
Dealing with Distortion During Heat Treat Processing
- The pre-heat step is the first critical distortion prevention step. ...
- At the austenizing temperature, the molecules in steel are ‘in-solution’. That is. they are in a molten state within the shape of the part. ...
- Taking the part from the Cress furnace and transporting it to an air quench rack, or to water or oil quench is next. ...
How to reduce heat-treat distortion?
Proper control of heat-treat distortion is of key importance to reduce production costs in gear manufacturing. The technology of Low Pressure Carburizing (LPC) combined with High Pressure Gas Quenching (HPGQ) offers the potential to reduce the amount of distortion compared to conventional case-hardening technologies.
What determines the post heat treat distortion result?
The shape of the part, or the "design geometry," dictates to a large extent the post heat-treat distortion results. Most often this parameter is fixed for a given application.
How to determine the allowable value of heat treatment distortion?
When the heat treatment is the final process of the workpiece process, the allowable value of the heat treatment distortion should meet the size of the workpiece specified in the drawings, and the distortion quantity shall be determined according to the machining dimension.
How do I prevent distortion when using heat-treated aluminum parts?
Allowing movement of the aluminum by loosely attaching the parts to the rack will allow movement of the aluminum and reduce distortion. Because of the poor strength of the heat-treated aluminum parts, distortion of the parts can occur as they enter the quenchant.
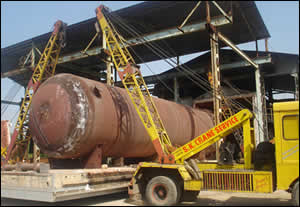
What causes distortion during heat treatment?
Causes of on-heating distortion Ultimately, on-heating distortion is the result of phase transformation gradients within the component. Stresses induced during phase transformations can result in the local yield strength of the material to be exceeded and therefore an appreciable change in shape.
What is the reason for the formation of distortion after quenching?
Causes for Distortion – General Holes, slots or varying section on a part (These areas will quench faster causing differential part cooling.) Part too long, high length/diameter ratio (As a rule, a ratio over eight-to-one results in distortion.)
Which heat treatment process is most susceptible to creating distortion problems?
Quenching is perhaps the area in a heat-treat operation where the problem of distortion will occur.
What is the primary cause of distortion and cracking of the heat-treated part?
Most of the problems in heat-treated parts are attributed to faulty heat-treatment practices (such as overheating and burning, and nonuniform heating and quenching), deficiency in the grade of steel used, part defect, improper grinding, and/or poor part design.
How can you prevent the distortion during quenching in thin parts?
The amount of distortion encountered depends strongly on the nature of the heat treating process that is used. In order to minimize distortion related issues during quenching, heat should be extracted from the component in as uniform a manner as possible.
Which should be added in alloy steel to remove distortion in quenching?
Slow (15-20 second) oils are used where hardenability of steel is high enough to compensate for the slow cooling aspects of this medium. All of these oils are used when quenching carburized and carbonitrided parts.
In which quenching medium the chances of distortion is minimum?
Gas or air quenching will provide the least distortion and may be used if the steel has sufficient hardenability to provide the desired properties.
What can go wrong during heat treatment?
MOST OF THE PROBLEMS in heat- treated parts are attributed to faulty heat- treatment practices (such as overheating and burning, and nonuniform heating and quench- ing), deficiency in the grade of steels used, part defect, improper grinding, and/or poor part design.
During which of the following heat treatments are the components likely to have distortion warping quench cracks and thermal stresses?
Quenching Media This severe cooling rate causes excessive internal stresses within the material which results in distortion or quench cracks within the steel.
How do welders prevent distortion?
The following design principles can control distortion:eliminate welding by forming the plate and using rolled or extruded sections.minimise the amount of weld metal.do not over weld.use intermittent welding in preference to a continuous weld pass.place welds about the neutral axis.More items...
What causes distortion?
Unwanted distortion is caused by a signal which is "too strong". If an audio signal level is too high for a particular component to cope with, then parts of the signal will be lost.
