
There are many advantages of heat treatment, including:
- It can change a material’s physical (mechanical) properties and it aids in other manufacturing steps.
- It relieves stresses, making the part easier to machine or weld.
- Increases strength, making the material ductile or more flexible.
- Introduces wear-resistant (hardness) characteristics, either just to the surface or right through the part.
What is heat treatment and why is it used?
Heat treatment in any of its forms is used to achieve a desirable improvement in the characteristics of material or to regain those characteristics which may have been adversely affected by production processes such as welding/bending/forming etc.
How to improve the performance of heat treated materials?
Uniform material organization and composition, improve material properties or prepare for subsequent heat treatment processes. Heat the metal parts to a certain high temperature for a period of time, then let them cool in the air by water spraying, mist spraying, blowing, etc.
What are the benefits of heat treatment for metals?
Heat treatment of the metals is one of the best ways to get the desired performance. It also helps to develop hard surfaces with ductile base materials. Asides from the application benefits, heat treatment is also beneficial to manufacturers. A proper heat treatment process help relieves internal stresses.
Why is heat treatment required after welding steel pipe?
Welding process, because local overheating will cause the pipe deformation and shrinkage stress, so steel pipe return to heat treatment after welding to eliminate internal stress. PWHT is based on the hardness of the steel, the thickness of the welding parts, structural rigidity, welding methods and conditions of use.
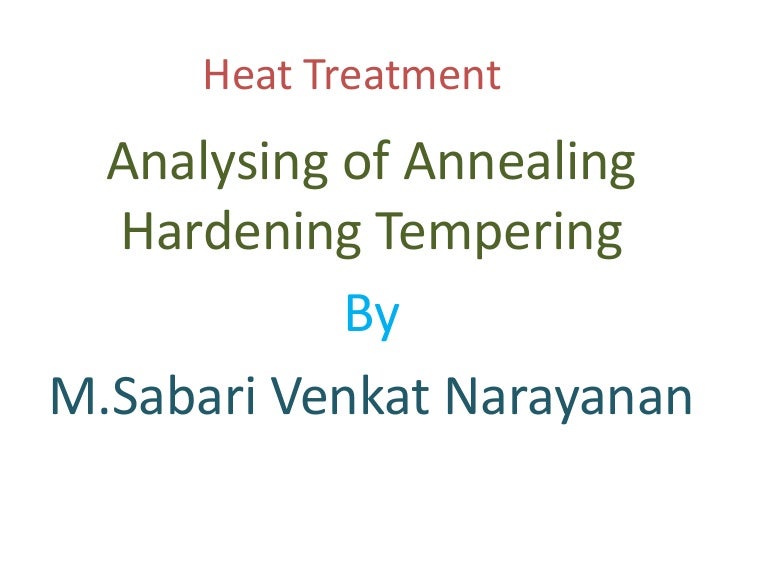
What is the main purpose of heat treatment?
Heat treating can soften metal, to improve formability. It can make parts harder, to improve strength. It can put a hard surface on relatively soft components, to increase abrasion resistance. It can create a corrosion-resistant skin, to protect parts that would otherwise corrode.
What is requirement of heat treatment?
Proper heat treating requires precise control over temperature, time held at a certain temperature and cooling rate. With the exception of stress-relieving, tempering, and aging, most heat treatments begin by heating an alloy beyond a certain transformation, or arrest (A), temperature.
What are four reasons for heat treatment?
Increase the toughness; That is, to produce a steel having both high tensile strength and good ductility, enabling it to withstand high impact. Improve the machine-ability. Improve the cutting properties of tool steels. Change or modify the magnetic properties of steel.
What are the advantages of heat treatment?
Benefits of Heat Treatment in a NutshellMore durable product.Steel becomes tougher, stronger.Easier to weld.Becomes more flexible.Increases its wear-resistance.Increase in overall lifetime of the part.
Why heat treatment of steel is done?
Heat treatment is a controlled process used to alter the microstructure of metals and alloys such as steel and aluminium to impart properties which benefit the working life of a component, for example increased surface hardness, temperature resistance, ductility and strength.
