
For the higher alloyed tool steels processed over 2000°F (1095°C), the quench rate from about 1800°F (980°C) to below 1200°F (650°C) is critical for optimum heat-treat response and material toughness. No matter how tool steels are quenched, the resulting martensitic structure is extremely brittle and under great stress.
How much do tool steels grow during heat treatment?
Most tool steels grow between about 0.0005 and 0.002 inch per inch of original length during heat treatment. This varies somewhat based on a number of theoretical and practical factors. Most heat treaters have a feel for what to expect from typical processes.
Is tool steel heat treated?
Tool steel is generally used in a heat-treated state. With a carbon content between 0.7% and 1.5%, tool steels are manufactured under carefully controlled conditions to produce the required quality. The manganese content is often kept low to minimize the possibility of cracking during water quenching.
Is there a shortcut to heat treat a tool?
Although it may only represent 10% or less of the cost of the tool, the heat treat process is probably the single most important factor in determining the performance of a tool. There is no such thing as an acceptable shortcut in heat treating tool steels. Preheating, or slow heating, of tool steels provides two important benefits.
Why outsource tool steel heat treatment?
The increased use of higher-alloy, air-hardening tool steel grades has made it less practical to conduct tool steel heat treatment in-house, which is why most modern toolrooms outsource the operation to commercial shops that have made the investment in the more sophisticated equipment now required.

Can tool steel be heat treated?
There are four basic steps in the process of heat treating tool steel: Preheating, Heating (also caused austenitizing), Quenching, and Tempering. Depending on the tool steel being treated and the ultimate applications for which it is intended, other steps can be added to the process as well.
Do you need to temper tool steel?
All tool and die steels must be heat treated to develop optimum properties in terms of hardness, strength, tough- ness and wear resistance. Almost all are hardened and tempered.
How hot do you have to get steel to heat treat?
For most grades a 1200/1250 degrees F temperature is used and soak times are similar to tem- pering. Heat treated steels may be similarly stress relieved at a temperature about 25 degrees F lower than the last tempering temperature.
Can you harden tool steel?
Steel is a common durable alloy, and while most steel used in tools is already tough, you can harden it even more to prevent wear and tear. Hardened steel prevents knife blades from dulling and tools from bending and breaking. With a simple heating and quenching process, you can make your steel last for much longer!
How much does it cost to heat treat a knife?
Heat Treat Prices: 1-9 Blades = $10.00/pc. 10-19 Blades = $8.00/pc. $20+ Blades = $6.00/pc.
How hard is D2 tool steel before heat treat?
D2 steel is an air hardening, high-carbon, high-chromium tool steel. It has high wear and abrasion resistant properties. It is heat treatable and will offer a hardness in the range 55-62 HRC, and is machinable in the annealed condition. D2 steel shows little distortion on correct hardening.
How do you harden O1 tool steel?
O1 steels should be heated uniformly to 780-820°C (1436-1508°F) until completely heated through. If needed, the steels can be preheated at 300-500°C (572-932°F). About 30 min/per 25 mm of ruling section is to be provided and then the steels should be immediately quenched in oil.
How do you heat treat S7 tool steel?
S7 should be preheated at 1200 to 1300°F and raised to the hardening temperature of 1725°F, holding at temperature for one hour for each inch of greatest cross-section. Sections 2-1/2-in. or less should be quenched in still air. Upon reaching 150°F, the piece should be tempered without delay.
How do you heat treat A2 tool steel?
Hardening Tools made from A2 tool steel may be hardened by placing them in a furnace maintained at a temperature of 1725/1775°F (940/969°C). Let the tools heat naturally to the furnace temperature, soak for 20 minutes plus 5 minutes per inch of thickness and air quench.
How do you harden tool steel at home?
0:005:25Heat Treating Steel - YouTubeYouTubeStart of suggested clipEnd of suggested clipOil I like peanut oil because it has the highest flashpoint of all the common household oils I don'tMoreOil I like peanut oil because it has the highest flashpoint of all the common household oils I don't like using petroleum oils because they smell terrible.
Why is slow heating important for tool steels?
First, most tool steels are sensitive to thermal shock, and reducing thermal gradients produced by rapid heat rates minimizes the tendency of tool steels to crack. Also, tool steels undergo a volume change when they transform from their annealed microstructure to austenite while heating to elevated temperature. If this volume change occurs non-uniformly, it can cause unexpected distortion, especially in cases where differences in section size exist.
What temperature should steel be tempered at?
In general, use the highest tempering temperature that will provide the necessary hardness for the tool. The rate of heating to and cooling from the tempering temperature is usually not critical. The material should be allowed to cool below 150°F (65°C) and often completely to room temperature between and after tempers. A good rule of thumb is to soak for one hour per inch of thickest section after the entire tool has reached temperature, but in no case less than two hours regardless of size.
What is the hardness of annealed steel?
Tool steels are usually supplied to customers in the annealed condition with typical hardness values around 200-250 Brinell (» 20 HRC) to facilitate machining and other operations. This is especially important for forged tools and die blocks where partial or full air hardening takes place, resulting in a buildup of internal stresses. Dies and tools that may need to be rehardened must be annealed.