What are the possible causes of distortion?
The principal factors affecting the type and degree of distortion, are:Parent material properties.Amount of restraint.Joint design.Part fit-up.Welding procedure.
What is quenching in heat treatment?
September 2, 2016. Quenching is perhaps the area in a heat-treat operation where the problem of distortion will occur. However, it is not always the quenching that is the cause of the distortion; it is usually “the effect” because it is immediately after quenching that distortion is seen. First, we need to understand the term "distortion" as it ...
What happens to the lattice structure when the temperature is taken to an austenitizing temperature?
If the temperature that the steel is being taken to is an austenitizing temperature, then a phase change will occur. This means that the lattice structure size and construction will change from a 9-atom to a 14-atom structure. In addition, this means that (amongst other things) the size has changed. It has grown!
How is stress induced in steel?
When steel or any metal is mechanically manipulated by machining or mechanical deformation such as forging and rolling, stress is induced into the steel. The only really effective method of the removal of induced stress is by the application of heat.
Can a heat treater cool down?
If the steel is cooled in such a manner, then full transformation can be achieved. The heat treater can only cool down at the rate that the particular quench medium will allow. If the quench medium cools down a little too slowly, the incomplete phase transformation will occur.
How does heat treatment affect the distortion of parts?
One — if not the biggest — factor which affects the distortion of parts is how they are placed and supported in the furnace by the fixturing. Any heat treatment process that requires heating the part to above the transformation temperature causes the part to lose most of the strength that it possesses at room temperature. A part subjected to extended times at elevated temperature, as in carburizing, experiences high temperature creep, and resulting plastic deformation, due to its own weight unless properly fixtured and supported. Single parts are better than stacked parts. If parts have to be stacked, support is important between the layers, especially for thin-walled parts. Also important is making sure that the parts are freely exposed to both the heat transfer medium and the quenching medium. In some instances, fixturing is impractical. In the case of a heavy precision gear, its size may dictate that it be laid directly onto a grid, and if that grid is warped you can expect the gear to attempt to conform to the tray shape during carburizing. Even if the gear is later press quenched this distortion can be difficult if not impossible to correct (if you can get the gear flat again, this still will have affected the precision gear geometry). Furnace trays are often overlooked when trying to find the causes of distortion. As a general rule, if you can see light between a straightedge and the tray, you should not use that tray. Some heat treaters grind the trays flat periodically when there are no other fixturing alternatives. Today, a new generation of high temperature materials has been developed to dramatically reduce dimensional change in trays and fixtures and lengthen useful life. There is no general solution for the design of the loading arrangement for gears. Loading ( Figure 4 A, B) depends on the furnace used, the part geometry, and the cooling medium. For example, research has shown that a horizontal loading in carburizing with continuous furnaces and quenching in oil lead to the lowest statistical (average and standard deviation) degree of distortion. In addition, there is a relationship between the length of time a fixture is in use and the degree of distortion [5].
What is the first step in heat treatment?
A necessary first step in the heat treatment process involves “normalizing, ” a process designed to present a homogenous microstructure to the carburizing process. To reduce overall part distortion, it is highly undesirable to have this homogenization take place during the carburizing cycle of a finished gear component. A separate normalizing cycle removes the problems associated with pearlite and ferrite segregation. Ferritic areas do not transform to the same hardness and stress levels as pearlitic areas when homogenized during the carburizing cycle, resulting in more — not less — distortion.
Why is oil quenching so popular?
Oil quenching is used when the hardenability of the steel is high enough to achieve the desired mechanical and metallurgical properties. The reason oil quenching is so popular is due to its excellent performance results and stability over a broad range of operating conditions.
What is normalizing a part?
