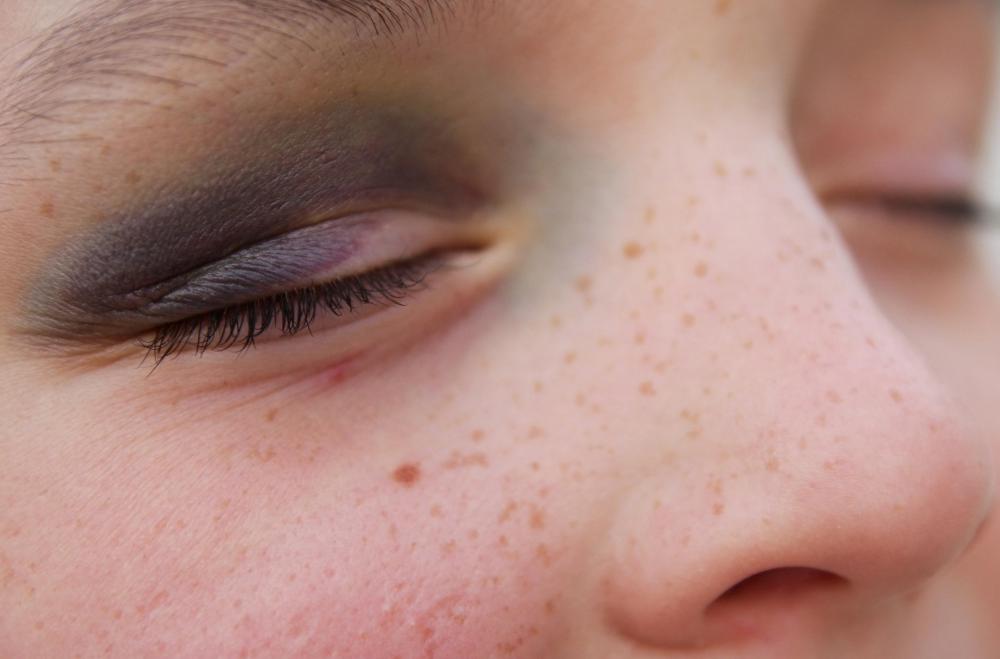
5 Types of Heat Treating and Their Purpose in Precision Machining
- HARDENING. In heat treating to harden a metal, the metal is heated to a temperature where the elements in the metal become a solution.
- CASE HARDENING. In the process of case hardening, the external layer of metal is hardened while the interior metal remains soft.
- ANNEALING. ...
- NORMALIZING. ...
- TEMPERING. ...
What is the normalizing heat treatment?
What is the Normalizing Heat Treatment?
- Normalizing Heat Treatment & Process. The metal is heated in a furnace for normalizing heat treatment process. ...
- Carbon Steel Normalizing. Carbon steel contains carbon in the range of 0.12 to 2%. ...
- Microstructure in Normalizing. ...
- Normalizing Equipment. ...
- Application of Normalizing. ...
What is tempering and its process?
When Is Tempering Used?
- Tempering is most commonly used following a quenching operation. Heating a carbon steel and rapidly quenching it can leave it too hard and brittle. ...
- Tempering can reduce the hardness and relieve the stress of a welded component. ...
- Work hardened materials often require tempering. ...
What is the heat treating process?
Heat treatment methods
- Normalising. This process consists of homogenisation or grain refinement to obtain uniformity in the material microstructure.
- Annealing. In this process, the material is heated beyond its upper critical point (the temperature above which austenite forms), soaked there and then cooled at a slow rate.
- Surface Hardening. ...
- Hardening. ...
- Tempering. ...
What is aging heat treatment?
The heat treatment aging process involves elevating the temperature of an alloy to change its properties. The process accelerates changes in an alloy’s properties through a series of heat treatments. When the aging process occurs at room temperature, the chemical properties of newly cast and forged metals will transform and settle very slowly.

What are the four types of heat treatment?
