
Heat treatment involves heating of metal in the solid-state and then subsequently cooled at varied cooling rates. It is very important manufacturing process that can not only help the manufacturing process but can also improve the product, its performance, and its characteristics in many ways.
What is the heat treatment process?
In very simple words I am going to explain the heat treatment process consists of a succession of heating and cooling cycles applied to a metal or alloy in order to obtain the desired properties, such as hardness, ductility, tensile strength, toughness, grain size, etc.
What is heat treatment in the material science industry?
Conclusion. Heat treatment is a very essential process in the material science industry to improve the properties of metal suitable for commercial purpose. It is one of the key processes that help in gaining the desired mechanical and chemical properties of metals. That’s all I have in this article.
What are heat treated parts made of?
It is very closely linked to the manufacture of steel products: about 80 percent of heat treated parts are made of steel. These include steel mill output such as bar and tube, as well as parts that have been cast, forged, welded, machined, rolled, stamped, drawn or extruded.
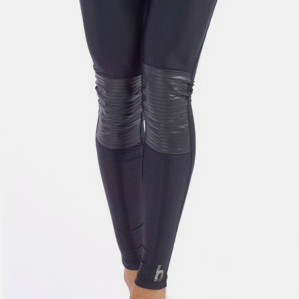
How do you create a heat treatment?
Approach to Design of the Heat Treatment CycleSelection of austenizing temperature,Adequate soaking time for thermal homogenization of the component,Selection of appropriate quenching media to obtain required cooling rate,Cooling the component to the room temperature,Tempering temperature and time.
What materials are used for heat treatment?
Ferrous heat-treated metals often include cast iron, alloys, stainless steel and tool steel, whereas some heat-treated non-ferrous metals include aluminum, copper, brass and titanium.
What are the 3 stages of heat treatment process?
The stages of the heat treatment process include heating, soaking, and cooling.Heating: Heating is the first stage in a heat-treating process. ... Soaking: Soaking is the stage at which the complete part of the heated metal completely changes in its structure. ... Cooling: The third stage of heat treatment is cooling.
How is heat treatment?
Heat treatment involves the use of heating or chilling, normally to extreme temperatures, to achieve the desired result such as hardening or softening of a material. Heat treatment techniques include annealing, case hardening, precipitation strengthening, tempering, carburizing, normalizing and quenching.
What are the five basic heat treatment process?
There are five basic heat treating processes: hardening, case hardening, annealing, normalizing, and tempering. Although each of these processes bring about different results in metal, all of them involve three basic steps: heating, soaking, and cooling. Heating is the first step in a heat-treating process.
How many types of heat treatment are there?
4 TypesWhat are the 4 Types of Heat Treating Processes? Common types of heat treating methods include annealing, hardening, quenching, and stress relieving, each of which has its own unique process to produce different results.
Why quenching is done?
quenching, rapid cooling, as by immersion in oil or water, of a metal object from the high temperature at which it has been shaped. This usually is undertaken to maintain mechanical properties associated with a crystalline structure or phase distribution that would be lost upon slow cooling.
Why hardening is done?
Metal Hardening Hardened materials are usually tempered or stress relieved to improve their dimensional stability and toughness. Steel parts often require a heat treatment to obtain improved mechanical properties, such as increasing increase hardness or strength.
What is heat treatment process PDF?
Heat treatment consists of heating the metal near or above its critical temperature, held for a particular time at that finally cooling the metal in some medium which may be air, water, brine, or molten salts.
Why is heat treated in steel?
Heat Treatment Does a Lot for Steel The softening of steel allows for metal working operations such as deep drawing, cold forging and machining. Thus, steel also increases its strength, making the material ductile or more flexible, while also introducing wear-resistance characteristics, making the material tougher.
How do they heat steel?
Methods of Heating and HardeningAnnealing - Heating and then slowly cool steel to refine it and make it softer.Carburizing - Adding carbon to the surface with heat and carbon-rich substances.Case hardening - Carburizing and quickly cooling steel to keep the center soft while the rest hardens.More items...
How is steel heat treated?
The normal processes used for the heat treatment of steels are (i) annealing, (ii) normalizing, (iii) hardening, and (iv) tempering. Annealing is a heat treatment process which involves heating and cooling. The process is normally used for the softening of steel.
Why is heat treatment important?
It is very important manufacturing process that can not only help the manufacturing process but can also improve the product, its performance, and its characteristics in many ways. By Heat Treatment process, Example: The plain carbon steel. The following changes may be achieved: The hardness of Steel may be increased or decreased.
