
Medicalnewstoday.com
1. Let it out...
2. Pass stool...
3. Eat slowly...
4. Avoid chewing gum...
5. Say no to straws...
6. Quit smoking...
7. Choose non-carbonated drinks...
8. Eliminate problem...
Learn More...Top10homeremedies.com
1. Fennel Seeds Act as a Carminative...
2. Peppermint Eases the Pain...
3. Ginger Helps the Body Expel Intestinal Gas...
4. Chamomile Tea Relieves Stomach Gas...
5. Caraway Seeds Facilitate Gas Expulsion...
6. Probiotics Balance Healthy Gut Flora...
7. Turmeric Improves Digestion...
8. A Pinch of Asafetida Relieves Gas Pains...
Learn More...Homeremedyshop.com
1. Garlic...
2. Ginger...
3. Black Pepper...
4. Caraway Seeds (Kala Jeera)...
5. Buttermilk...
6. Cloves...
7. Fennel (Saunf)...
8. Warm Water...
Learn More...What gases are used in heat treatment?
Vacuum heat treatments can also be used to remove dissolved contaminants. The inert gases most commonly used in heat treatment processes are argon (Ar), helium (He), and nitrogen (N2), and they are often used in the following combinations: Ar/He, Ar/He/ N2, and N2/He.
What is solution heat treatment?
What is solution heat treatment? Solution Heat Treatment is a treatment in which an aluminum alloy is heated to a suitable temperature and held at this temperature for a sufficient length of time to allow the desired constituent to enter into the solid solution, followed by rapid cooling to hold the constituent in the solution. .
What is heat treatment in glass?
Heat treatments are also used in the manufacture of many other materials, such as glass. Heat treatment involves the use of heating or chilling, normally to extreme temperatures, to achieve the desired result such as hardening or softening of a material. Heat treatment techniques include annealing, case hardening,...
What are the key processes of heat treatment?
Below are those key processes of heat treatment. The first step in the heat treatment process is heating the metal. The temperature depends on the types of metal and the technique used. Sometimes you need to heat the outer surfaces of the metal, and sometimes you need to heat the whole body.
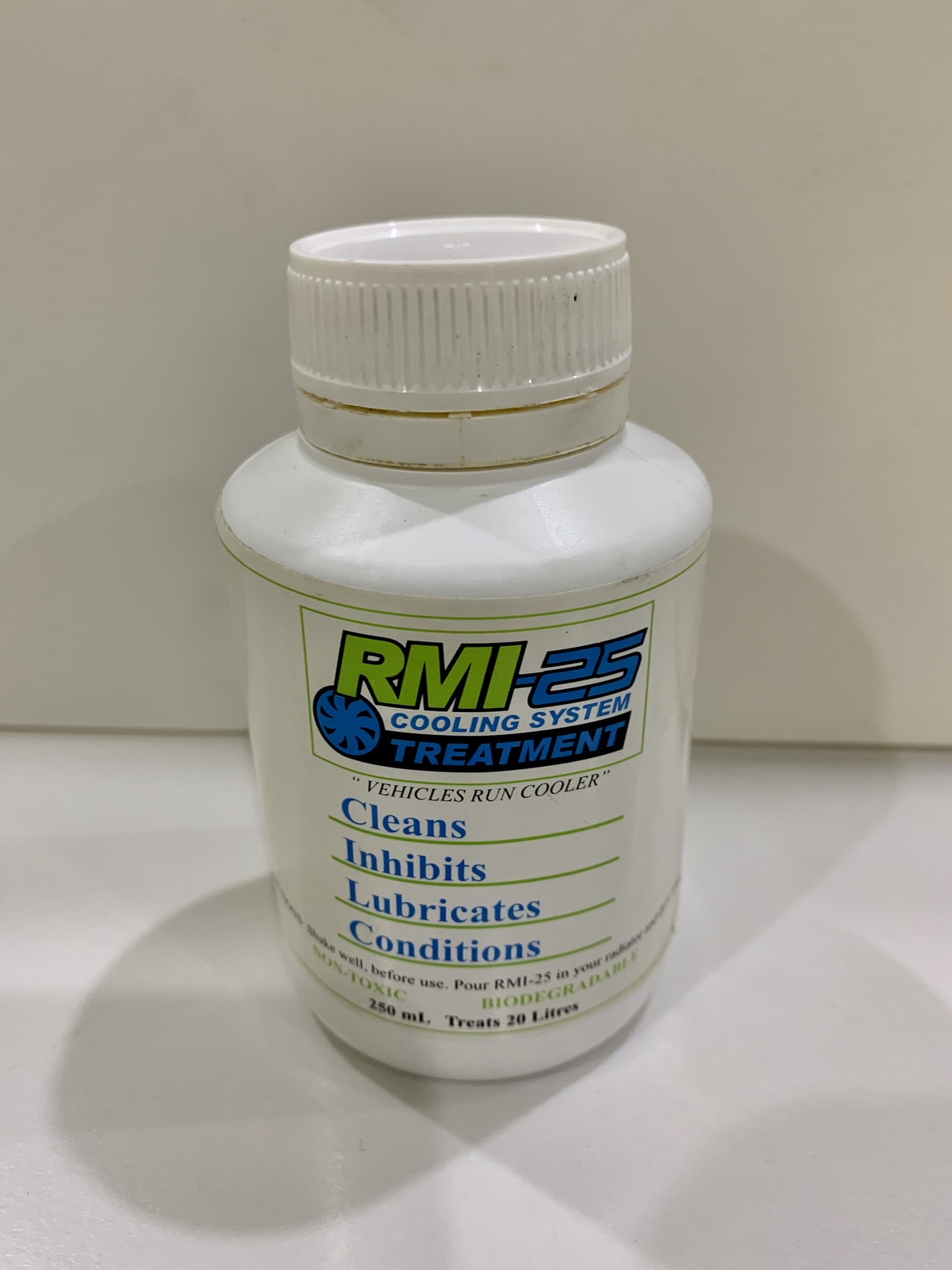
What are the ingredients in HEET?
The specific active ingredients of HEET and ISO-HEET are methanol and isopropanol, respectively. Amazingly enough, ethanol works precisely the same way: Water is absorbed by the ethanol and then gets vaporized in the combustion process.
What is in HEET gas treatment?
How does it work? HEET® brand contains a special fuel additive and methanol. When HEET® brand is added to the gas tank, it sinks to the bottom and mixes with any water. Since both HEET® brand and water are heavier than gasoline, they go to the bottom of the gas tank.
What is gas treatment made of?
