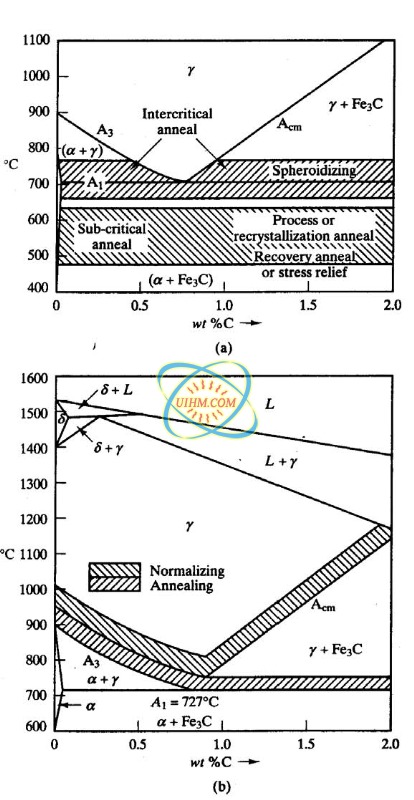
How to heat treatment of H13 hot steel?
The heat treatment of H13 hot steel 1 Forging process. H13 steel contains quite high alloy elements, offering poor thermal conductivity and low eutectic temperature, easy to cause overburning. 2 Spheroidization annealing process. ... 3 Quenching and tempering process. ...
What are the requirements for H-13 heat treatment quality?
This excellent publication provides a very detailed explanation for H-13 heat treatment quality requirements. Heat treating H-13 die steel is divided into four major steps: preheating, austenitizing, quenching and tempering. Each step has a specific function with unique thermal requirements to optimize the steel’s mechanical properties.
How do you anneal H13?
Annealing H13 may be annealed by heating to 1600°F. Soak one hour per inch of greatest thickness, and furnace cool at 30 degrees per hour to 900°F. Then air cool. Proper annealing procedure includes packing in a sealed container, using a neutral inert material. Result, maximum Brinell hardness of 207.
What is the hardness of A H13 steel?
H13 steel has good hardenability, of less than 150 mm thick parts oil quenching to achieve a uniform hardness. But because the steel contains Mn, Si element prone to oxidation and decarbonization.
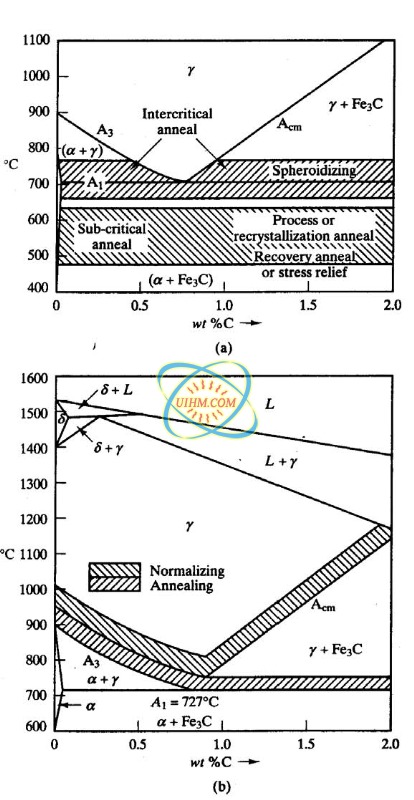
How do you anneal steel in H13?
H13 may be annealed by heating to 1600°F. Soak one hour per inch of greatest thickness, and furnace cool at 30 degrees per hour to 900°F. Then air cool. Proper annealing procedure includes packing in a sealed container, using a neutral inert material.
How do you harden H13 steel?
H13 is a steel having very high hardenability and should be hardened by cooling in still air. The use of a salt bath or controlled atmosphere furnace is desirable to minimize decarburization, and if not available, pack hardening in spent pitch coke is suggested.
Can you temper steel multiple times?
All Answers (3) Induced phase transformation depends on temperature and time. You can repeat simple quenching heat treatment numerous time if sample is austenitized before hand.
How do you anneal tool steel?
So how do you anneal steel? To anneal steel, heat it up about 100 degrees F above its critical temperature, soak it at that temp for 1 hour per inch of thickness, and let it cool at a maximum rate of 70 F per hour. Ok, that's the short answer.
Is H13 air hardening steel?
H-13 is an air hardening, 5% chromium die steel, which is an excellent choice for a wide range of hot work and cold work applications. H-13 is widely used for aluminum, zinc, and magnesium die casting dies where resistance to thermal fatigue due to alternated heating and cooling cycles is of primary importance.