Normalizing is a process that involves heating a part above the upper critical temperature and then typically air cooling outside the furnace to relieve residual stresses in a gear blank and to aid dimensional stability. Normalizing is often considered from both a thermal and microstructural standpoint. In the thermal sense, normalizing is austenitizing followed by cooling in still or slightly agitated air or nitrogen. In a microstructural sense, the areas of the microstructure that contain about 0.8 percent carbon are pearlitic, while the areas of low carbon are ferritic. A normalized part is very machinable but harder than an annealed part. It also relieves any residual stresses present from the steel making and forging processes that could cause later distortion during carburizing.
How does gas quenching affect cooling?
As such, this uneven transitory step creates huge temperature differentials and is the major factor in distortion when quenching in these media. Since gas quenching forms no vapor layer, the overall result is lower distortion. It is important to note that the distortion that does occur is therefore different than that produced by oil quenching, and those choosing this alternative must be prepared to adjust their post-grinding procedures.
Why is support important in heat transfer?
Also important is making sure that the parts are freely exposed to both the heat transfer medium and the quenching medium. In some instances, fixturing is impractical.
How long should a rough material be held at a normalizing temperature?
A good normalizing cycle consists of holding the rough material “at temperature” for two hours minimum, or one hour per inch of section thickness. The temperature should be the same or higher than the carburizing temperature later used.
Why is heat treatment distortion important?
Proper control of heat-treat distortion is of key importance to reduce production costs in gear manufacturing.
Why is distortion important in hardening?
Controlling distortion is of key importance during the case hardening process for the production of gear components. By effective control of distortion and the variation of distortion, significant costs in post-heat treatment machining processes can be avoided. In some cases, it is even possible to eliminate all post- machining operations. In other cases, it may be possible to avoid the press-quenching of individual components, resulting in huge cost-benefits.
Why is distortion important in electric vehicles?
With the introduction of E-mobility, proper distortion control has become even more important than in previous days. Distorted gear components cause noise in the transmission. Especially battery-operated electric vehicles (BEVs) and all other electrified vehicles (including hybrids) will require a low noise transmission with high precision components.
What causes distortion in a component?
and they depend on the heat treatment. If the total stress in the component exceeds the yield stress, then distortion of the component takes place. Walton [14] published the numerous potential factors that are influencing distortion in more detail, see Figure 1.
What is the cost impact of distortion?
Distortion has a strong cost-impact, since distorted components need to be hard-machined after heat treatment. Better control of distortion means: Less cycle time per part in hard-machining. Less hard-machining capacity needed. Less tooling cost for hard machining.
How much flatness is reduced in a final drive ring gear?
For a Final Drive Ring gear from a 6-speed automatic transmission, the average change of flatness during heat treatment was reduced by 24 percent when changing from 3D-treatment to 2D-treatment. The average change of roundness was reduced by 50 percent. This improvement in distortion control will result in significant cost savings for subsequent hard turning and grinding process steps.
How many parts were measured in 3D distortion?
In this distortion study, 181 parts from 3D-treatment were measured and 160 parts from 2D-treatment (taken from 20 furnace-runs) were measured with a CNC analytical gear-checker.
What is distortion in heat treating?
Distortion is routinely encountered in industrial heat treating operations, and is an especially important consideration where high accuracy, precision components are concerned. It can result from a wide variety of independent contributing factors. In press quenching these can include, among others:
What happens if vapor bubbles are allowed to form in areas around the surface of the component?
If vapor bubbles are allowed to form in areas around the surface of the component, uneven heat extraction will result that can lead to unacceptable hardness variations and distortion. After this initial quenching stage has been successfully eliminated, lower quenchant flow rates may be safely tolerated.
How does oil flow in a quench chamber?
Oil is pumped into the quench chamber through apertures around the outside diameter of the lower die. As the chamber fills up surrounding the component, oil flows out of the top. If the tooling is properly designed, the direction of oil flow over the component can be adjusted to obtain the best overall results. The elongated apertures at the exit may be adjusted to restrict oil flow, or may be fully opened to maximize flow depending upon the requirements for the part in question. The lower dies are constructed from several different concentric slotted rings that may be rotated to provide full flow or to restrict oil flow to the underside of the part. These particular features can be finely adjusted to help minimize the degree of distortion attributed to uneven heat removal during quenching. Timed segments during the quenching cycle can also be utilized to vary both the oil flow rate and duration in order to establish a well defined quenching recipe for a specific part design.