Gas Treatments contain polyisobutene or PIB. They are formulated to improve the quality of the gas that you use by ridding the fuel of harmful agents like carbon deposits and water that can dilute the fuel.
Will HEET hurt my engine?
One bottle of HEET® will protect up to 20-gallons of fuel. There is a caveat that you must be aware of – regular HEET® in the yellow bottle is for gasoline 4-stroke engines only, it could damage 2-stroke or diesel engines.
Is HEET 100% methanol?
Yes: Heet is allegedly 99% methanol, and according to the BTU rating is 8,900…
What is the difference between ISO-HEET and HEET?
YELLOW - WHAT IS THE DIFFERENCE? ISO-HEET® Brand (red) is a premium water remover and injector cleaner that can be used all year-round and can be used in all types of gasoline, 2-cycle mix and DIESEL. HEET® (yellow) is designed to prevent and treat freezing gas lines and remove some water.
Is STP the same as Heet?
Heet is alcohol and STP is a petroleum based solvent (which may contain some alcohol/ethanol). If you're curious ... take some STP and put it in an old tin can and light it. My guess is it'll have a noxious odor and may smoke, whereas HEET burns clean and hot.
Is gas treatment safe?
While most fuel additives are, at worst, harmless, Trotta warns against using engine cooling system additives that claim to plug leaks. These, she says, will only work temporarily on small leaks, will have no effect on larger leaks and could cause damage to your car's mechanics.
What's the best gas treatment?
Editor's Pick: Chevron Techron Concentrate Plus Fuel System Cleaner. ... Red Line Complete SI-1 Fuel System Cleaner (60103) ... Royal Purple Max-Clean Fuel System Cleaner and Stabilizer (11722) ... Liqui Moly Jectron Fuel Injection Cleaner. ... Sea Foam Motor Treatment (SF-16) ... Lucas Oil Deep Clean Fuel System Cleaner (10512)More items...•
How much water will HEET Remove from gas?
How Much Water Will A Bottle Of Heet Remove? Adding Heet to gas tanks will dissolve the water and remove the oil. Aside from being a gas-freezing agent, ISO-HEET has the additional feature of removing up to five times the water from the mix.
How often should you put HEET in your car?
Many mechanics recommend that you pour a bottle of Heet into your fuel tank every time you fill up during the winter months. This is the best practice when it is consistently below twenty degrees. However, if temperatures are closer to thirty, you may only need to use it once every two or three fill-ups.
How much water does HEET remove?
ISO-HEET Heet is the industry standard if you need an additive to remove the water from your gas tank. Not only is ISO-HEET a gas anti-freeze, but it can remove up to 5x the water as other additives.