In this post, we'll cover the four basic types of heat treatment steel undergoes today: annealing, normalizing, hardening, and tempering.
What are the 3 stages of heat treatment process?
Stages of Heat TreatmentThe Heating Stage.The Soaking Stage.The Cooling Stage.
What are the five basic heat treating processes?
Heat Treatment Process StepsHeating. Jet engine parts going into a furnace. ... Holding. During the holding, or soaking stage, the metal is kept at the achieved temperature. ... Cooling. After the soaking stage is complete, the metal must be cooled in a prescribed manner. ... Annealing. ... Normalising. ... Hardening. ... Ageing. ... Stress Relieving.More items...•
What is heat treatment?
Heat treatment refers to the controlled process of heating and cooling a material in order to improve its properties, performance, and strength. Most metals and alloys are heat treated in one way or another, and the understanding and science of heat treatment have been developed over the past 100 to 125 years.
What is heat treatment and types?
Heat treatment involves the use of heating or chilling, normally to extreme temperatures, to achieve the desired result such as hardening or softening of a material. Heat treatment techniques include annealing, case hardening, precipitation strengthening, tempering, carburizing, normalizing and quenching.
What are the types of annealing?
What Is Annealing (7 Types of Annealing Process)Complete annealing.Isothermal annealing.Incomplete annealing.Spherification annealing.Diffusion annealing (uniform annealing)Stress Relief annealing.Recrystallization annealing.
What are the types of heat processing?
Following are the different types of heat treatment processes:Annealing.Normalizing.hardening.Tempering.Nitriding.Cyaniding.Induction Hardening.Flame Hardening.
What is annealing used for?
Annealing is used to reverse the effects of work hardening, which can occur during processes such as bending, cold forming or drawing. If the material becomes too hard it can make working impossible or result in cracking.
What is flame hardening?
Flame hardening is a heat treatment process where oxyfuel gas flames are directly impinged onto the gear-tooth surface area to be hardened which is then subjected to quenching. It results in a hard surface layer of martensite over a softer interior core.
Who uses heat treatment?
Heat treatment is commonly used to alter or strengthen materials' structure through a heating and cooling process. It can be applied to both ferrous and non-ferrous metals, and there are a number of different methods of heat treatment.
What is critical temperature in heat treatment?
Critical temperature of steel defines phase transition between two phases of steel. As the steel is heated above the critical temperature, about 1335°F (724°C), it undergoes a phase change, recrystallizing as austenite.
What is recrystallization temperature?
The recrystallization temperature of alloys may vary from 340° to 400°C (650° to 750°F). The temperature and the rate of heating are specific to the alloy and must be carefully applied.
What Is Heat Treatment?
Types of Heat Treatment Processes
- Following are the different types of heat treatment processes: 1. Annealing 2. Normalizing 3. hardening 4. Tempering 5. Nitriding 6. Cyaniding 7. Induction Hardening 8. Flame Hardening Read Also: 1. What is Metal Casting Process? A Complete guide 2. List of Mechanical Properties of materials
Types of Heat Treatment
Purpose of Heat Treatment of Steel
Conclusion
Overview
Furnace types
Furnaces used for heat treatment can be split into two broad categories: batch furnaces and continuous furnaces. Batch furnaces are usually manually loaded and unloaded, whereas continuous furnaces have an automatic conveying system to provide a constant load into the furnace chamber.
Batch systems usually consist of an insulated chamber with a steel shell, a hea…
Physical processes
Effects of composition
Effects of time and temperature
Techniques
Specification of heat treatment
See also
Stages of Heat Treatment Process
Purpose of Heat Treatment
Classification of Heat Treatment Processes
- Various heat treatment processes can be classified as follows: 1. Annealing. 2. Normalizing. 3. Hardening. 4. Tempering. 5. Case hardening. 6. Surface hardening. 7. Diffusion coating.
Annealing
Normalizing
Hardening
Tempering
Surface Hardening Or Case Hardening.