What is critical temperature in heat treatment?
Critical temperature of steel defines phase transition between two phases of steel. As the steel is heated above the critical temperature, about 1335°F (724°C), it undergoes a phase change, recrystallizing as austenite.
What is the advantage and disadvantage of heat treatment?
Heat treatment helps to get desired mechanical and chemical properties, to reduce stresses, prevent stress relief and distortion when put to service. Whilst the disadvantages include distortion, surface oxidation or other contamination, added cost, etc.
What is heat treatment?
Heat treatments are a way of using controlled heating and cooling procedures to change metal’s physical properties and improve them to be used in a large range of industries. These heat treatments vary depending on the metal type, and the mechanical properties that are required for the parts’ function. It is essential that the correct heat ...
How does heat treatment work?
Heat treatment is commonly used to alter or strengthen materials’ structure through a heating and cooling process. It offers many advantages, including: 1 It can change a material’s physical (mechanical) properties and it aids in other manufacturing steps. 2 It relieves stresses, making the part easier to machine or weld. 3 Increases strength, making the material ductile or more flexible. 4 Introduces wear-resistant (hardness) characteristics, either just to the surface or right through the part. 5 Improves brittleness. Some metals can become weak or brittle once exposed to a specific environment, so they need to be treated in order to overcome this. 6 Can improve the electrical and magnetic properties of a metal, which will improve its compatibility with other materials.
Why is annealing used in casting?
Annealing is often used to reduce the hardness of a material as well, which helps to improve its machinability. Suitable for both ferrous and non-ferrous alloys.
What is the purpose of tempering?
A further heating and cooling cycle known as tempering can be used to introduce a degree of ductility to the part, making it tougher and less likely to crack under pressure. Tempering allows parts to become tougher.
What are the advantages of a ductile material?
It offers many advantages, including: It can change a material’s physical (mechanical) properties and it aids in other manufacturing steps. It relieves stresses, making the part easier to machine or weld. Increases strength, making the material ductile or more flexible.
Why use solution annealing?
When it comes to solution annealing, the process, while similar to annealing in its use of temperature, is commonly used with 300 series stainless steels to improve corrosion resistance and ductility.
What is low pressure treatment?
This low-pressure treatment is suitable for alloys that are heat-resistant, including nickel-based ones, and helps parts to better withstand high heat environments and other stresses. For this reason, it’s commonly found in sectors like aerospace, mainly for engines and exhausts.
How does heat treatment work?
These tend to consist of either cooling different areas of an alloy at different rates, by quickly heating in a localized area and then quenching, by thermochemical diffusion, or by tempering different areas of an object at different temperatures, such as in differential tempering.
What is the purpose of heat treating metals?
grain size and composition) is one of the most effective factors that can determine the overall mechanical behavior of the metal. Heat treatment provides an efficient way to manipulate the properties of the metal by controlling the rate of diffusion and the rate of cooling within the microstructure. Heat treating is often used to alter the mechanical properties of a metallic alloy, manipulating properties such as the hardness, strength, toughness, ductility, and elasticity .
How does salt heat up?
Parts are loaded into a pot of molten salt where they are heated by conduction, giving a very readily available source of heat. The core temperature of a part rises in temperature at approximately the same rate as its surface in a salt bath.
What is a heat treating schedule?
Complex heat treating schedules, or " cycles," are often devised by metallurgists to optimize an alloy's mechanical properties. In the aerospace industry, a superalloy may undergo five or more different heat treating operations to develop the desired properties. This can lead to quality problems depending on the accuracy of the furnace's temperature controls and timer. These operations can usually be divided into several basic techniques.
What is the process of heating something to alter it?
Process of heating something to alter it. Heat treating furnace at 1,800 °F (980 °C) Heat treating (or heat treatment) is a group of industrial, thermal and metalworking processes used to alter the physical, and sometimes chemical, properties of a material. The most common application is metallurgical. Heat treatments are also used in the ...
Why is heat treatment called an arrest?
This temperature is referred to as an "arrest" because at the A temperature the metal experiences a period of hysteresis.
How is annealing done?