How is endothermic gas produced?
The endothermic gas is produced when a mixture of air and fuel at a very low air-to-gas ratio is introduced into an externally heated retort that itself contains an active catalyst (usually nickel) for cracking the mixture . When this gas leaves the retort, it is rapidly cooled before it arrives in the furnace.
Does heat treatment require an inert atmosphere?
There are several different heat treatment processes that may require a controlled atmosphere in order to be successful. Those requiring either an inert atmosphere or a hydrogen atmosphere include the following:
Why is heat treated steel used?
This heat treatment process is usually carried for low and medium carbon steel as well as alloy steel to make the grain structure more uniform and relieve the internal stresses.
Why is heat treatment important?
It is very important manufacturing process that can not only help the manufacturing process but can also improve the product, its performance, and its characteristics in many ways. By Heat Treatment process, Example: The plain carbon steel. The following changes may be achieved: The hardness of Steel may be increased or decreased.
What are the changes in steel?
The following changes may be achieved: The hardness of Steel may be increased or decreased. Internal stresses that are set up due to cold or hot working may be relieved. The machinability of Steel may be enhanced. The mechanical properties like tensile strength the Talati shock resistance toughness etc may be improved.
What is hardening steel?
Hardening is a heat treatment process carried out to increase the hardness of Steel.
What is recrystallization in steel?
This causes complete recrystallization in steel to form New grain structure. This will release the internal stresses previously the strip in the steel and improve the machinability.
What is normalizing steel?
Normalizing is a heat treatment process similar to annealing in which the Steel is heated to about 50 degree Celsius above the upper critical temperature followed by air cooling. This results in a softer state which will be lesser soft than that produced by annealing.
How long does steel stay in a cyanide bath?
The immersed Steel parts are left in the molten cyanide bath for about 15 to 20 minutes.
What is a heat treating schedule?
Complex heat treating schedules, or " cycles," are often devised by metallurgists to optimize an alloy's mechanical properties. In the aerospace industry, a superalloy may undergo five or more different heat treating operations to develop the desired properties. This can lead to quality problems depending on the accuracy of the furnace's temperature controls and timer. These operations can usually be divided into several basic techniques.
How does heat treatment work?
These tend to consist of either cooling different areas of an alloy at different rates, by quickly heating in a localized area and then quenching, by thermochemical diffusion, or by tempering different areas of an object at different temperatures, such as in differential tempering.
What is the purpose of heat treating metals?
grain size and composition) is one of the most effective factors that can determine the overall mechanical behavior of the metal. Heat treatment provides an efficient way to manipulate the properties of the metal by controlling the rate of diffusion and the rate of cooling within the microstructure. Heat treating is often used to alter the mechanical properties of a metallic alloy, manipulating properties such as the hardness, strength, toughness, ductility, and elasticity .
What is the process of heating something to alter it?
Process of heating something to alter it. Heat treating furnace at 1,800 °F (980 °C) Heat treating (or heat treatment) is a group of industrial, thermal and metalworking processes used to alter the physical, and sometimes chemical, properties of a material. The most common application is metallurgical. Heat treatments are also used in the ...
Why is heat treatment called an arrest?
This temperature is referred to as an "arrest" because at the A temperature the metal experiences a period of hysteresis.
How does salt heat up?
Parts are loaded into a pot of molten salt where they are heated by conduction, giving a very readily available source of heat. The core temperature of a part rises in temperature at approximately the same rate as its surface in a salt bath.
What is heat treatment?
Heat treatment is a critical and complex element in the manufacturing of gears that greatly impacts how each will perform in transmitting power or carrying motion to other components in an assembly. Heat treatments optimize the performance and extend the life of gears in service by altering their chemical, metallurgical, and physical properties.
How does heat treatment help gears?
Heat treatments also improve a gear’s fatigue life by generating subsurface compressive stresses to prevent pitting and deformation from high contact stresses on gear teeth. These same compressive stresses prevent fatigue failures in gear roots from cyclic tooth bending.
How is induction heat treated?
Induction heat treating is localized heat treatment used to increase the fatigue life, strength, and wear resistance of a component. Induction hardening is accomplished by placing the part inside an alternating magnetic field causing an electrical current to form at the surface. Heat is generated as a result of the I2R losses in the material and allows heat treaters to selectively austenitize only the surface material of a component while leaving the core material untransformed. Not only is the surface only selectively heated, but induction allows only those desired surfaces to be heated while other surfaces may be left cold. In the case of gears it is possible to only austenitize the near surface of a single tooth leaving the balance of the part cold during processing. The heated gear surface is subsequently quenched in either water, oil, or a polymer based quench to transform the austenite into martensite thereby increasing hardness in the required area while leaving the remainder of the component virtually undisturbed.