Is H13 air hardened?
Harden: H13 steel has very high hardenability and should be hardened by cooling in air. Use a salt bath or controlled atmosphere furnace to minimize decarburization, or alternatively (if not available) pack hardening in spent pitch coke . The temperature used is typically 1800°-1850°F, depending on size.
Can you anneal multiple times?
In principle, annealing of metallic alloys involves a number of diffusion governed processes having additive character. So, through applying it twice (or more times), the overall effect will be the the same to that obtained through applying a long-time annealing.
What happens if you heat treat steel twice?
The study also found that the ductile-brittle transition temperature was reduced in steel that had been twice tempered. The ductile-brittle transition temperature means the point at which a material goes from ductile, or able to bend and absorb impact, to brittle, or liable to break on impact.
Why do we double temper steel?
Some highly alloyed steels require a double temper to increase toughness and ductility. The change in hardness for plain carbon steels as a function of tempering temperature is shown in Figure 3.
What are the three stages of annealing?
There are three main stages to an annealing process.Recovery stage.Recrystallization stage.Grain growth stage.
What is the annealing temperature?
The temperature range for process annealing ranges from 260 °C (500 °F) to 760 °C (1400 °F), depending on the alloy in question. This process is mainly suited for low-carbon steel. The material is heated up to a temperature just below the lower critical temperature of steel.
What is annealing PDF?
What Is Annealing? Annealing is a heat treatment process in which a metal is heated above its recrystallization temperature, kept at that temperature for some time for homogenization, and then cooled slowly to develop an equilibrium structure.
What is H13 steel?
H13 steel is the American National Standard ANSI steel, the equivalent of China GB / T1299 4Cr5MoSiV1. H13 steel in Cr, Mo, Si, V and other alloying elements [1], shown in Table 1, except Si element does not form carbides, Cr, Mo, V three elements will combine to form special carbides with carbon, these special carbide will improve ...
What is the effect of Mo on steel?
Influence of Mo: Mo is a carbide-forming elements, in H13 steel can improve the steel tempering stability and wear resistance. Influence of Si: increase steel strength, hardness and resistance to tempering, heat treatment furnace at the same time weaken the oxidizing atmosphere. Effect of V: The lower thermal sensitivity ...
Is H13 steel hot?
H13 steel is widely used internationally a hot die steel, because it has a good impact toughness at high temperatures, wear resistance, ductility, hot hardness and applied die casting, forging die and extrusion die manufacturing. This article describes a heat treatment process H13 steel after forging change. 1, The chemical composition of the steel.
Can H13 be used for ball annealing?
H13 alloy elements more change when heated slowly, it can not and should be used with conventional annealing temperature ball annealing, the alloy carbides form a uniform granular material, to give a fine granular pearlite.
What is the process of making H13 steel?
In addition, the manufacture of H13 steel mold has to go through a series of processes such as forging, annealing and machining. Improper operation in each process will cause premature failure of the mold and reduce its service life.
What is H13 steel used for?
The heat treatment of H13 hot steel. H13 is the most commonly used hot work steel, it has higher thermal strength and hardness, wear resistance and toughness, better heat resistance fatigue performance, has been widely used in the manufacture of various forging die, hot extrusion die and aluminum, copper and its alloy casting mold.
What is the purpose of spheroidization annealing?
The purpose of spheroidization annealing is to uniform structure, reduce hardness, improve cutting performance and prepare the structure for quenching and tempering.
What is H13 steel used for?
H13 is one of the most widely used tool steels for both hot and cold work tooling applications. Binder jet additive manufacturing offers the potential to deposit complex tools at scale due to larger powder bed sizes and faster deposition rates. However, to date there is no published literature on the sintering of H13 to full densification. In this paper, we discuss pressureless sintering of binder jet AM H13 steel to full densification via supersolidus liquid phase sintering (SLPS) while discussing appropriate process windows (1360 °C – 1380 °C) for densification without distortion. The process windows have been rationalized based on thermodynamic calculations for liquid volume fractions with temperature. We show that higher binder saturation results in higher carbon retention and subsequently earlier liquid formation that can initiate the sintering process at lower temperatures. We report abnormal grain growth during sintering and found that the solidification phase transformations play a critical role on microstructural evolution and must be considered to accurately model the kinetics of SLPS.
What is AISI H13?
