
Bolts are much stronger than screws because they have a larger diameter. The size of the head on a bolt is usually much larger than that of screws so you can use less torque when tightening them Fluid Dynamics. For the most part, screws are round with a point on one end and a flat surface on the other.
Full Answer
What do the markings on the bolts on a bolt mean?
In MRO applications, the markings on the bolts should be noted when replacing worn, damaged or rusted bolts. If the bolt head is rusted or damaged to the point where the markings are unreadable, the equipment manual or OEM should be consulted for the proper fastener specifications.
Are heat treated bolts stronger?
Heat-treated bolts are stronger, but not indestructible. Misuse of fasteners could lead to their breakage and even failure of the entire assembly, equipment or structure. Over-tightening hardened bolts above their torsional strength can result in failure.
What is the difference between screws and bolts?
Even in technical parlance, there is often no distinction made between screws and bolts. The truth is that these terms were in use before the advent of machined threaded fasteners, so they are often used interchangeably.
What happens if you over tighten a bolt?
Over-tightening hardened bolts above their torsional strength can result in failure. Under-tightened fasteners can lead to premature failure due to fretting, fretting fatigue or changes in loading and internal stresses on the fasteners.
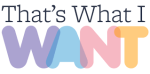
How do you identify different bolts?
0:1019:06How to Measure and identify Bolts - YouTubeYouTubeStart of suggested clipEnd of suggested clipWe basically measure the diameter of the bolt. And we look at the thread pitch and that tells usMoreWe basically measure the diameter of the bolt. And we look at the thread pitch and that tells us basically it gives us clues to whether it's a metric or standard.
How can you tell the material of a bolt?
0:242:01Determining Bolt Grade and Head Markings - YouTubeYouTubeStart of suggested clipEnd of suggested clipYou always want to see 3 radial slashes on the top of the head that mark is a grade.MoreYou always want to see 3 radial slashes on the top of the head that mark is a grade.
What is the gold coating on bolts?
The yellow zinc plating of the fastener refers to the colour of the chromate that is applied once the zinc has been deposited on the fixing or fastener. This chromate prevents the zinc from corroding as well as increasing overall protection.
How can Standard bolts be identified?
Fasteners are identified by four or five attributes; Type, Material, Diameter, Length, and Thread Pitch or Count (machine thread fasteners only).
What do the markings on top of bolts mean?
The markings can identify the standard to which the bolt was made. For instance, if a bolt head contains three radial lines, then it's a Grade 5 bolt. If it contains five radial lines, then the bolt is Grade 8.
What does JH on a bolt mean?
1:426:50Bolt Head Markings: What do they mean? | Fasteners 101 - YouTubeYouTubeStart of suggested clipEnd of suggested clipAnd typically three slashes is going to be grade. Five. Okay you see the JH. There that's aMoreAnd typically three slashes is going to be grade. Five. Okay you see the JH. There that's a manufacturer's marking.
How can you tell if a bolt is cadmium plated?
Cadmium plated stuff should be easy to spot because of it's dull blue-grey mealy appearance. You probably have some old Cd passivated screws in your bits boxes.
How can you tell if a bolt is zinc plated?
Hot dip galvanising or zinc plating can be used on anything from small nuts and bolts to large beams for buildings. The steel is put in a big bath, where the coating is applied. If it's galvanised, it will be dull grey and a little rough. A zinc plated product will be shiny and smooth.
What is the black coating on bolts?
Black Oxide, sometimes called blackening, is the act of converting the top layer of a ferrous material with a chemical treatment. Treating fasteners with a black oxide coating not only adds a nice clean black look but can also add a mild layer of corrosion and abrasion resistance.
What do the markings on a nut mean?
Fasteners commonly have two different markings: a unique manufacturer identification symbol – such as letters or an insignia – and information about the fastener strength. Such markings differ based on how the fasteners were made.
What does 7 on a bolt head mean?
The marks approximately correspond to the following property classes: Head Mark "4": 4.6, 4.8, 5.6, 5.8, 6.8. Head Mark "7": 8.8. Head Mark "8": 9.8. #2.
How do I identify my bolt manufacturer?
Manufacturer's identification mark, e.g., “X” ( on head of bolts and screws and on one end of studs and stud bolts). Manufacture's identification mark, e.g., “X”, applied to head (raised or depressed at option of manufacturer).
Why are fasteners plated with nickel?
Therefore, people take advantage of its high-temperature resistance and lubrication characteristics for fasteners that work at high temperatures to prevent bolts and nuts from oxidizing and seizing . Fasteners are plated with nickel, which is mainly used in places where anti-corrosion and good conductivity are required.
Is phosphating oil better than galvanizing?
