
A typical CIP cycle consists of many steps which often include (in order):
- Pre-rinse with WFI (water for injection) or PW ( purified water) which is performed to wet the interior surface of the tank and remove residue. ...
- Caustic solution single pass flush through the vessel to drain. ...
- Caustic solution re-circulation through the vessel.
- Intermediate WFI or PW rinse
What is a CIP system used for?
CIP SYSTEMS CIP Systems are typically meant for cleaning the interior surfaces of process equipment. Equipment such as tanks, pipes, and pumps for example. It’s usually a highly sophisticated system, with sensors, heat exchangers, pumps and tanks, all to give the user the most effective and repeatable cleaning.
What is CIP (cleaning in place)?
Cleaning-in-Place (CIP) equipment is best used for cleaning pipelines, vats, heat exchangers, centrifugal machines and homogenizers. CIP systems can vary in amount of automation according to cleaning requirements.
Why use electrolyzed water in industrial CIP applications?
Easy handling, low hazard risk, and low cost are additional advantages of using electrolyzed water in industrial CIP applications. Thus pending further research and approval of the appropriate authorities, CIP using EOW can be an economical and environmentally friendly alternative for use of harmful and dangerous chemicals.
What is the role of chemicals in CIP?
In manual CIP systems, operators often add more chemicals than needed to cleaning cycles. This overcompensating can be costly. Understanding the role chemicals play in your cleaning regimen, and adopting automation for dosing control and concentration monitoring, help to keep those costs in check.
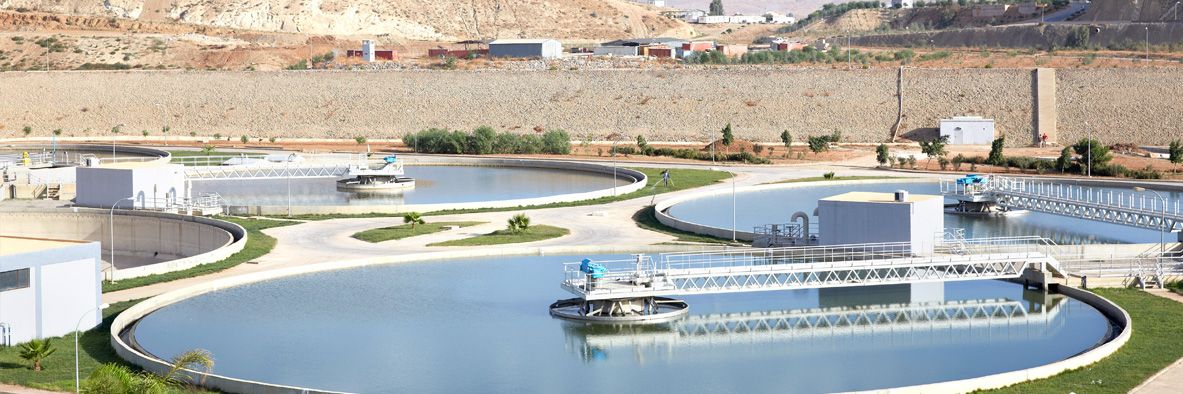
What is CIP water?
Clean-in-place (CIP) is a method of cleaning the interior surfaces of pipes, vessels, process equipment, filters and associated fittings without disassembly.
What chemicals are used in CIP?
Commonly used chemicals for soil removal include Caustic Soda, Phosphoric and Nitric acids, Sodium Hypochlorite (Hypo) and Peracetic Acid (PAA). Caustic Soda is an alkali typically used at 0.5% - 2% volume.
What is a CIP solution?
Cleaning in Place (CIP) systems are designed to automate your cleaning process and efficiently clean and disinfect your enclosed processing equipment. Combined effects of chemicals, turbulence, energy and heat help remove solid, debris and microorganisms from pipework without manual cleaning.
What are the steps of CIP?
CIP systems have a vital role in processing because of the need to keep processing components free of bacteria....Step 1: Pre-rinse. ... Step 2: Caustic Wash – (140° – 185° F) ... Step 3: Intermediate Rinse. ... Step 4: Final Rinse. ... Sanitizing Rinse.
Which acid is used in CIP?
Acid. Nitric acid is the most commonly used wash for scale removal and pH stabilization after a caustic wash. At a typical concentration of 0.5%, it can be used effectively at lower temperatures than caustic solutions, requiring less heating. Phosphoric acid is sometimes used but is somewhat less common.
