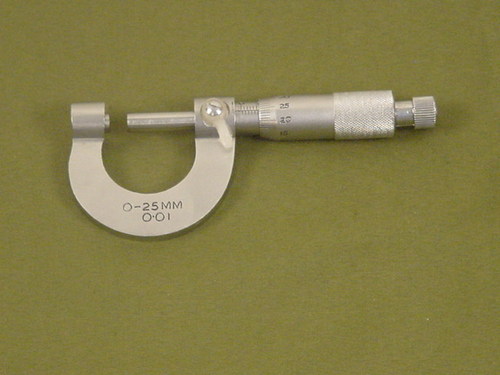
Post Weld Heat Treatment (PWHT), or also called stress relief (SR) is a method for reducing- relieving, and redistributing the residual stresses in the material that have been introduced by welding.
Full Answer
What is post weld heat treatment?
Post weld heat treatment is a controlled process in that a welded components (welded material) is reheated in a furnace or localized heating arrangement to a temperature below its lower critical transformation temperature (AC1), and then it is held at that temperature for a specified amount of time.
What are the heat treatment techniques used in cooling?
During cooling, there are some structural changes occur. Different media such as water, oil, or forced air is used to aid in cooling. You can also use furnaces for cooling purposes as the control environments help inefficient cooling. Following are few common heat treatment technique used in industries.
How does the heat treatment process work?
The first step in the heat treatment process is heating the metal. The temperature depends on the types of metal and the technique used. Sometimes you need to heat the outer surfaces of the metal, and sometimes you need to heat the whole body.
What is heat treatment in metalworking?
During metalworking and equipment fabrication, various heat treatment techniques can be used to alter the physical and mechanical properties of materials. Oftentimes, these techniques are used in combination to achieve desired metal characteristics.

What is post forming heat treatment?
Alternative higher strength steels can be developed by post-forming heat treatment. Retaining the geometry of components during and subsequent to the heat treatment process is a key barrier for the widespread adoption of HSS.
What is meant by post weld heat treatment?
Post Weld Heat Treatment (PWHT), or stress relief as it is sometimes known, is a method for reducing and redistributing the residual stresses in the material that have been introduced by welding.
What is Post heating used for?
Post-heating refers to the maintenance of preheat after the weld has been completed, to allow increased rates of hydrogen evolution from the weld to occur. The post-heat temperature may be the same as, or greater than, the original preheat temperature specified.
What is pre and post weld heat treatment?
When welding some base materials and for some service conditions, preheating and/or postweld heat treatment may be a requirement. These types of thermal treatments are generally required in order to ensure suitable weld integrity and will typically prevent or remove undesirable characteristics in the completed weld.
What is the most commonly used post heat treatment?
In concept, PWHT can encompass many different potential treatments; however, in steel fabrication, the two most common pro- cedures used are post heating and stress relieving. When is it Required? The need for PWHT is driven by code and application requirements, as well as the service environment.
What is the difference between post heating and PWHT?
The heating temperature of PWHT is at least 400 ℃, and the temperature of PWHT is 200-350 ℃. Third,Measures after heat preservation are different,post heat treatment is to cover with heat preservation cotton and let it cool to room temperature slowly.
What is the benefit of post weld heat treatment?
A post weld heat treatment is performed to alleviate residual stresses, increase the strength, increase or decrease the hardness, and reduce the risk of cracking. An array of heating processes can be used to carry out post weld heat treatment.
How many times PWHT can be done?
How many times PWHT is allowed to be done in one weld? and What is the impact on the weld and materia (mechanical/metallurgical properties) if multiple PWHT were done? Hoping to get feedback here as soon as possible. There is no limit, unless imposed by specification, for the number of PWHT's imposed on a weld joint.
What is the need of pre and post-heating?
Pre- and post-heating help to avoid defects such as cracking. These techniques are recommended – and indeed specified – by many standards and codes of practice. Pre-heating is usually applied immediately prior to cutting while both pre- and post-heating are used in welding.
Where is PWHT required?
PWHT is required where there is a risk of environmentally-assisted cracking. PWHT of C-Mn steels is typically carried out at approximately 600°C, for one hour per 25mm of thickness.
What is pre heat treatment?
What is Preheating? In regard to piping and tubing, preheating is the application of heat to a base metal (weld metal, HAZ, and adjacent base metal) prior to and throughout welding, as well as at the start of each pass in a multi-pass weld.
What is the difference between post weld heat treatment and stress relieving?