What happens to steel when it is heated?
In fact, when purchasing steel it is generally in the annealed condition. An annealed structure is a combination of primarily ferrite (Fe, pure iron) and iron carbide (Fe3C, cementite). These will be in the form of alternating layers of ferrite and Fe3C (pearlitic structure), or ferrite with dispersed Fe3C spheres or spheroids (spherodized structure). When steel is heated above its austenitizing temperature, it transforms into the austenite structure. An approximate austenitizing temperature for most plain carbon steels is around 1330F and varies by exact grade of steel. Once full transformation of the steel to an austenite structure has occurred the austenite may be quenched (cooled rapidly), and that austentite structure will transform to a martensite structure. This transformation of austenite to martensite is the hardening process. The martensite structure yields the highest hardness and tensile strength properties of any structure for that steel. Producing a martensitic structure from austenite is the goal in hardening heat treatment of steels. One critical aspect of this hardening process is the cooling rate employed during quenching. Each grade of steel requires that a certain minimum cooling rate be achieved during quenching or the transformation from austenite to martensite will not occur. Austenitized steels held at high temperature and quenched too slowly down to ambient temperature will not transform from austenite to a martensitic structure. They will instead revert back a softer mix of ferrite and cementite again.
What is neutral hardening?
Neutral hardening refers to maintaining the carbon potential of the atmosphere at the same percentage as the carbon in the steel during the hardening cycle. This means that carbon is entering and leaving the surface of the steel at the same rate, and no net gain or net loss of carbon atoms inside the surface of the steel occurs. Many gears are neutral hardened, but for the most demanding applications case hardening processes, such as carburizing and nitriding, are the preferred methods due to their improved wear characteristics and mechanical properties.
What causes distortion in heat treatment?
A third source of distortion is quenching, which is typically the main offender in distorting parts during heat treatment. The ideal quench is the slowest quench that will uniformly pull heat out of the part, while still fully transforming the surface to martensite and achieving the desired case and core properties. This sounds easy enough, but in practice it can be quite difficult given the design and complex shape of many gears. Due to variations in customers’ part geometries, limitations in fixture designs, non-uniform quench tank agitation, and part-to-part or part-to-fixture interactions, it is the most difficult distortion mechanism to resolve and predict. Even within a single part it’s possible to have some thinner sections of a component cool faster than thicker sections causing one area to transform earlier than another and warp dimensions as the transformations with their associated volume expansions occur at different times during a quench.
Why is heat treatment important for gears?