Phosphating is cheaper than galvanizing, and its corrosion resistance is worse than galvanizing. Oil should be applied after phosphating. The level of corrosion resistance has a great relationship with the performance of the applied oil. For example, applying general anti-rust oil after phosphating, the neutral salt spray test is only 10-20 hours. Apply high-grade anti-rust oil, it can reach 72~96 hours. But its price is 2 to 3 times that of general phosphating oil. There are two commonly used fastener phosphating, zinc phosphating, and manganese phosphating. Zinc-based phosphating has better lubrication performance than manganese-based phosphating, and manganese-based phosphating has better corrosion resistance and wear resistance. Its operating temperature can reach 225°F to 400°F. Many industrial fasteners are treated with phosphating oil. Because it has a good torque-pre-tightening force consistency, it can guarantee to meet the tightening requirements expected by the design during assembly, so it is used more in the industry, especially the connection of some important parts. High-strength bolts are phosphate, which can also avoid hydrogen embrittlement.
Is chrome plating good for corrosion?
The chromium plating layer is very stable in the atmosphere, is not easy to change color and lose luster, has high hardness and good wear resistance. Chrome plating on fasteners is generally used for decorative purposes. It is rarely used in industrial fields with high anti-corrosion requirements because good chrome-plated fasteners are as expensive as stainless steel. Only when the strength of stainless steel is not enough, chrome-plated fasteners are used instead.
Does silver plated fastener work?
The silver coating can not only prevent corrosion but also act as a solid lubricant for fasteners. Silver loses its luster in the air but can work at 1600 degrees Fahrenheit. Therefore, people take advantage of its high-temperature resistance and lubrication characteristics for fasteners that work at high temperatures to prevent bolts and nuts from oxidizing and seizing. Fasteners are plated with nickel, which is mainly used in places where anti-corrosion and good conductivity are required.
What is a heat treated bolt?
Heat-treated bolts are stronger, but not indestructible. Misuse of fasteners could lead to their breakage and even failure of the entire assembly, equipment or structure. Over-tightening hardened bolts above their torsional strength can result in failure. Under-tightened fasteners can lead to premature failure due to fretting, fretting fatigue or changes in loading and internal stresses on the fasteners. As with any threaded fastening system, the proper torque level must be applied to take full advantage of the bolt’s strength levels. If a soft, nonheat treated nut is used with a hardened bolt, then premature failure is likely to occur in the nut. In bolting applications, ASTM A563 or ASTM A194 grade heavy-duty nuts should be used with strength levels comparable to or compatible with the high-strength bolts selected (Figure 5). Heat-treated bolts are not designed for use in threaded holes because steel plates or structural members are usually soft carbon steel or unhardened alloy steel. In threaded stud applications, the material with the threaded hole should have strength levels compatible with the heat-treated fastener. Washers should meet ASTM F436 specifications for hardened steel washers as well.
What is bolting in power plants?
Oil and gas, petrochemical, chemical and power generation plants contain boilers, pressure piping vessels, valves and process equipment requiring high-strength bolting to maintain seal closure on flanged joints, fittings and closures. Heat-treated bolts are needed to withstand the tensile stresses within the bolts. High horsepower industrial mixers and pump drive shafts often require the higher shear strength provided by heat-treated bolts or pins.
How do steel fasteners change to martensite?
In the quench and temper hardening process, steel fasteners are first heated up to a temperature where their structure is converted into austenite and then quenched or rapidly cooled in water, oil or air to crystal structures that transform to martensite. Next, the martensitic steel fasteners are heated at an intermediate tempering temperature to change the martensite to ferrite, with a very fine dispersion of cementite. Steels cooled slowly from austenitizing temperatures, as well as nonhardenable, low carbon grade steels, form a softer, coarser pearlite structure of ferrite and iron carbides (cementite). The cooling rate has to be fast enough to avoid the formation of pearlite.
What percentage of fasteners are steel based?
About 90 percent of fasteners are steel based and the required strength level is usually developed in steel fasteners using quenching and tempering processes. Accordingly, the terms “high strength” with “heat treated” or “hardened” are often equivocated with the fastener world. However, heat treatment includes a wide range of processes.
What is a carburized pin?
The carburized steel pin or fastener is then conventionally hardened with a quench and temper process. The resulting fastener has a soft, tough, low carbon steel inner core with a case-hardened, high carbon steel outer surface. The hardened surface resists abrasion, wear or cutting. T;he soft, tough inner core prevents fasteners from being snapped or sheared. Pins and sheet metal screws often use case-hardened surfaces. Bolts, shackles and other hardware for locks are often case hardened because they are not easily saw cut and have the toughness to resist fracture from a hammer blow.