In ferrous alloys, annealing is usually accomplished by heating the metal beyond the upper critical temperature and then cooling very slowly, resulting in the formation of pearlite. In both pure metals and many alloys that cannot be heat treated, annealing is used to remove the hardness caused by cold working. The metal is heated to a temperature where recrystallization can occur, thereby repairing the defects caused by plastic deformation. In these metals, the rate of cooling will usually have little effect. Most non-ferrous alloys that are heat-treatable are also annealed to relieve the hardness of cold working. These may be slowly cooled to allow full precipitation of the constituents and produce a refined microstructure.
What are the steps of heat treating?
Heat treating processes require three basic steps: Heating to a specified temperature.
What is heat treated parts?
Heat treated parts are essential to the operation of automobiles, aircraft, spacecraft, computers and heavy equipment of every kind. Saws, axes, cutting tools, bearings, gears, axles, fasteners, camshafts and crankshafts all depend on heat treating.
Why is aluminum alloy heat treated?
It is also a vital step in the manufacture of nonferrous products. For example, aluminum alloy automotive castings are heat treated to improve hardness and strength; brass and bronze items are heat treated to increase strength and prevent cracking; titanium alloy structures are heat treated to improve strength at high temperatures.
How much does heat treatment add to metal?
Heat treating adds about $15 billion per year in value to metal products by imparting specific properties that are required if parts are to function successfully. It is very closely linked to the manufacture of steel products: about 80 percent of heat treated parts are made of steel.
Why is hard surface important?
It can make parts harder, to improve strength. It can put a hard surface on relatively soft components, to increase abrasion resistance. It can create a corrosion-resistant skin, to protect parts that would otherwise corrode. And, it can toughen brittle products.
What temperature do you need to quench a cryogenic process?
Some materials are cooled slowly in the furnace, but others must be cooled quickly, or quenched. Certain cryogenic processes require treatment at -120°F or lower . Quenching media include water, brine, oils, polymer solutions, molten salts, molten metals and gases.
Why is heat treatment important?
Heat treatment is an essential process in the material science industry to improve metal properties for commercial purposes. It is one of the key processes that help gain the desired mechanical and chemical properties of metals.
What is heat treatment?
Heat treatment is a heating and then cooling process using predefined methods to achieve desired mechanical properties like hardness , ductility, toughness, strength, etc. It is the combination of thermal, industrial, and metalworking processes to alter the mechanical properties and chemical properties of metals.
How does heat treatment help metals?
Heat treatment assist in improving the ductility of metal in the annealing process. Heat treatment helps in hardening metals. Case hardening helps in hardening only the outer surface of the metal piece keeping the rest of the portion soft and ductile. Machinability of metals gets improved.
How does heat treatment change mechanical properties?
During the whole process, the mechanical properties get changed due to changes in microstructure. All metallic metals have grains which are nothing but microstructures of crystals. The nature of those grains determines the behavior of the mechanical properties of a metal. Heat treatment changes that mechanical structure by controlling the rate ...
What happens after holding a furnace?
After the holding process, cooling starts. The cooling must be done in a prescribed manner. During cooling, there are some structural changes occur. Different media such as water, oil, or forced air is used to aid in cooling. You can also use furnaces for cooling purposes as the control environments help inefficient cooling.
What is the first step in heat treatment?
The first step in the heat treatment process is heating the metal. The temperature depends on the types of metal and the technique used. Sometimes you need to heat the outer surfaces of the metal, and sometimes you need to heat the whole body. That depends on what kind of alteration you want in the mechanical structure.
How is annealing done?
Annealing is done by heating the metals at the above critical temperature , hold them there for some time and then cool it at a very slow rate in the furnace itself. Annealing is usually done on ferrous and non-ferrous metals to reduce hardness after the cold working process.
Why do we heat treat metals?
We heat treat metals in an attempt to optimise the mechanical and physical properties for a given application. Most people think of heat treatment as a process for hardening metal. This is not necessarily so, as many heat treatments are applied to soften metal in order to allow metal working operations such as deep drawing, cold forging and machining.
Is heat treatment an industry?