What temperature should press quench oil be?
The average oil temperature for most press quenching operations typically falls somewhere within the range of approximately 75ºF to165 ºF, depending upon the material in question, the nature of the quenching operation, the type of quench oil being used, and post heat treat property requirements. Average quench oil temperatures exceeding 140ºF should generally be avoided as a precaution to prevent damage to the machine seals that are used to contain the quench oil. Proper and routine maintenance of the quench oil bath is an often neglected aspect of the press quenching process and can lead to unexpected variations in the hardening response of the materials processed in these types of systems. As the quench oil continues to be used, the oil additives gradually break down, and fine particulates can accumulate over time even if the oil is continuously filtered. If left undetected, this can lead to accelerated quench rates which can compromise the integrity of the oil quenching process.
Where is the hot bearing race on a quenching machine?
Figure 3: Hot bearing race positioned on the lower die assembly of a quenching machine just before it is retracted into the machine for quenching. Note the segmented die tooling and individual slotted rings. The slotted rings may be independently adjusted to control the flow of oil over the part being quenched. (Photograph courtesy of The Gleason Works, Rochester, NY).
Does press quenching eliminate heat?
Although press quenching cannot eliminate these effects, its use can help to minimize their contribution to the overall distortion that is produced during heat treatment. The amount of distortion encountered depends strongly on the nature of the heat treating process that is used. In order to minimize distortion related issues during quenching, ...
What causes distortion during quenching?
Distortion during quenching is caused by differential cooling, and differential thermal strains developed during quenching. These thermal strains could be developed center-to-surface, or surface-to-surface. This differential cooling can be caused by large quench rates, so that the center is cooled much slower than the surface (non-Newtonian cooling) or by non-uniform heat transfer across the surface of the part.
What are the problems with aluminum heat treatment?
Of all the possible “defects” occurring during the heat treatment of aluminum, distortion during quenching is the most common. It is probably responsible for most of the non-value-added work (straightening) and costs associated with aluminum heat-treating.
Why is aluminum more prone to quenching distortion than steel?
Aluminum is more prone to quenching distortion than steel. This is because solution heat-treating temperatures are so close to the liquidus temperature. Aluminum exhibits less strength and greater plasticity than steel at the solution heat-treating temperature (or austenitizing temperature for steel).
Why rack a part so that it enters the quenchant smoothly?
Racking a part so that it enters the quenchant smoothly also offers the benefit that it is more likely to have uniform heat transfer across the part. Distortion is more likely to occur because of horizontal changes in heat transfer than by vertical differences in heat transfer.
What percentage of stretch is used in quenching?
The amount of stretch varies but is generally in the range of 1 to 5 percent . Because the stretch plastically deforms the plate, many dislocations are introduced into the material. This plastic deformation causes the elastic stresses resulting from quenching to be redistributed into a less deleterious amount.
Why is it important to have a higher quench rate?
Much higher quench rates are necessary in aluminum to prevent premature heterogeneous precipitation occurring during quenching, and to maintain supersaturation of the solute. In steel, there is a coupled phase transformation of austenite to martensite. This causes a 3 percent volume change during quenching.
Do water-quenched parts need to be straightened?
This is particularly true for water-quenched parts. Parts must be straightened. This is often much easier in the as-quenched condition before aging. However, there are certain things that must be understood to achieve straight parts.
Why does heat treatment cause distortion?
A material that is placed under a heat treatment process may have surface tearing or burnishing, which then creates stress risers on the part. Excessive stress from machining, particularly from drilling and milling, can likewise distort the material. If there are holes, slots, or varying sections on a part, then these specific areas will most likely quench faster and cause differential part cooling.