What factors affect the selection of stainless steel fasteners?
Mechanical loads and stresses are one aspect of fastener selection. Environmental considerations such as temperature and corrosive media are an additional factor that will impact a project. Highly corrosive environments with low stresses might require stainless steel fasteners.
What are anchor bolts made of?
Structural anchor bolts are made of carbon or fully heat-treated medium alloy steel.
What is the gauge number for UTS bolts?
UTS bolts that have diameters of less than 1/4 inch are provided gauge numbers, but inch measurements are used between 1/4 and 1 inch sizes. The second number of a UTS bolt designates the threads per inch (TPI).
What are the two methods used to manufacture threads?
In fact, there are two methods used to manufactured threads—rolling and cutting —that affect fastener functionality. Cutting requires a blank rod that is the exact diameter as the bolt specification, and excess material is cut away from the blank to create threads.
What threads are less likely to gall?
Coarse threads offer clearance for thread plating and are less likely to gall. These threads are also unlikely to strip if the bolt is made of a soft material. Fine and extra-fine threads can be examined together.
What is the difference between coarse threads and fine threads?
Coarse threads are thicker and more durable than fine-threaded hardware. Coarse-threaded fasteners can also be installed more quickly. For instance, a 3/4-10 UNC requires 10 rotations to install 1 inch of the bolt shaft, while a 3/4-16 UNF would require 16 rotations.
What is thread fit?
Thread fit categorizes the tolerances between the peaks and valleys (crests and roots) of mating threaded hardware. In metric descriptions, thread fit is classified by a number and letter system; lower numbers indicate threads with higher precision and letters indicate tolerance position. In some instances, hardware may actually be labelled with two sets of thread fit measurements. The first label represents the pitch diameter (the imaginary diameter that cuts the threads half way—the distance is equal from the major and minor diameters), while the latter represents the crest diameter, which is the minor diameter on internal threads and the major diameter on external threads. For example, a 4G5G bolt would have a grade 4 pitch internal thread and a grade 4 crest internal thread. When the pitch and crest grades are the same, the notation is simplified; a 4G4G bolt would be labelled 4G instead. Threads with higher tolerance install quicker and are better-suited to accommodate coatings such as a threadlocker.
Why are screws used in worm drives?
They could be used to convey objects linearly or to pump fluids, as in Archimedes’ famous screw pump. Screws were effective as gear reductions in worm drives. Most importantly, they could assemble materials reliably and proficiently. It’s easy to argue that bolts and nuts are just as high-tech today.
What does pitch diameter mean on a thread?
The first label represents the pitch diameter (the imaginary diameter that cuts the threads half way—the distance is equal from the major and minor diameters), while the latter represents the crest diameter, which is the minor diameter on internal threads and the major diameter on external threads.
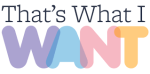
Electro-Galvanized
Hydrogen Embrittlement
- During the production process of fasteners, especially in the picklingbefore plating and subsequent electroplating, the surface absorbs hydrogen atoms, and then the deposited metal coating also traps hydrogen atoms. When the fastener is tightened, the hydrogen atoms are transferred to the stress concentration part, causing the pressure to increase to exceed the stre…
Phosphating
- Phosphating (phosphorization) is a process of chemical and electrochemical reactions to form a phosphate chemical conversion film. The formed phosphate conversion film is called a phosphate film. The thickness of the film is generally 10-15 microns, and the friction coefficient is 0.05. The main purpose of phosphating is: to provide protection to the base metal and prevent the metal fr…
Oxidation
- Blackening is a common method of chemical surface treatment. The principle is to produce an oxide film (ferric oxide) with a thickness of 0.6 to 0.8 microns on the metal surface to isolate the air and achieve the purpose of rust prevention. Blackening treatment can be used when the appearance requirements are not high. The surface blackening treatm...
Cadmium Plating
- Cadmium coating has good corrosion resistance, but it is expensive, so it is not used in general industries and is only used in some specific environments. For example, fasteners for oil drilling platforms and HNA aircraft.
Sherardizing
- Sherardizing is zinc powder solid metallurgical thermal diffusion coating. Its uniformity is good, and a uniform layer can be obtained in threads and blind holes. The thickness of the coating is 10~110μm, and the error can be controlled within 10%. Its bonding strength and anti-corrosion performance with the substrate are the best among zinc coatings (electro-galvanized, hot-dip ga…
Dacromet
- Dacromet, or Dikron, is a new type of anticorrosive coating with zinc powder, aluminum powder, chromic acid, and deionized water as the main components. There is no hydrogen embrittlement problem, and the torque-preload consistency performance is very good. If chromium and environmental issues are not considered, it is actually the most suitable for high-strength fasten…