PWHT decreases the weld & HAZ hardness by reducing the locked-in stresses. Due to improved ductility and tempering effects on the material, the toughness of the material is increased, although not at a pronounced level. PWHT improves the corrosion resistance and service-related cracking resistance of the materials.
What is post weld heat treatment?
Post-weld heat treatment (PWHT) reduces the levels of tensile residual stresses in a joint. It does not reduce these levels to zero, however, and, even in a very well controlled thermal cycle, the levels of final residual stress are unlikely to be much below 30% of the material yield strength. If a tensile residual stress of, say, 100 MPa, remains after PWHT, almost all applied fatigue cycles (assuming these are typically less than 100 MPa in stress range) still result in entirely tensile stresses at the weld toe and are fully damaging.
What is temper bead welding?
The principle is simple enough – when one layer of weld metal is laid down on top of another the heat from the upper one provides some heat treatment (grain refinement) to the weld underneath. A multilayer weld which is built up in this way will therefore be given an amount of grain refinement throughout its depth. The top layer of the final weld pass will not have anything above it to provide it with heat treatment, so the solution is to grind it off. Figure 11.5 shows the idea.
What happens if tensile residual stress is 100 MPa?
If a tensile residual stress of, say, 100 MPa, remains after PWHT, almost all applied fatigue cycles (assuming these are typically less than 100 MPa in stress range) still result in entirely tensile stresses at the weld toe and are fully damaging.
What temperature is chromium rich carbide heated to?
It is also caused by precipitation of grain boundary chromium-rich carbides in the region of the HAZ which is heated to temperatures between 500 and 850 °C. Susceptible materials should be given a post-weld heat treatment to a temperature greater than 950 °C to take the carbides into solution.
What temperature is required for a polythionic acid?
However, in petroleum refinery units, where polythionic acids may form, a stabilisation heat treatment (for example at 850–920 °C for type 347) is sometimes required for resistance to intergranular attack. 19. A second means of overcoming sensitisation is to reduce carbon levels in the steel.
What is the first step in heat treatment?
The first step in the heat treatment process is heating the metal. The temperature depends on the types of metal and the technique used. Sometimes you need to heat the outer surfaces of the metal, and sometimes you need to heat the whole body. That depends on what kind of alteration you want in the mechanical structure.
What is heat treatment?
Heat treatment is a heating and then cooling process using predefined methods to achieve desired mechanical properties like hardness , ductility, toughness, strength, etc. It is the combination of thermal, industrial, and metalworking processes to alter the mechanical properties and chemical properties of metals.
How does heat treatment help metals?
Heat treatment assist in improving the ductility of metal in the annealing process. Heat treatment helps in hardening metals. Case hardening helps in hardening only the outer surface of the metal piece keeping the rest of the portion soft and ductile. Machinability of metals gets improved.
How is annealing done?
Annealing is done by heating the metals at the above critical temperature , hold them there for some time and then cool it at a very slow rate in the furnace itself. Annealing is usually done on ferrous and non-ferrous metals to reduce hardness after the cold working process.
What is annealing in metals?
Annealing. Annealing is a heat treatment process that is used to soften the metal. In other words, annealing helps to improve ductility, machinability, and toughness. On the flip side, the hardness of metals gets reduced. Annealing does this by changing the microstructure of metals.
What is the process of increasing the hardness of a metal?
Curborization. In carburization, the hardness of the metal piece is increased by increasing the carbon content. The metal piece is heated below the melting point with high carbon materials such as charcoal. The heated metal piece then absorbs carbons to make it more hard and brittle.
How does tampering work?
Tampering is a very common process for machine tools, knives, etc. Tampering is usually done by heating the metal at a relatively low temperature. The temperature depends on the required mechanical properties of metals.
What is post weld heat treatment?
Post weld heat treatment ( PWHT) is a controlled process in which a material that has been welded is reheated to a temperature below its lower critical transformation temperature, and then it is held at that temperature for a specified amount of time. It is often referred to as being any heat treatment performed after welding; however, within the oil, gas, petrochemical and nuclear industries, it has a specific meaning. Industry codes, such as the ASME Pressure Vessel and Piping Codes, often require mandatory performance of PWHT on certain materials to ensure a safe design with optimal mechanical and metallurgical properties.
What is the holding temperature of a material?
