strength and hardness higher than in as received condition. It is also used to remove undesirable free carbide present in the as-received sample [1]. Steel is an alloy of iron with definite percentage of carbon ranges from 0.15 to 1.5% [2], plain carbon steels are those containing 0.1–0.25%.Steel is mainly an alloy of iron and carbon, where other elements are present in quantities too small to affect the properties. The other alloying elements allowed in plain-carbon steel are manganese and silicon. Steel with low carbon content has the same properties as iron, soft but easily formed [3]. Prediction of microstructure transformations is prerequisite for successful prediction of mechanical properties after a heat treatment and of generation of stresses and strains during a heat treatment. Phase transformation modeling is one of the main challenges in modeling of heat treatment [4]. During annealing, softening processes are under way in the microstructure and, in some cases, recovery and recrystallization take place as well. Naturally, the morphology of carbides changes as well [5]. In the present paper, microstructure and mechanical properties of EN31, EN 24 and EN8, under heat treatments such as annealing, normalizing and hardening has been investigated.
How long did the specimen stay in the furnace?
For normalizing: In this case the specimen was put in the furnace for 910 °C and we kept it in this situation for approximately 70 min. After that it was cooled in room temperature (Air).
Can mechanical properties be modified?
The mechanical properties can easily be modified by heat treating to suit a particular design purpose. In the present study, selected samples are heat-treated at certain temperature above the austenitic region and quenched in order to investigate the effect on the mechanical properties and microstructure of the steel.
Abstract
High chromium cast iron (HCCI) is taken as material of coal water slurry pump impeller, but it is susceptible to produce serious abrasive wear and erosion wear because of souring of hard coal particles.
Author information
Key Laboratory of Pressure Systems and Safety of Ministry of Education, East China University of Science and Technology, Shanghai, 200237, China
Additional information
Supported by National Hi-tech Research and Development Program of China (863 Program, Grant No. 2013BAF01B01)
What is the microstructure of low carbon steel?
The microstructure of a new low carbon HSLA steel with a high tensile strength and a high toughness in the as-hot forged condition for automotive parts was observed in detail in an 0.12% C-2% Mn-1% Cr-0.25% Mo-0.12% Nb-0.021% Ti-0.0018% B steel. Lath-like microstructure observed at the cooling rate ranging from 250 to 6°C/s mainly was revealed to consist of bainitic-ferrite with retained austenite and auto-tempered martensite. Granular microstructure observed at the cooling rate ranging from 0.17 to 0.04°C/s was characterized to be martensite-austenite constituent islands in featureless matrix. This microstructure is considered to be formed the following process. The neighboring laths of bainitic ferrite coalesced and the length of untransformed austenite shortened and consequently its shape became to resemble islands during slow cooling. Toughness of granular microstructure was lowered by twinned martensite in islands and no boundaries in packets compared with lath-like microstructure. Toughness of the low carbon HSLA steel with as-transformed martensite and bainite microstructure is equivalent or superior to that of conventional medium carbon steels.
What temperature to austenitize steel?
4340 steel bars were austenitized at 850°C for 1h followed by heating at 700°C for 90min and quenching into a salt bath at the temperature range of 300–450°C for 1h to obtain dual structures with 34vol.% fraction ferrite and various bainite morphologies. SEM studies showed that by increasing the austempering temperature, bainite morphology varies from lower to upper bainite. Tensile, impact and hardness tests revealed that increasing the austempering temperature from 300 to 400°C leads to a reduction in yield and ultimate tensile strength, hardness, uniform and total elongation and impact energy. But in dual phase steel produced by austempering at 450°C, yield and tensile strength and hardness increased and severe reduction in total elongation and impact energy obtained. Fractography of tensile specimens showed brittle behavior for this austempering temperature. Fatigue test results showed that fatigue limit decreases with increasing austempering temperature from 300 to 400°C. Finally, fractography studies showed cleavage fracture at the surface of fatigue specimens austempered at 400°C, which confirms the tendency to brittle behavior.
What is HSLA steel?
With rapid development of national economy,high strength low alloy (HSLA) steel plates have been extensively used in fields of engineering machinery,coal mine machinery,port machinery and so on. HSLA steel should possess not only enough strength and hardness but also excellent toughness and forming property in order to make the machine large scale, lightweight and high parameter. And in recent years, with the new modern plate heat treatment lines pulling into production, the production conditions of high-strength steel plates have been improved significantly, and the development of HSLA steel has attracted more and more attentions. In this paper, taking Q690 high strength steel as the research object, the effects of intercritical heat treatment and quenched-tempered process on microstructure and mechanical properties were investigated. The results show that the impact toughness of test steel with prior microstructure containing plenty of massive ferrite can be deteriorated while the intercritical quenching temperature was 810°C. However, by the same intercritical heat treatment, the final microstructure of test steel with prior lath martensite structure consists of much finer martensite and acicular ferrite existed among martensite phase. The Charpy impact energy at - 40°C reaches 247 J,but the strength is much lower. The excellent comprehensive mechanical properties can be obtained by quenching and tempering heat treatment. Based on the test results,in addition, the effect mechanism of various quenching condition on low temperature impact toughness was analyzed.
What furnace is used to make corundum crucibles?
in a corundum crucible in a vacuum furnace [23]. Before
What is the treatment for st ep?
treatment includes two st ep quenching and tempering.

Abstract
- The variations of microstructure and mechanical properties of a high-chromium cast iron for rolls were studied from as-cast to the final heat treatments. Results show that the as-cast microstructure of the HCCI consists of M7C3 carbide, M23C6 carbide, martensite matrix, and retained austenite. The large dendritic M7C3 carbide surrounds the matrix, ...
Introduction
- High-chromium cast iron (HCCI), as excellent wear-resistant material, has been widely used for hot rolling working roller since the end of the last century [1–4]. The exceptional wear resistance of HCCIs is attributed primarily to the high volume fraction of hard eutectic chromium carbides [5, 6]. The high volume fraction of hard and consecutive eutectic chromium carbides results in a fat…
Materials and Procedures
- The roll is a small wok roll, normally prefabricated by uphill casting a layer of wear-resistant material (HCCI) on the outside surface of the 1045 steel sleeve as the roll sleeve, and then the spindle is installed by means of interference fit. Figure 1 is the casting process schematic representation, the actual picture, and design parameters of roll sleeve. From Figure 1(a), the ca…
Results and Discussion
- Figure 2 shows the XRD patterns of the specimens after different heat treatments. The phases of the HCCI mainly consist of martensite, retained austenite, and chromium carbides of M7C3 (PDF: 17-0333) and M23C6 (PDF: 5-0721) [14]; some differences could also be found in different specimens. For the as-cast specimen, the diffraction peak intensities of retained austenite and …
Conclusions
- (1)The as-cast microstructure of the HCCI consists of M7C3 carbide, M23C6 carbide, and matrix of mixed martensite and retained austenite. During austenization at 1020°C, part of M23C6 carbide transformed to M7C3 carbide and was dissolved in austenite; thus, the amount of M23C6 carbide decreased, whereas that of M7C3 carbide increased. During tempering at 500°C, the mic…
Acknowledgments
- This work is sponsored by Hebei Science and Technology Support Program (13274202D) and Hebei University of Science and Technology Fund (XL201002).