In all cases, gear design engineers understand that heat treatments play a complex and vital role in both the ease of manufacturing and the performance of the gears they make. Today, many options exist for the heat treatment of gears. Proper selection and design of the heat treatment process can greatly affect performance, ease of manufacture, and economics of a component. This paper will focus on a variety of different processes and highlight some benefits and disadvantages of each.
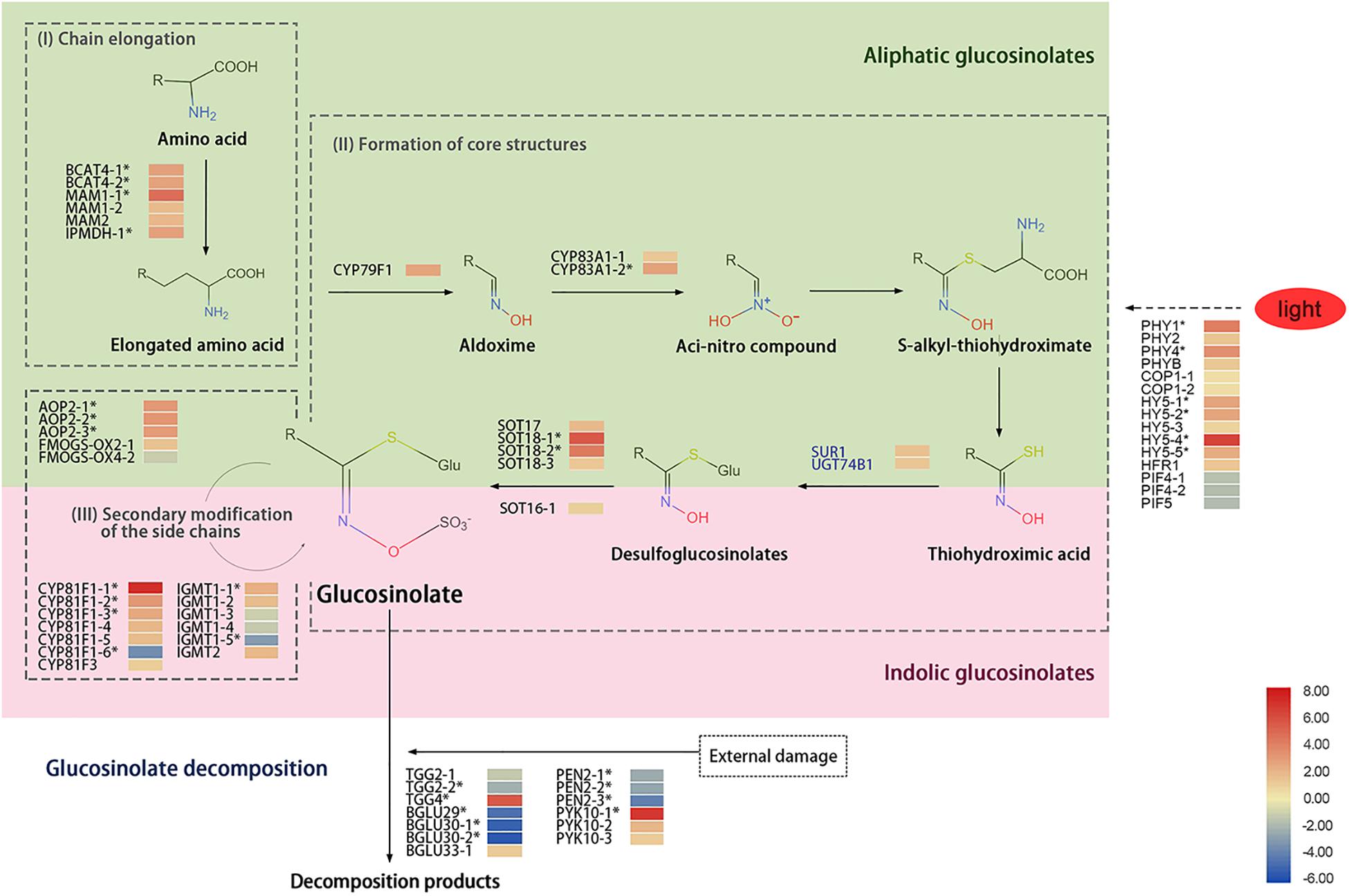
Overview
Heat treating (or heat treatment) is a group of industrial, thermal and metalworking processes used to alter the physical, and sometimes chemical, properties of a material. The most common application is metallurgical. Heat treatments are also used in the manufacture of many other materials, such as glass. Heat treatment involves the use of heating or chilling, normally to extre…
Physical processes
Metallic materials consist of a microstructure of small crystals called "grains" or crystallites. The nature of the grains (i.e. grain size and composition) is one of the most effective factors that can determine the overall mechanical behavior of the metal. Heat treatment provides an efficient way to manipulate the properties of the metal by controlling the rate of diffusion and the rate of cooling within th…
Effects of composition
The specific composition of an alloy system will usually have a great effect on the results of heat treating. If the percentage of each constituent is just right, the alloy will form a single, continuous microstructure upon cooling. Such a mixture is said to be eutectoid. However, If the percentage of the solutes varies from the eutectoid mixture, two or more different microstructures will usually form sim…
Effects of time and temperature
Proper heat treating requires precise control over temperature, time held at a certain temperature and cooling rate.
With the exception of stress-relieving, tempering, and aging, most heat treatments begin by heating an alloy beyond a certain transformation, or arrest (A), temperature. This temperature is referred to as an "arrest" because at the A temperature the metal experiences a period of hystere…
Techniques
Complex heat treating schedules, or "cycles", are often devised by metallurgists to optimize an alloy's mechanical properties. In the aerospace industry, a superalloy may undergo five or more different heat treating operations to develop the desired properties. This can lead to quality problems depending on the accuracy of the furnace's temperature controls and timer. These operation…
Specification of heat treatment
Usually the end condition is specified instead of the process used in heat treatment.
Case hardening is specified by hardness and case depth. The case depth can be specified in two ways: total case depth or effective case depth. The total case depth is the true depth of the case. For most alloys, the effective case depth i…
Furnace types
Furnaces used for heat treatment can be split into two broad categories: batch furnaces and continuous furnaces. Batch furnaces are usually manually loaded and unloaded, whereas continuous furnaces have an automatic conveying system to provide a constant load into the furnace chamber.
Batch systems usually consist of an insulated chamber with a steel shell, a hea…
See also
• Carbon steel
• Carbonizing
• Diffusion hardening
• Induction hardening
• Retrogression heat treatment