This is to allow the material to reach a stable condition where the distribution and levels of stresses become more uniform and decrease. The specified holding temperature is one that is at a high enough temperature to relieve high residual stress levels, yet is still below the lower transformation temperature. In addition to the reduction of stress, high hold temperatures below the transformation temperature allow for microstructural transformations, therein reducing hardness and improving ductility. Great care should be taken as to not heat the component above the lower transformation temperature, as detrimental metallurgical effects and impaired mechanical properties can result. In addition, the holding temperature should not be greater than the original tempering temperature unless later mechanical testing is performed. Holding above the original tempering temperature can reduce the strength of the material to below ASME required minimums.
Why do we need PWHT?
The need for PWHT is mostly due to the residual stresses and micro-structural changes that occur after welding has been completed. During the welding process, a high temperature gradient is experienced between the weld metal and the parent material. As the weld cools, residual stress is formed.
Why are thermocouples used in PWHT?
Thermocouples are typically attached to the component undergoing PWHT to check and ensure that heating rates, hold temperatures, and cooling rates meet code specification. Computer software is typically used in conjunction with the thermocouples to monitor the fore-mentioned variables and provide documentation that the PWHT was performed properly.
What happens if the rate of heating is not performed properly?
If the rate of heating is not performed properly, either by heating too quickly or unevenly, temperature gradients within the component can become detrimental to the component. As a result, stress cracks may occur and residual stresses not previously created can form when the component is cooled to ambient temperatures.
Why is rapid cooling rate important?
As with the heating rate, the cooling rate must be controlled, as to avoid any detrimental temperature gradients that could cause cracking or introduce new stresses during cooling. In addition to this, rapid cooling rates can increase hardness, which may increase the susceptibility of a brittle fracture.
Is it OK to hold a material above the original tempering temperature?
In addition, the holding temperature should not be greater than the original tempering temperature unless later mechanical testing is performed. Holding above the original tempering temperature can reduce the strength of the material to below ASME required minimums.
What is PWHT?
The full form of PWHT is Post-weld heat treatment. PWHT is a controlled process that involves reheating the metal below its lower critical transformation temperature, following a welding process.
When PWHT is required for Carbon Steel?
Post Weld Heat Treatment or PWHT of Carbon Steel must be performed after every welding in order to ensure the material strength of the part is retained. The exact criteria for PWHT of carbon steel are mentioned in the ASME BPVC code.
PWHT Method and Equipment
The local post-weld heat treatment of the welded joints on the pipes shall be carried out by the electric-resistance method and after the completion of all welding or repairing operation.
Requirements for Post Weld Heat Treatment or PWHT
Before applying for the detailed PWHT requirements and exemption in these paragraphs, satisfactory weld procedure qualifications of the welding procedures specification to be used shall be performed in accordance with all the essential variables of ASME SECTION IX including conditions of post-weld heat treatment and including other restrictions listed below..
Preparation and Attachment of Thermocouple for PWHT
After performing visual inspection and removing surface defects and temporary tack welds (if any) an adequate number of thermocouples (based on the diameter of pipes) shall be attached to the pipe directly and equally spaced location along the periphery of the pipe joint.
PWHT Temperature, Time Record
The post-weld heat treatment temperature and time and its heating and cooling rates shall be recorded automatically and present the actual temperature of the weld area. Each thermocouple shall be connected to the controlling and recording instrument for each treated joint.
Heating, Holding and Cooling in PWHT
The heating temperature above 300°c shall be recorded and the heating and cooling rate shall not be more than that specified in related WPS and standards but in no case, more than 200°c/hr and the difference between the temperatures measured by various thermocouples shall be within the range specified.
Why is heat treatment called an arrest?
This temperature is referred to as an "arrest" because at the A temperature the metal experiences a period of hysteresis.
What is the process of heating something to alter it?
Process of heating something to alter it. Heat treating furnace at 1,800 °F (980 °C) Heat treating (or heat treatment) is a group of industrial, thermal and metalworking processes used to alter the physical, and sometimes chemical, properties of a material. The most common application is metallurgical. Heat treatments are also used in the ...
How much carbon is in hypoeutectoid steel?
A hypoeutectoid steel contains less than 0.77% carbon. Upon cooling a hypoeutectoid steel from the austenite transformation temperature, small islands of proeutectoid-ferrite will form. These will continue to grow and the carbon will recede until the eutectoid concentration in the rest of the steel is reached.
How does steel change carbon?