Why is heat treated steel used?
This heat treatment process is usually carried for low and medium carbon steel as well as alloy steel to make the grain structure more uniform and relieve the internal stresses.
What are the changes in steel?
The following changes may be achieved: The hardness of Steel may be increased or decreased. Internal stresses that are set up due to cold or hot working may be relieved. The machinability of Steel may be enhanced. The mechanical properties like tensile strength the Talati shock resistance toughness etc may be improved.
What is nitriding in steel?
Nitriding is a process of surface hardening in which nitrogen gas is used to obtain a hard surface for the Steel. In this process, the Steel parts are heated in an atmosphere of ammonia (NH 3 ) for a prolonged period and then cooled slowly.
How is steel sampling done?
Sampling is done by reheating the hardened Steel to some temperature below the lower critical temperature and then quenching in oil or salt bath.
Why is annealing done?
Annealing is carried out for such parts to remove the internal stresses and make them more ductile and less brittle.
What is recrystallization in steel?
This causes complete recrystallization in steel to form New grain structure. This will release the internal stresses previously the strip in the steel and improve the machinability.
What is heat treatment?
Heat treatment is a heating and then cooling process using predefined methods to achieve desired mechanical properties like hardness , ductility, toughness, strength, etc. It is the combination of thermal, industrial, and metalworking processes to alter the mechanical properties and chemical properties of metals.
What is the first step in heat treatment?
The first step in the heat treatment process is heating the metal. The temperature depends on the types of metal and the technique used. Sometimes you need to heat the outer surfaces of the metal, and sometimes you need to heat the whole body. That depends on what kind of alteration you want in the mechanical structure.
How does heat treatment help metals?
Heat treatment assist in improving the ductility of metal in the annealing process. Heat treatment helps in hardening metals. Case hardening helps in hardening only the outer surface of the metal piece keeping the rest of the portion soft and ductile. Machinability of metals gets improved.
How is annealing done?
Annealing is done by heating the metals at the above critical temperature , hold them there for some time and then cool it at a very slow rate in the furnace itself. Annealing is usually done on ferrous and non-ferrous metals to reduce hardness after the cold working process.
What is annealing in metals?
Annealing. Annealing is a heat treatment process that is used to soften the metal. In other words, annealing helps to improve ductility, machinability, and toughness. On the flip side, the hardness of metals gets reduced. Annealing does this by changing the microstructure of metals.
How does tampering work?
Tampering is a very common process for machine tools, knives, etc. Tampering is usually done by heating the metal at a relatively low temperature. The temperature depends on the required mechanical properties of metals.
How many types of annealing processes are there?
There are two types of annealing process which are shown below.
How is heat treated?
Solution treatment involves heating the aluminium to dissolve casting precipitates and disperse the alloying elements through the aluminium matrix. Quenching involves rapid cooling of the hot aluminium to a low temperature (usually room temperature) to avoid the formation of large, brittle precipitates. After quenching the aluminium matrix is supersaturated with solute (alloying) elements. The final operation of ageing involves reheating the alloy to a moderately high temperature (usually 150–200 °C) to allow the alloying elements to precipitate small particles that strengthen the alloy. The heat-treatment process can improve virtually every mechanical property that is important to an aircraft structure (except Young’s modulus that remains unchanged). Properties that are improved include yield strength, ultimate strength, fracture toughness, fatigue endurance and hardness. The heat-treatment process is performed in a foundry using specialist furnaces and ovens, and then the alloy is delivered in the final condition to the aircraft manufacturer. Some large aerospace companies have their own foundry because of the large amount of aluminium alloys used in the production of their aircraft.
Where is heat treatment done?
The heat-treatment process is performed in a foundry using specialist furnaces and ovens, and then the alloy is delivered in the final condition to the aircraft manufacturer. Some large aerospace companies have their own foundry because of the large amount of aluminium alloys used in the production of their aircraft.
How does heat treatment affect fatigue?