Why caustic soda is used in CIP?
Sodium hydroxide (caustic) or chlorinated alkaline cleaners (at pH 10–13) are commonly used in food and beverage manufacturing CIP (cleaning in place) processes to remove proteinaceous soils because of their efficacy in peptizing the bonds that hold proteins together.
What is the pH of CIP 100?
pH 2.0 to pH 13.5The special surfactant selected for CIP 100 cleaner is active across the full pH range (from pH 2.0 to pH 13.5), and across the full temperature range from cold to boiling. CIP 100 cleaner is free of perfumes and dyes and is designed to be extremely free-rinsing.
What are CIP requirements?
The CIP rule requires that a bank retain the identifying information obtained about the customer at the time of account opening for five years after the date the account is closed or, in the case of 7 Page 8 credit card accounts, five years after the account is closed or becomes dormant.
Why is CIP important?
CIP equipment helps control, monitor, and document the cleaning methods essential to hygienic processing. As clean-in-place technologies have become more efficient and cost effective, cleaning process systems in-place not only helps ensure product safety but can also add efficiencies to cleaning processes.
What is CIP equipment?
Clean-In-Place (CIP) systems are automated systems used to clean the interior surfaces of food and beverage process pipes, processing vessels, tanks, spiral freezers, mixers, blenders, homogenizers, roasters and associated fittings, without disassembling the process.
What is CIP pump?
CIP system pumps keep product, cleaning chemicals, and water moving through the system during each phase of cleaning. Push-Out (optional) - Prior to the pre-rinse cycle, push out residual product in the process lines using a projectile-type product recovery system.
What is CIP tank in RO plant?
~ CIP is a closed system in which a recirculating cleaning solution (often applied with nozzles) cleans, rinses, and sanitises equipment. The CIP system is typically automatically controlled, and cleaning sequences are assigned the optimum timing for efficient cleaning of all plant parts.
What is CIP in cleaning?
In addition to understanding the chemistry of cleaning and sanitising chemicals, the successful application of cleaning compounds via Clean-in-Place (CIP) procedures also depends on an understanding of the types of soils to be removed and equipment design.
What is a CIP?
CIP can be defined as the ‘cleaning of complete items of plant or pipeline circuits without dismantling or opening of the equipment and with little or no manual involvement on the part of the operator’ ( Bremer et al., 2006 ). Under high turbulence and high velocity, jets are sprayed on the surfaces or cleaning solutions are circulated through the plant ( Romney, 1990 ). Effective periodical CIP prevents the formation of biofilms on equipment surfaces. A large number of factors influence the effectiveness of cleaning which includes the nature and age of the biofilm, composition and concentration of the cleaning agent, time and temperature of cleaning, degree of turbulence of the cleaning solution; and the characteristics of the surface being cleaned ( Stewart and Seiberling, 1996; Changani et al., 1997; Lelievre et al., 2002; Boulange-Petermann et al., 2004 ). Sodium hydroxide (NaOH) at concentrations in the range of 1–5%, is the most common alkaline cleaner used in CIP ( Flint et al., 1997 ). Proteins and carbohydrates are effectively removed by the caustic alkali ( Chisti, 1999 ). The CIP process usually involves a caustic wash, which is followed by an acid wash and then a sanitizer.
What is a CIP circuit?
CIP circuits can be designed to be (1) single use with cleaning solution dumped directly to drain after completion of the CIP cycle or (2) reuse or multi-use systems. Multi-use CIP systems are often designed to recover final rinse water for use to make up subsequent cleaning solutions. Some or all of the cleaning solution itself can also be saved and reused to minimize chemical usage. In all CIP designs, any final rinse or sanitizing rinse would not be reused in that function but fresh final steps would generally be required by food processing regulations in most regions.
How is dairy equipment cleaned?
Dairy equipment is regularly cleaned using clean-in-place (CIP) operations. CIP is a system of cleaning and sanitising based on circulating chemicals and water without taking the equipment apart (IDF 1979 ). The first step in the cleaning cycle is a water rinse, followed by a caustic wash to remove most of the organic deposit. After a short water rinse, an acidic wash is circulated to remove the mineral soils, followed by a sanitising step ( Henck 1995 ). In the dairy industry, CIP operations make a substantial contribution to water consumption and are responsible for 50–95% of overall waste stream volume and high pH (9–11) ( Gesan-Guiziou et al. 2002). According to the work of Hogaas-Eide (2002), cleaning processes are also major contributors to the total eutrophication potential from dairy processing at 80%; while the corresponding contribution to energy use is approximately 30%.