When steel is heated in an oxidizing environment, the oxygen combines with the iron to form an iron-oxide layer, which protects the steel from decarburization. When the steel turns to austenite, however, the oxygen combines with iron to form a slag, which provides no protection from decarburization. The formation of slag and scale actually increases decarburization, because the iron oxide keeps oxygen in contact with the decarburization zone even after the steel is moved into an oxygen-free environment, such as the coals of a forge. Thus, the carbon atoms begin combining with the surrounding scale and slag to form both carbon monoxide and carbon dioxide, which is released into the air.
What happens when an alloy is cooled to an insoluble state?
If the alloy is cooled to an insoluble state, the atoms of the dissolved constituents (solutes) may migrate out of the solution. This type of diffusion, called precipitation, leads to nucleation, where the migrating atoms group together at the grain-boundaries.
What is a bell furnace?
Bell-type furnace. Bell furnaces have removable covers called bells, which are lowered over the load and hearth by crane. An inner bell is placed over the hearth and sealed to supply a protective atmosphere. An outer bell is lowered to provide the heat supply.
Why are nonferrous alloys annealed?
Most non-ferrous alloys that are heat-treatable are also annealed to relieve the hardness of cold working. These may be slowly cooled to allow full precipitation of the constituents and produce a refined microstructure. Ferrous alloys are usually either " full annealed" or " process annealed.".
Why are metals reheated?
Metals are reheated at a low temperature to attain a desired combination of strength, hardness and durability. Tempering time and temperature are controlled to produce the desired material properties. Steels are always tempered after quenching in order to relieve stresses and reduce the brittleness from hardening.
What is annealing a metal?
With metals that cannot undergo heat treatment, annealing helps to reduce the hardness caused by cold working. Quenching – Quenching involves cooling a metal at a rapid rate. Its impact on metal properties varies from alloy to alloy.
What is hardening steel?
Hardening is often followed by tempering of the metal to alleviate internal stresses. In case hardening of steels, carbon is introduced to harden the outer layer of material, leaving a soft and ductile core, which improves wear resistance.
What is the purpose of hardening metal?
Hardening – As its name indicates, hardening is performed to improve the hardness of a metal, resulting in a tougher and more durable product . The metal is heated above its critical transformation temperature and then it is cooled quickly via quenching.
Why is annealing important?
With metals that cannot undergo heat treatment, annealing helps to reduce the hardness caused by cold working.
Why do we need postweld heat treatment?
One of the reasons why post-weld heat treatment is required on any metal is to improve the mechanical properties of weldment and also make it useful for other specific service conditions. This is demonstrated to help reduce the residual stress level and hardness diffusing the required weldment with some flexibility.
Why is post weld heat treatment important?
They are responsible for miles of welding seams. A post-weld heat treatment (PWHT) allows welders to maintain toughness on the materials in the weld zone. So the elasticity of the material is increasing and it can be bent but not break. This characteristic is extremely important for the durability of the structure.
What is PWHT welding?
PWHT is one of the methods used by welders to reduce residual stresses to combat hardness or enhance material strength. If PWHT is not adequately performed or is overlooked altogether, the residual stresses plus the load stresses can join together to cause a brittle fracture.
Why is PWHT used?
Because PWHT helps to lower the level of hardness, the thermal treatment welded component can easily be machined to bring about dimensional conditions. The softening of these welded parts makes it easy for grinding, machining, including other surfaces treatment that the metal may require.
What happens to HAZ after welding?
Softening. After the HAZ material is welded, it gets harder, and with excess hardness, the material becomes nearly useless for a particular kind of work application. This is where PWHT comes to play. Companies mostly use post-weld heat treatment to change the hard heat-affected zone.
What causes residual stress during welding?
A high thermal ingredient may be a significant factor in residual stress during welding. During any thermal welding process, heat may cause an expansion in some metals while in cooling, it may also cause localized contraction. This is what brings about unwanted residual stresses.
Why does tempered material lose strength?
Loss Of Strength. Reduced strength of a material can occur when there is too high a temperature or too much time is spent on stress relief post-weld heat treatment. Also, tempering treatment is a cause of reducing strength for tempered and quenched materials.
What is heat treatment?
Heat treatment is a critical and complex element in the manufacturing of gears that greatly impacts how each will perform in transmitting power or carrying motion to other components in an assembly. Heat treatments optimize the performance and extend the life of gears in service by altering their chemical, metallurgical, and physical properties.
How does heat treatment help gears?
Heat treatments also improve a gear’s fatigue life by generating subsurface compressive stresses to prevent pitting and deformation from high contact stresses on gear teeth. These same compressive stresses prevent fatigue failures in gear roots from cyclic tooth bending.