Heat treatment is a significant industry and forms a basic part of the industrial infrastructure of countries.
Why is preheating important for welds?
Preheating of the weldment area achieves better weld penetration and slows the cooling process, thus allowing added relief of stresses and reduced hardening of the materials .
What is post weld heat treatment?
Post weld heat treatment is designed to return a metal as near as possible to its prefabrication state of yield, ultimate tensile and ductility.
What is the holding temperature of a steel?
The Code sections contain requirements for stress relieving, specifying rate of heating and cooling above 800oF and requiring a holding temperature, usually one hour per inch of thickness of the material. The holding temperatures vary with the P-numbers of the material which in turn are based on alloy content. As an example, P-1 through P-4 require 1100-F holding temperature, P-1 being carbon steels, P-3 being carbon steels alloyed in relatively small percent with molybdemum, manganese and vanadium. P-4 steels are the nickel steels, chrome-molys and nickel- chrome-molys. P-5, P-6 and P-7 high alloy steels generally require a higher holding temperature ranging up to 1350oF. Some of the special steels now listed in the Code sections call for even higher temperatures.
Why are furnace thermocouples important?
The rate of temperature rise, holding time at temperature and rate of cooling are vitally important. For this reason, furnace thermocouples must measure metal temperature, not furnace atmospheric temperature. Heat treatment of any type must be a planned, systematic action.
Where do authorized inspectors encounter heat treatment?
Let's take a short look at some of the most frequently used processes of heat treatment, those which the Authorized Inspector may encounter in boiler and pressure vessel fabrication shops.
Is air normalizing the same as quenching?
This process is used for virtually the same purposes as quenching and tempering. It differs in that normalizing is accomplished by cooling in air in place of fast quenching in a liquid. Air normalizing, much slower than liquid quenching, may be used by itself or the material may be subjected to a controlled furnace tempering process in order to better control desired mechanical properties.
Is heat treatment a systematic action?
Heat treatment of any type must be a planned, systematic action. Poorly performed heat treatment can result in far more harm to material than any good which may result.
What temperature does heat treatment go to?
The first step involves the heating of the metal or alloy to the required temperature. Sometimes, the temperature goes up to 2400°F. It is held at the temperature for a specified amount of time before cooling.
How does heat treatment improve mechanical properties?
Conclusion. Heat treatment of metals is a great way of improving the mechanical properties of metals. Asides from the physical, it can also improve the electrical and magnetic properties of a metal. This further improves the compatibility of the part with other materials.
Why do we heat treat steel?
This is another heat treatment process that helps to increase the resilience of steel. Iron-based alloys are usually hard but often too brittle for certain applications. Tempering helps to alter the hardness, brittleness, and ductility of the metal. This is in a bid to make the machining process easier.
What would happen if metals were not heat treated?
Without the heat treatment of metals, there may be nothing like metal parts for devices and equipment. Even if they existed, they wouldn’t function in the right manner. For example, non-ferrous metal parts would be too weak for several applications.
Why does cooling occur?
Then, cooling occurs to harden the heated material. The process aims towards changing the microstructure of the metal. Also, it helps to bring out desired mechanical, chemical, and physical characteristics. The alteration of these properties benefits the working life of the component involved.
What happens to the microstructure of a metal when it is hot?
While the metal is hot, the microstructure changes . This is the physical structure of the metal. The change in the structure ultimately results in a change in the physical properties of the metal. The ‘soak time’ is the amount of time used to heat the metal.
Why use heat treated metal?
Using effectively heat-treated metal parts ensures the effective and cost-effective running of machines. Furthermore, the product will be a lot more efficient, even for the toughest applications. Also, there may be the need for extremely hard metals for some applications.
What is heat treat pallet?
Heat treat pallets are required for all wood packaging material used in international shipments. One of the necessary steps for ensuring the safety of not only the product being shipped, but also the environment of the product’s destination, is heat treatment. Wood pallets are made from organic material – trees.
How long does it take to heat pallets?
During this process, the pallets, boxes, or crates being treated are heated to a core temperature of 140 degrees for a minimum of 30 minutes. This ensures that all insects and larva will be killed off, after which the pallet can be used and reused to ship goods internationally.
