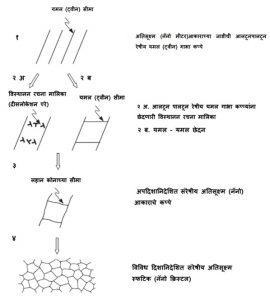
- Introduction. Surface Mechanical Attrition Treatment (SMAT) is a recent process that enables to nanocrystallize the surface of metallic alloys [ [1], [2] ].
- Material and methods. The material used in this study is a polycrystalline austenitic stainless steel corresponding to the AFNOR designation X2CrNiMo18.14.3. ...
- Results. ...
- Discussion. ...
- Conclusions. ...
Does surface mechanical attrition treatment improve the oxidation resistance of AISI 316L?
The present article investigates the effect of Surface Mechanical Attrition Treatment (SMAT) on the high temperature oxidation of AISI 316L, during isothermal oxidation between 650 and 750 °C in air. The observations show a beneficial effect of the SMAT process on the oxidation resistance of 316L steel, for high temperatures.
How to improve the adhesion characteristic of the SMAT?
This adhesion characteristic can be improved by the SMAT through the mechanical state, since this treatment introduces local compression stresses in the substrate, thus changing the stress state on the surface and which may reduce the risk of spallation. 4.1. The role of grain boundaries on chromium diffusion
Does SMAT process affect the oxidation behaviour of 316L stainless steel?
In the present work, the effects of SMAT on the oxidation behaviour of 316L stainless steel are specifically investigated at different temperatures: 650, 700 and 750 °C. First, SMAT process has been deeply investigated on this material, with results that can then be directly used to compare with oxidised samples.
How does surface charachteristics affect the properties of a material?
It can be noticed from many researches that the property of a material can be altered just by changing its surface charachteristics. This is mainly because any defect usually starts from the surface of the material. So by strengthening the surface a lot of defects can be overcome.
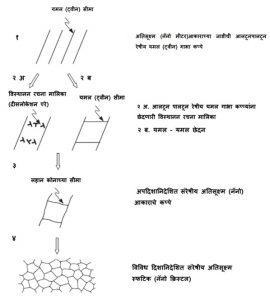
Abstract
Discs of Al 6061 and Al 2024 alloys were coated with Ni powder by surface mechanical attrition treatment. The microstructure of the cross-section of the specimens was investigated by scanning electron microscopy and X-ray diffraction. Mechanical properties were studied by dynamic hardness tests.
1. Introduction
Mechanical alloying (MA) has become a well-established method to refine the microstructure and to prepare supersaturated solid solutions or metastable phases in several alloy systems [1]. MA is usually carried out on a mixture of powders.
2. Experimental
Ni coatings were deposited using a SPEX 8000 shaker mill onto two different technical Al alloy target plates, which were used as the end surface of the hardened steel vial. The targets were discs of Al 6061 and high-Cu (≈5 wt.%) Al 2024 with a thickness of 3 mm.
3. Results and discussions
XRD linewidth analysis has shown that the average grain size of the untreated plates (0.44 and 0.45 μm for Al 6061 and Al 2024, respectively) were almost identical. However, EDX analysis revealed that the Cu-content of Al 2024 was significantly higher than that of the Al 6061 alloy.
4. Conclusions
Discs of Al 6061 and Al 2024 alloys were coated with Ni powder by surface mechanical attrition treatment. In the case of the harder Al 2024 alloy intermetallic phases form while only microstructural refinement occurs for the Al 6061 alloy.
Acknowledgements
ÁR acknowledges the Hungarian-American Enterprise Scholarship Fund (HAESF) for a Senior Reseach Fellowship. The nanoindentrer measurements were made possible by a grant from the National Science Foundation grant no. 0521467. The help of Saejin Park with hardness studies is appreciated.
What is the effect of SMAT on AISI 316L?
The present article investigates the effect of Surface Mechanical Attrition Treatment (SMAT) on the high temperature oxidation of AISI 316L, during isothermal oxidation between 650 and 750 °C in air. The observations show a beneficial effect of the SMAT process on the oxidation resistance of 316L steel, for high temperatures. Indeed, the oxidation kinetics of the treated samples is shown to be related to a preferential growth of chromia starting at 700 °C up to 750 °C. This leads us to conclude that the SMAT used on the 316L reverses the main oxide phase, inhibiting the growth of the hematite and promoting the chromia.
What is SMAT in metals?
Surface Mechanical Attrition Treatment (SMAT) is a recent process that enables to nanocrystallize the surface of metallic alloys [ [1], [2] ]. It can enhance the mechanical properties of treated materials by inducing a grain refinement down to the nanometre scale in the top surface layer. This nanocrystallisation process leads to different effects that have been successively studied on several metallic materials, such as increase in the surface hardness, enhancement of wear resistance and fatigue properties [ [3], [4], [5], [6], [7]] or the coupling with nitriding process [ 8 ]. Recently, investigations have been performed on these effects; most of them mainly focus on the surface morphologies and tribological properties [ 9 ]. It can be expected that SMAT could affect the oxidation resistance. Indeed, due to the induced grain refinement, an increase in the grain boundary volume fraction, from the core to the top surface of the sample, can modify the diffusion mechanisms. It is now well established that the surface reactivity can also be modified by nanocrystallisation treatments [ [10], [11], [12], [13], [14] ]. Moreover, the presence of residual stresses in thermal oxide layers during the isothermal oxidation process may influence the protective properties of the oxide layers. The influence of SMAT process on oxidation phenomena can be found in [ [15], [16], [17], [18], [19], [20] ].