What are the factors that affect heat treatment?
Numerous factors such as strength, hardness, toughness, machinability, formability, ductility, and elasticity can all be affected by the heat treatment process. To date, there are various techniques that industries maximise to get their desired products.
How does distortion affect material?
The length of a material may also shrink or grow, depending on its part geometry. Additionally, materials with long parts that are distorted will bend unevenly. And as the distortion occurs, materials with cross holes and slots may shrink and cause stress riser. The concentricity of the material likewise gets lost as its thin tubing adopts and oval shape.
What are the two types of distortion?
Types of Distortion. Heat treatment can cause two types of distortion. One type of distortion is dimensional distortion. This type of distortion occurs whenever the metal material changes volume whenever its crystal structure changes. Whenever the heated parts are subjected under one heat treatment technique, their internal crystal structure ...
Why does metal warp when heated?
Some of the reasons why a metal material warp during heat treatment include rapid heating, overheating, non-uniform heating, cooling, or agitation, oil contamination, huge mass and section change, and asymmetric characteristics .
What is heat treatment?
Heat treatment is a type of metalworking process that is utilised to change and alter the physical and even the chemical properties of a specific metal material. This process typically deals with heating or chilling material to extreme temperatures so that the same material can be either hardened or softened. ...
What are some techniques that can cause distortion?
These techniques include annealing, hardening, case hardening, normalising, tempering, precipitation strengthening, and quenching . While these techniques often promote the transformation of material, there are instances where the heat treatment process can cause distortion.
What factors affect heat treatment costs?
In addition to the furnace, other factors affect the heat-treatment costs include: Scale and debris (very difficult and costly to clean up) Cleanliness. Specific carburize area or section (When specific areas on the part require carburizing, the remaining areas must have the carbon removed after carburizing.)
What happens if you have a high length/diameter ratio?
Part too long, high length/diameter ratio (As a rule, a ratio over eight-to-one results in distortion. )
Can heat be removed from a part?
Irrespective of the effective case depth specified, for a given geometry and loading arrangement, heat can only be removed from the part by the quench medium at a fixed rate. This means that even though the depth of 50 HRC may be greater if a deeper effective case depth is specified, the depth of the surface layer where the hardness is 58 HRC is not proportionally deeper and, as a result, excessive grinding sacrifices surface hardness.
What are the three stages of heat treatment?
In fact, there are many forms of heat treatment process applied in industry, and their basic processes are the thermal processes which are composed of three stages: heating, heat preservation, and cooling. In the whole heat treatment process, we need to use all kinds of heating furnace, since metal heat treatment was done in the heating furnace. (such as annealing, quenching, and tempering, etc). Therefore, temperature measurement is an important parameter measurement of heat treatment. If the temperature measurement is not accurate, the heat treatment process specification can’t be implemented correctly, resulting in the product quality decline or even scrapped. So temperature measurement and control are crucial to the heat-treatment process and also the key factor affecting the deformation.
Why is heat treatment important?
The heat treatment process is an important means to obtain excellent performance of various metal materials. Sometime, reasonable choice material and various machining processes can’t meet the requirements of the mechanical properties, physical properties, and chemical properties of metal parts. At this time, the heat treatment process is crucial to them.
How does hot oil quenching affect deformation?
The cooling capacity of oil is also critical to deformation. In addition to this, the stirring method and speed of quenching will also affect the deformation. When metal heat treatment cools faster, the more uneven the cooling, the greater the stress, and the greater the deformation of the die. Of course, we can use the pre-cooling method to reduce the deformation on the premise of ensuring the hardness of the mold; and we also can use fractional cooling quenching to reduce the thermal stress and tissue stress of metal to reduce the deformation. For many high degrees of complexity or precision workpiece, using isothermal quenching can significantly reduce the deformation of metal parts.
What should be avoided in a round angle transition?
The workpiece should avoid sharp cornets, grooves, and so on, and the round angle transition should be made at the thickness of the workpiece and the steps.