Does Kamps make heat treated pallets?
Kamps Pallets is committed to doing our part in ensuring the supply of safe and sanitary pallets for the use of our customers, and we have the ability to produce heat treated pallets in large numbers as necessary. If your company has a need for heat treated pallets in whatever numbers, please contact us and we can discuss how we can meet this need together.
When the welded pipeline components cannot add heat treatment furnace, heat treatment allows segmentation.?
When the welded pipeline components cannot add heat treatment furnace, heat treatment allows segmentation. In the subsection heat treatment, the length of the repeated heating is at least 300mm, at the same time, it is necessary to protect the outer part of the furnace, in order to prevent harmful temperature gradient.
What is the range of heat treatment for flammable materials?
Flammable materials with 30m range of heat treatment should be cleared.
How does a PWHT work?
The method of PWHT is electric heating. The caterpillar electric heater and linear electric heater should be fixed on the parts which are needed to PWHT; they connect with the automatic controller through cable. And the thermocouple should be fixed on the parts needed to PWHT through the compensating conductor. It connects with the computer automatic controller. Then the controller will work automatically according to the process parameter that is being inputted into the controller .
Why does steel pipe need to be heated after welding?
Welding process, because local overheating will cause the pipe deformation and shrinkage stress, so steel pipe return to heat treatment after welding to eliminate internal stress.
When local heat treatment is applied to weld joints, a circumferential band of the run pipe, and?
When local heat treatment is applied weld joints, a circumferential band of the run pipe, and of the branch where applicable, shall be heated until the specified temperature range exists over the entire pipe section, gradually diminishing beyond a band which includes the weldment or the bent or formed section and at least 25mm beyond the ends thereof .
Should stress corrosion be carried out post weld heat treatment?
On the stress corrosion of the weld, should be carried out post weld heat treatment.
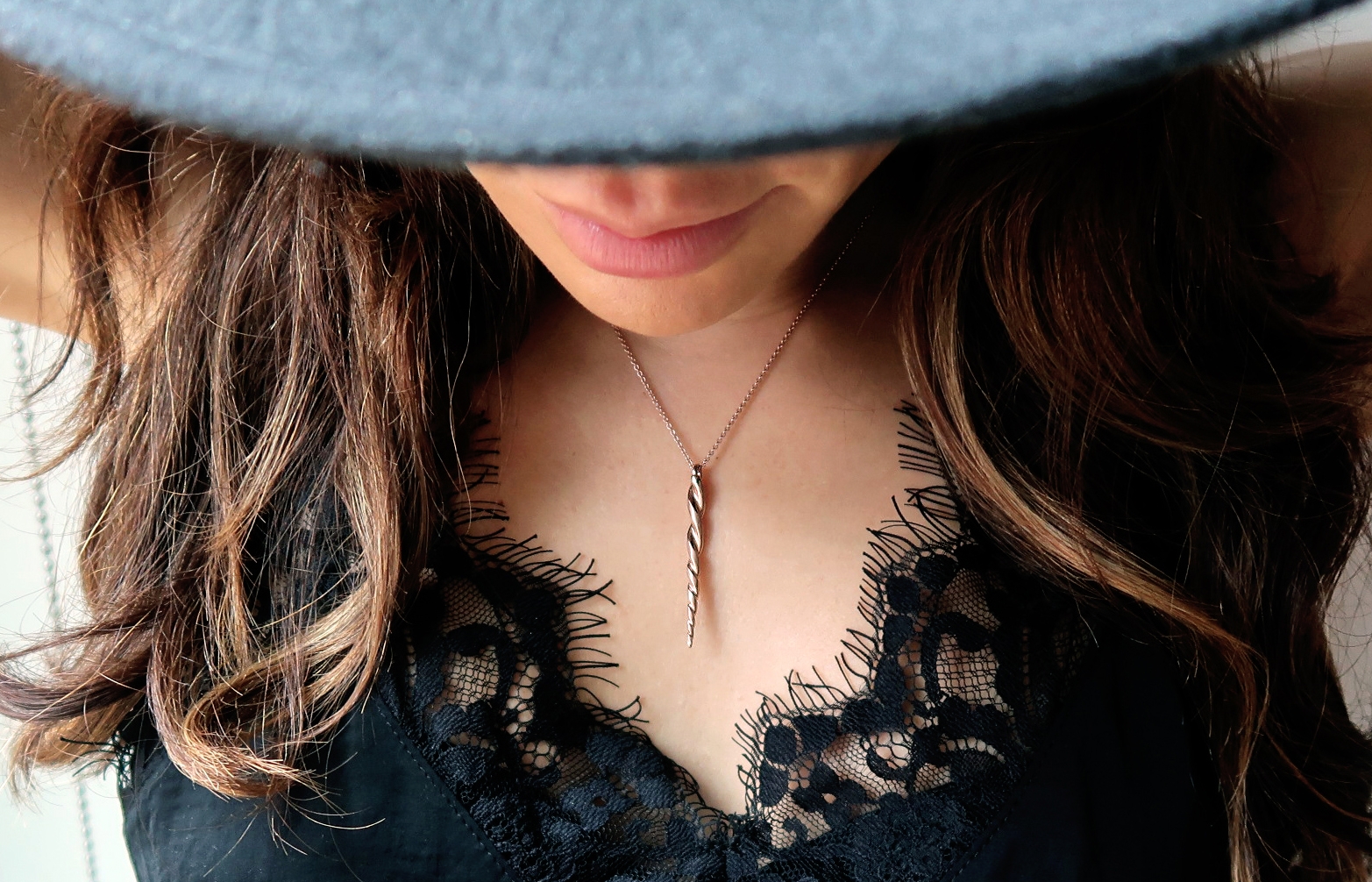
Overview
Heat treating (or heat treatment) is a group of industrial, thermal and metalworking processes used to alter the physical, and sometimes chemical, properties of a material. The most common application is metallurgical. Heat treatments are also used in the manufacture of many other materials, such as glass. Heat treatment involves the use of heating or chilling, normally to extre…