The AISI H13 is a chromium based, medium carbon content hot work tool steel which is widely used in hot working as well as cold working applications. These steels are very popular because of their key characteristics such as high hardness, high strength, high fracture toughness and high wear resistance. These steels are continuously subjected to high mechanical stresses and temperature fluctuations, fatigue and wear loss which results in limited die life. It is therefore necessary to improve the properties of these tool steels. One of the methods to improve the properties of these tool steels is with the help of conventional heat treatment. But no significant improvements in the properties were observed. From the literature survey, it is realized that implementation of cryogenic treatment can improve the properties of tool steel. In the present paper, cryogenic treatment on AISI H13 hot work tool steel is studied with the help of characterization techniques such as hardness, wear and microstructure study. One set of specimens were subjected to conventional heat treatment (HTT) viz. hardening at 1020 °C followed by double tempering at 500 °C. Another set of specimens were subjected to conventional heat treatment followed by deep cryogenic treatment at −196 °C and soft tempering at three different temperatures viz. 200 °C, 300 °C and 400 °C (HTTCT). A modified heat treatment cycle (HTCT) is also proposed with varying soft tempering temperatures viz. 200 °C, 300 °C and 400 °C and comparison is made with HTT and HTTCT. The specimens were tested for hardness, wear and microstructure study. The experimental investigation shows that cryogenically treated specimens shows significant improvement in the hardness and carbide density as compared to conventionally treated specimens. It is thus concluded that HTTCT cycle gives two times higher wear resistance than conventional heat treatment cycle (HTT) because of precipitation of fine tertiary carbides.
What temperature is austenitized?
This paper intends to find out the impact of austenitizing temperature on the wear behaviour of AISI H13 die steel. Austenitizing of H13 steel is done at different temperatures, i.e., 1000 °C, 1020 °C, 1040 °C, 1060 °C and then tempering is done twice at 560 °C for two hours. H13 die steel when tempered after austenitizing at 1020 °C lath martensite of large size is produced. Whereas, quite smaller lath martensitic structure has been observed in H13 die steel tempered after austenitizing at 1060 °C. Wear test investigation carried out using a pin on disc tribometer for H13 steel pins austenitized at different temperatures against D2 steel disc having 61 HRC. It is observed that the wear volume of H13 die steel exhibits an inverse linear relationship with its austenitizing temperature due to an increase in hardness. It is seen that small protective layer like patches of oxidized debris formed on the worn surface of H13 steel austenitized at 1060 °C. Whereas, no such protective layer formation is found on H13 die steel austenitized at a lower temperature. Post wear test, subsurface cross-section study shows plastic deformation of grains just beneath the worn surface along the direction of wear tracks. H13 die steel austenitized at 1060 °C with larger grains shows plastic deformation of grains up to a greater depth. Whereas, H13 die steel austenitized at 1000 °C with finer grain exhibits plastic deformation up to a lesser depth. An increase in grain boundaries of nearly twice is also found below the worn subsurface up to 80 to 100 µm depth. The present study will help to select the austenitizing temperature for H13 die steel to have better wear resistance.
How is H13 steel made?
The H13 steel made by electroslag remelting (ESR) process can effectively improve the low microstructure and den sification of steel, and improve the isotropy of die steel. Compared with ESR process, the furnace refining H13 can save 20% ~ 30% of the production cost, is still the mainstream smelting method. Reasonable forging process and heat ...
Why do you temper H13 steel?
In order to eliminate the stress and improve the high temp toughness of H13 forgings must be tempered at high temperatures, secondary tempering can be used to improve the life of the die due to the good fire resistance and secondary hardening of the alloy elements in the steel.
What is the microstructure after tempering?
The microstructure after tempering is tempered martensite and a small amount of granular carbides. Tempering should be done twice. When tempering at 500℃, the secondary hardening peak appears, with the highest tempering hardness and peak value around 55HRC, but the worst toughness.
What is hot worked die steel?
Hot-working AISI H13 tool steel offers high hardenability, excellent wear resistance and hot toughness, has been widely used in hot forging dies, pressure dies casting tools, extrusion tools, hot shear blades, stamping dies, plastic mold and aluminum alloy die casting dies, is the most commonly used hot-worked die steel. The H13 steel made by electroslag remelting (ESR) process can effectively improve the low microstructure and densification of steel, and improve the isotropy of die steel. Compared with ESR process, the furnace refining H13 can save 20% ~ 30% of the production cost, is still the mainstream smelting method. Reasonable forging process and heat treatment process can improve the quality, performance and service life of H13 steel.