Is CIP water safe?
It is essential that CIP final rinse water, which is used to flush out foreign matter and disinfecting solutions, is microbiologically safe. Fully automated UV disinfection systems can be integrated with CIP rinse cycles to insure that final rinse water does not reintroduce microbiological contaminants. Although most town supplies are free from coliforms, they are rarely sterile. Resistant to the effects of acid, detergents, steam and chemical sterilants, UV systems are an effective method of providing disinfected water for final rinse systems.
Where is the milking system swabbed?
For each method, eight locations on the milking system were swabbed: one on the inside of the plastic claw, one on the neck of the glass receiver, two on the inside of the rubber liners, two on the inside of the stainless steel elbows, and two on the inside of the stainless steel pipeline.
Can you reuse a CIP rinse?
Some or all of the cleaning solution itself can also be saved and reused to minimize chemical usage. In all CIP designs, any final rinse or sanitizing rinse would not be reused in that function but fresh final steps would generally be required by food processing regulations in most regions.
HOW LONG DOES IT TAKE TO CLEAN IN PLACE UNIT?
Despite the fact that CIP technology has numerous advantages for liquid processing companies, many existing and aged CIP systems are extremely resource-intensive, wasting large amounts of water, energy, and cleaning chemicals.At the very same time, while CIP does not typically involve lengthy dismantling and cleaning tasks, it can still result in significant downtime.While the CIP process is being carried out, manufacturing is halted.
CHALLENGES FOR CIP
A modern CIP system must consider not only the cleaning requirements, but also the overall CIP process' environmental impact. Energy usage, as well as the amount of water and chemicals utilised, must be kept to a minimum.
What happens if you don't optimize your CIP?
When your facility doesn’t optimize CIP, your entire wastewater system could be at risk. If the higher flow rates during CIP and sanitation are not taken into account, undersized equalization tanks may be in place, resulting in poor wastewater treatment.
What chemicals are used in wastewater treatment?
In most food & beverage and pharmaceutical facilities, chemicals like chlorine, caustic soda, phosphoric and nitric acids, sodium hypochlorite (hypo), and peracetic acid (PAA) ...
Why do sanitation and wastewater operators need to communicate?
Therefore, sanitation and wastewater operators must communicate regularly to improve the success of the treatment process. Wastewater operators need to know when sanitation processes occur, the chemicals used, and the volume of water. This keeps all operators on the same page for a more efficient process.
What is a CIP system?
CIP Systems are typically meant for cleaning the interior surfaces of process equipment. Equipment such as tanks, pipes, and pumps for example. It’s usually a highly sophisticated system, with sensors, heat exchangers, pumps and tanks, all to give the user the most effective and repeatable cleaning.
Do CIP systems have higher initial costs?
CIP systems tend to have higher initial costs. ( Smaller, portable CIP/COP systems do exist however, with a lower capital investment than traditional CIP systems.) For more on different types of CIP systems, see our earlier post.
What is emulsify in CIP?
Emulsify water-soluble soil in the cleaning solution for easier transport. Note: Without chemical additives most CIP systems still achieve a reasonable level of cleanliness and safety, but the time, action, and temperatures required to do it increase.
What is the best detergent for a CIP wash?
Softens fats, making them easier to remove. Non-foaming formulation can help reduce pump cavitation and increase efficiency. 2. Acid. Nitric acid is the most commonly used wash for scale removal and pH stabilization after a caustic wash.
What is CSI in sanitary processing?
CSI has the ability to engineer, design, and fabricate a custom clean-in-place system to meet your exact hygienic processing needs. CIP equipment from CSI helps you diagram, control, monitor, and document the cleaning methods that are essential to sanitary processing.
What is CSI in manufacturing?
Central States Industrial Equipment (CSI) is a leader in distribution of hygienic pipe, valves, fittings, pumps, heat exchangers, and MRO supplies for hygien ic industrial processors , with four distribution facilities across the U.S. CSI also provides detail design and execution for hygienic process systems in the food, dairy, beverage, pharmaceutical, biotechnology, and personal care industries. Specializing in process piping, system start-ups, and cleaning systems, CSI leverages technology, intellectual property, and industry expertise to deliver solutions to processing problems. More information can be found at www.csidesigns.com.