Physical processes
Metallic materials consist of a microstructure of small crystals called "grains" or crystallites. The nature of the grains (i.e. grain size and composition) is one of the most effective factors that can determine the overall mechanical behavior of the metal. Heat treatment provides an efficient way to manipulate the properties of the metal by controlling the rate of diffusion and the rate of cooling within th…
Effects of composition
The specific composition of an alloy system will usually have a great effect on the results of heat treating. If the percentage of each constituent is just right, the alloy will form a single, continuous microstructure upon cooling. Such a mixture is said to be eutectoid. However, If the percentage of the solutes varies from the eutectoid mixture, two or more different microstructures will usually form sim…
Effects of time and temperature
Proper heat treating requires precise control over temperature, time held at a certain temperature and cooling rate.
With the exception of stress-relieving, tempering, and aging, most heat treatments begin by heating an alloy beyond a certain transformation, or arrest (A), temperature. This temperature is referred to as an "arrest" because at the A temperature the metal experiences a period of hystere…
Techniques
Complex heat treating schedules, or " cycles," are often devised by metallurgists to optimize an alloy's mechanical properties. In the aerospace industry, a superalloy may undergo five or more different heat treating operations to develop the desired properties. This can lead to quality problems depending on the accuracy of the furnace's temperature controls and timer. These operation…
Specification of heat treatment
Usually the end condition is specified instead of the process used in heat treatment.
Case hardening is specified by hardness and case depth. The case depth can be specified in two ways: total case depth or effective case depth. The total case depth is the true depth of the case. For most alloys, the effective case depth i…
Furnace types
Furnaces used for heat treatment can be split into two broad categories: batch furnaces and continuous furnaces. Batch furnaces are usually manually loaded and unloaded, whereas continuous furnaces have an automatic conveying system to provide a constant load into the furnace chamber.
Batch systems usually consist of an insulated chamber with a steel shell, a hea…
See also
• Carbon steel
• Carbonizing
• Diffusion hardening
• Induction hardening
• Retrogression heat treatment