Is H13 steel hardenable?
H13 steel has good hardenability, for H13 forging thickness less than 150 mm, oil quenching can achieve uniform hardness, but it’s easy to cause oxidation and decarburization and other defects deo to Mn, Si elements in the steel. It is recommended to use salt bath, controlled atmosphere heat treatment, vacuum heat treatment or coating ...
How to anneal H13?
H13 may be annealed by heating to 1600°F. Soak one hour per inch of greatest thickness, and furnace cool at 30 degrees per hour to 900°F. Then air cool. Proper annealing procedure includes packing in a sealed container, using a neutral inert material. Result, maximum Brinell hardness of 207.
What is H13 steel?
It is an AISI H13 hot work tool steel, the most widely used steel for aluminum and zinc die casting dies. It is also popular for extrusion press tooling because of its ability to withstand drastic cooling from high operating temperatures.
What is the hardness of H13 steel?
For hot work applications, H13 is used in the hardness range of HRC 38 to 48. The usual hardness range for die casting dies is HRC 44 to 48 requiring a temper at approximately 1100°F. For improved shock resistance, the steel is often tempered at temperatures approaching 1150°F, resulting in hardnesses of HRC 40 to 44. The steel should be held at the tempering temperature for at least two hours per inch of greatest cross section. All hot work steel should be tempered at a minimum of 50 degrees above the expected maximum operating temperature of the tool or die. Double tempering, with the second temper of 25 to 50 degrees lower than the first temper is always advisable, particularly where heat checking is a problem.
Why is heat treatment important?
Heat treatment is the single most important factor in determining performance of the steel. The challenge for the customer is determining whether a proper heat treatment has been performed. By reviewing and understanding the key criteria of a furnace chart, the customer can have confidence in the steel’s delivered performance.
What is the most important factor in determining the performance of die steel?
The single most important factor in determining the performance of die steel is the heat treatment process. To ensure the dies achieve their desired performance, confirming proper heat treatment of the die steel is essential.
What are the three areas that must be verified via the furnace chart?
There are three distinct areas that must be verified via the furnace chart. 1. Pre-heating time and temperatures. 2.
What is the temperature of a workpiece?
Preheat time and temperatures. During the workpiece’s heat up, the core temperature (Tc) should not exceed 400°F/hour. The workpiece should be held at the first preheat temperature until the difference between the surface temperature (Ts) and core temperature (Tc) is less than 200°F. ( See Figure 2.)
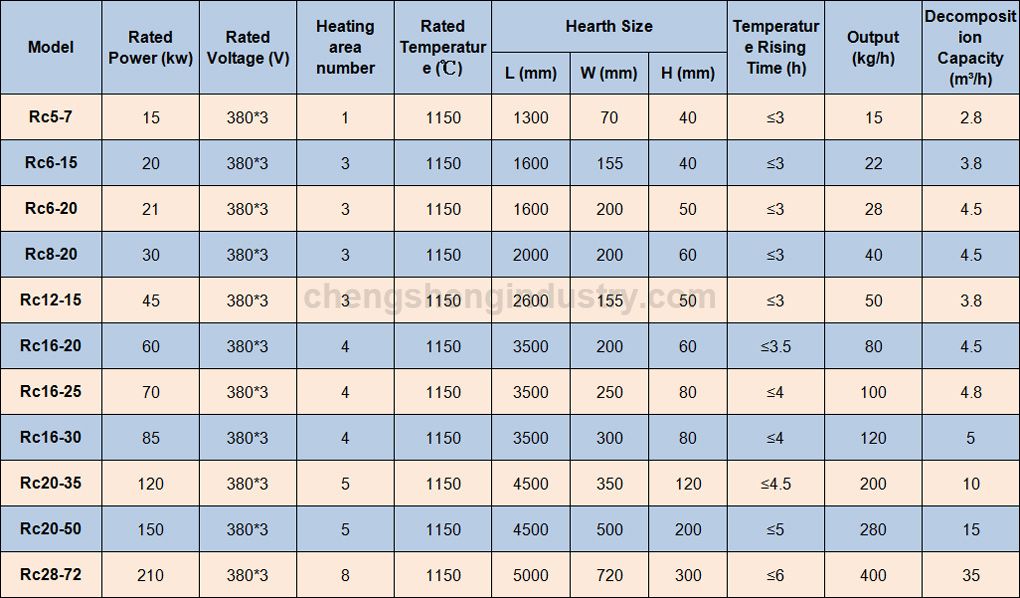