What is press quenching?
The art of press quenching while being around for decades remains somewhat of a mystery to the engineering world, and even our own heat treating industry. In basic form, gears are carburized in large batches, slow cooled, reheated individually, and then quenched rapidly under some form of restraint to minimize distortion. The main dimensions that are restrained during press quenching are the flatness of the gear and the roundness of the bore in relation to the hub.
What temperature does carbon steel have to be to be austenitized?
An approximate austenitizing temperature for most plain carbon steels is around 1330F and varies by exact grade of steel. Once full transformation of the steel to an austenite structure has occurred the austenite may be quenched (cooled rapidly), and that austentite structure will transform to a martensite structure.
What is neutral hardening?
Neutral hardening refers to maintaining the carbon potential of the atmosphere at the same percentage as the carbon in the steel during the hardening cycle. This means that carbon is entering and leaving the surface of the steel at the same rate, and no net gain or net loss of carbon atoms inside the surface of the steel occurs. Many gears are neutral hardened, but for the most demanding applications case hardening processes, such as carburizing and nitriding, are the preferred methods due to their improved wear characteristics and mechanical properties.
Why is steel tempered down?
After quenching to the maximum hardness achievable, which is determined by the steel’s carbon content, the steel may then be tempered down to a lower hardness to improve ductility and toughness at the expense of slightly reducing the strength, hardness, and wear characteristics of the material.
What is an annealed structure?
An annealed structure is a combination of primarily ferrite (Fe, pure iron) and iron carbide (Fe3C, cementite). These will be in the form of alternating layers of ferrite and Fe3C (pearlitic structure), or ferrite with dispersed Fe3C spheres or spheroids (spherodized structure).
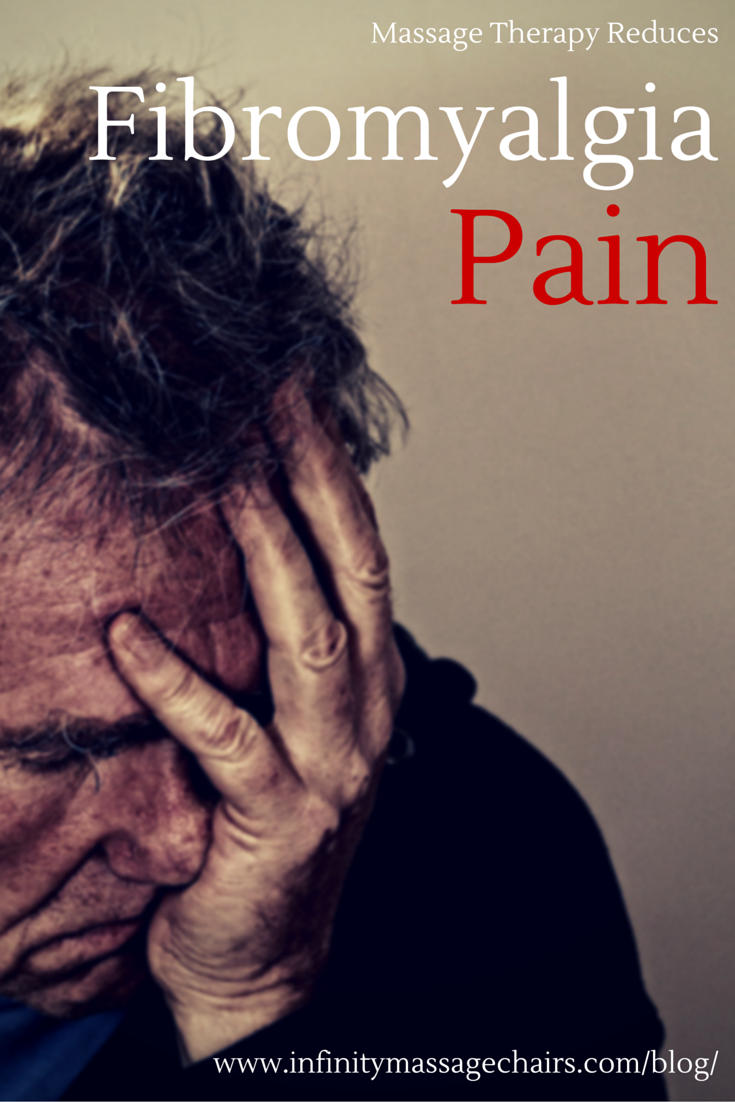