Is a thin part cold or hot?
After metal heat treatment, the thin part is always cold fast than the thick one in the cooling process. In the case of meeting the actual production needs, the thickness of the workpiece should be minimized and the section of the parts should be uniform, so as to reduce the distortion and cracking tendency of the stress concentration in the transition zone.
Does heat treatment reduce deformation?
But how to balance and maintain these two relationships? Today, we will introduce 4 ways to reduce the deformation of heat treatment as much as possible.

Factors That Influence Distortion
Importance of Normalizing
- A necessary first step in the heat treatment process involves “normalizing,” a process designed to present a homogenous microstructure to the carburizing process. To reduce overall part distortion, it is highly undesirable to have this homogenization take place during the carburizing cycle of a finished gear component. A separate normalizing cycle ...
Part Size
- Within the industry, the benefits of normalizing small gears–typically those under 5″ (125 mm) or certain AGMA classes of gears–has been the subject of intense scrutiny and investigation. On large gears, manufacturers have been able to demonstrate more consistency and lower distortion which results in a number of benefits (less time in finish machining operations, reduced scrap ra…
Influence of Equipment Design
- The elimination of equipment-induced variability is perhaps the least recognized yet most significant factor with respect to producing consistency in the heat treatment process. Understanding this aspect of the overall process results in predictable, and repeatable, distortion patterns. The areas of primary focus are: • Fixture design (tray/grid flatness, basket and support …
Quench Variables and Quench Tank Design
- Quench-related variables also have a significant affect on part distortion. In general, the selection of a quench medium depends on the following general factors: • Cooling Rate (measured by the efficiency, or “speed” of an oil quench media). • Mechanisms of Heat Removal (largely dependent on part geometry for a given material which dictates the requirements of the quench system). • …
Influence of Material
- Gears under load are subject to gradient stresses both on the active flank and at the root fillet. Proper material selection, as well as heat treatment, will produce strength gradients that are adequate to withstand the stress gradients and provide an acceptable margin of safety. In all gears, the choice of material must be made only after careful consideration of the performance …
Influence of Design Factors
- A number of other design factors are often overlooked as contributing to distortion related issues. These include: • Large, heavy sections adjacent to small, thin sections • Section radii • Helix unwind • Holes Designs with heavy sections adjacent to thin sections or with sharp radii should be avoided since they will almost certainly create distortion issues. The use of as large a radius as …
References
- Edenhofer, B, Grafen, W., and Muller-Ziller, J., Umgang mit der Verzugsproblematik in der industriellen Warmebehandlungspraxis, HTM 6/2003, pp. 328-335 (in German).
- Herring, D.H., Lindell, G. D., Breuer, D.J., and Matlock, B., An Evaluation of Atmosphere and Vacuum Carburizing Methods for the Heat Treatment of Gears, SAE Off-Highway Road Conference, Las Vegas,...
- Edenhofer, B, Grafen, W., and Muller-Ziller, J., Umgang mit der Verzugsproblematik in der industriellen Warmebehandlungspraxis, HTM 6/2003, pp. 328-335 (in German).
- Herring, D.H., Lindell, G. D., Breuer, D.J., and Matlock, B., An Evaluation of Atmosphere and Vacuum Carburizing Methods for the Heat Treatment of Gears, SAE Off-Highway Road Conference, Las Vegas,...
- Private Correspondence, Toyota.
- Unpublished research, Twin Disc, Inc.
Introduction
Distortion Mechanisms and High Pressure Gas Quenching
Lean Heat Treatment
Distortion Studies – Comparison Between 3D-Treatment and 2D-Treatment
Summary
- Proper control of heat-treat distortion is of key importance to reduce production costs in gear manufacturing. The technology of Low Pressure Carburizing (LPC) combined with High Pressure Gas Quenching (HPGQ) offers the potential to reduce the amount of distortion compared to conventional case-hardening technologies. The amount of distortion can be...
References