Is there such a thing as acceptable short cuts in heat treatment?
For anyone involved with heat treating of tool steels, it is critical to remember that there is no such thing as acceptable short-cuts in the heat-treatment process. As such, applying best practices for preheating, austenitizing, quenching, deep-freezing and tempering is mandatory. Let’s learn more.
What is hardness test?
Hardness testing is the most popularway to check the results of hardening .Hardness is usually the property thatis specified when a tool is hardened.It is easy to test hardness. Thematerial is not destroyed and theapparatus is relatively inexpensive.The most common methods areRockwell C (HRC), Vickers (HV) andBrinell (HBW).
What is case hardening?
Case hardening is a process in whicha finished part is exposed to acarburizing atmosphere and hightemperature simultaneously. Thetemperature range is 850°C–950°C(1560°F–1740°F). This exposuregenerates a layer with higher carboncontent, normally 0.1–1.5 mm thick.After the layer has been formed, thepart is to be quenched in order forthe layer to transform into marten-site with higher carbon content, andit will therefore have a higher hard-ness. Tempering of the part shouldfollow.
How is nitriding performed?
Nitriding is performed by exposingthe parts to some media rich innitrogen under certain physical con-ditions that will result in the diffusionof nitrogen atoms into the steel andthe formation of nitrides . The partsurface will then be harder and havea higher wear resistance in its outerlayer.
What is load thermocouple?
A load thermocouple provides extremely accurate control of actual time at temperature. Various die details will be cut from these blanks after hardening.
Is heat treating a toolmaking trade?
In years gone by most toolmaking apprenticeship programs taught metallurgy basics; heat treating was considered a basic of the toolmaking trade.
How much oil should I use for steel quenching?
The oil should be a warm, thin quenching oil that contains a safe flash point. Olive oil has been used as a sub stitute. As a rule of thumb, there should be a gallon of oil for each pound of steel. For, warming the oil before quenching, you may heat a piece of steel and drop it in the oil. 1.)
Do furnace blades need to be cooled before drawing?
Sometimes the blades will be cooled before the furnace comes down. In this case keep the blades warm (place near the furnace door) or you may use the kitchen oven for drawing. It is important on all grades thato they do not cool much below the 125°F. temperature before drawing.
How to test Rockwell hardness?
In Rockwell hardness testing, a conicaldiamond is first pressed with a force F0, and then with a force F0+F1 against aspecimen of the material whose hard-ness is to be determined. After unload-ing to F0, the increase (e) of the depthof the impression caused by F1 is deter-mined. The depth of penetration (e) isconverted into a hardness number
What is hardness test?
Hardness testing is the most popularway to check the results of hardening .Hardness is usually the property that isspecified when a tool is hardened.It is easy to test hardness. The mate-rial is not destroyed and the apparatusis relatively inexpensive. The most com-mon methods are Rockwell C (HRC),Vickers (HV) and Brinell (HBW).
What is hard chromium plating?
Hard chromium plating can improve thewear resistance and corrosion resistanceof a tool. Hard chromium plating is doneelectrolytically. The thickness of theplating is normally between 0,001 and0,1 mm (0,00004–0,004 inch). It can bedifficult to obtain a uniform surfacelayer, especially on complex tools, sinceprojecting corners and edges may re-ceive a thicker deposit than large flatsurfaces or the holes. If the chromiumlayer is damaged, the exposed steel maycorrode rapidly.
What is Brinell hardness?
In Brinell hardness testing, a Tungsten(W) ball is pressed against the materialwhose hardness is to be determined.A fter unloading, two measurements ofthe diameter of the impression aretaken at 90° to each other (d1 and d2)and the HBW value is read off a table,from the average of d1 and d2.When the test results are reported,Brinell hardness is indicated with theletters HBW and a suffix indicating balldiameter, the mass with which the load
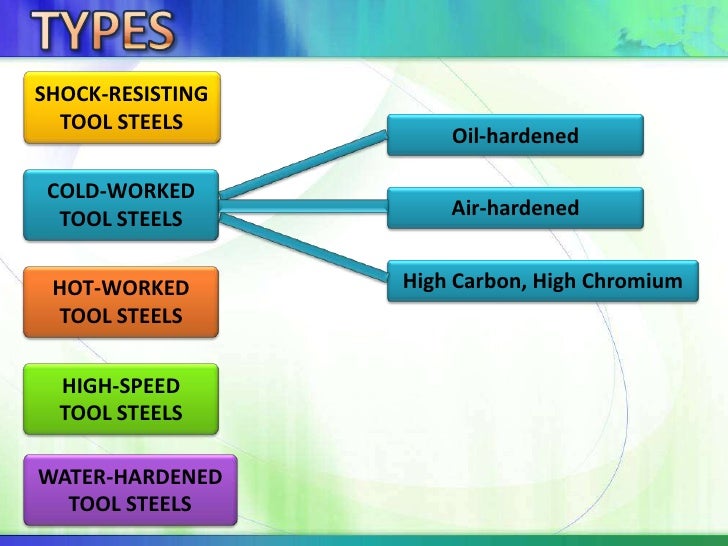