The main reason for the beneficial effect of both heat treatments is the simultaneous effect of higher hardness and compressive residual stresses in the case. Distribution and properties of plate martensite and retained austenite and in consequence the hardness profile and the residual stresses depend on the carbon profile, the dominant parameter of carburizing. The fatigue fractures start intergranular at the surface; therefore the surface conditions also influence the fatigue behavior. Nitrided microstructures are composed heterogeneously with compound layer and diffusion zone. The crack initiation places, where the applied stresses reach the strength of the microstructures, determine the main influences on the microstructure fatigue behavior. Applied stresses in the range of finite life as well as stress concentrations in the notch root of notched components lead to a stress maximum at the surface and consequently to surface crack initiation. In this case the properties of the compound layer determine the fatigue behavior. Stress amplitudes in the transition range shift the crack start below the surface in the diffusion zone. The fatigue behavior then depends on the hardness of the diffusion zone, the residual stress distribution and, if present, non-metallic inclusions acting as weak points. Low stress amplitude at the infinite life limit and very high cycles to failure again shift the crack start to the surface. Due to the contrary effect of nitriding time on the hardness profile and the residual stress distribution, an optimal nitriding time for the fatigue strength is observed.
How are bicycle tubes made?
The tubes used in bicycles are manufactured by hot working, the plastic deformation of a metal under the influence of an applied external force to change the shape by working the metal above its recrystallization temperature. The factors that affect hot working are the temperature of deformation, rate of deformation or strain rate, and amount of deformation. Success also depends on the method and tooling of hot working. Roll and die quality affect the tube quality. The two major hot working processes involved in tube manufacture are hot rolling and hot extrusion. Hot rolling needs a secondary operation of electric welding to close the seams. Tubes made by hot rolling are weak at the seams, whereas extruded tubes are free of this limitation.
What are the processes involved in the manufacture of a bicycle?
From the foregoing discussion, it is clear that the most important processes involved in the manufacture of the bicycle are welding, machining, heat treatment, painting, inorganic coating, and tube drawing. Effective control of the process variables in Table 10.30 is a prerequisite to obtaining a usable product. A discussion of the process variables associated with these processes follows.
Is heat treatment a good disinfectant?
In addition to that, it is not necessary to prefilter the water before introduction into heat exchangers. As there is no addition of chemicals to disinfect, therefore, no harmful residuals will be produced as by-products. It removes some of the volatile organic chemicals. Simple bo iling is a quick, temporary, and very effective on emergency. On the other hand, the cost of this technique might fluctuate depending on the price of the fuel used for heating the water. Boiling and then subsequent cooling are time-consuming processes. It might impart a stale taste to the water. Minerals (especially calcium) present in water will get deposited inside the heat exchanger tank over a period, reducing the efficacy of the process and thus demanding high maintenance in due course. Expensive protection from recontamination and requirement of large storage areas for treated water are other drawbacks of this technique.
How does heat treatment work?
These tend to consist of either cooling different areas of an alloy at different rates, by quickly heating in a localized area and then quenching, by thermochemical diffusion, or by tempering different areas of an object at different temperatures, such as in differential tempering.
What is a heat treating schedule?
Complex heat treating schedules, or " cycles," are often devised by metallurgists to optimize an alloy's mechanical properties. In the aerospace industry, a superalloy may undergo five or more different heat treating operations to develop the desired properties. This can lead to quality problems depending on the accuracy of the furnace's temperature controls and timer. These operations can usually be divided into several basic techniques.
How is annealing done?
In ferrous alloys, annealing is usually accomplished by heating the metal beyond the upper critical temperature and then cooling very slowly, resulting in the formation of pearlite. In both pure metals and many alloys that cannot be heat treated, annealing is used to remove the hardness caused by cold working. The metal is heated to a temperature where recrystallization can occur, thereby repairing the defects caused by plastic deformation. In these metals, the rate of cooling will usually have little effect. Most non-ferrous alloys that are heat-treatable are also annealed to relieve the hardness of cold working. These may be slowly cooled to allow full precipitation of the constituents and produce a refined microstructure.
What is the purpose of heat treating metals?
grain size and composition) is one of the most effective factors that can determine the overall mechanical behavior of the metal. Heat treatment provides an efficient way to manipulate the properties of the metal by controlling the rate of diffusion and the rate of cooling within the microstructure. Heat treating is often used to alter the mechanical properties of a metallic alloy, manipulating properties such as the hardness, strength, toughness, ductility, and elasticity .
How does salt heat up?
Parts are loaded into a pot of molten salt where they are heated by conduction, giving a very readily available source of heat. The core temperature of a part rises in temperature at approximately the same rate as its surface in a salt bath.
Why are metals annealed?
Most non-ferrous alloys that are heat-treatable are also annealed to relieve the hardness of cold working.
What is the process of heating something to alter it?
Process of heating something to alter it. Heat treating furnace at 1,800 °F (980 °C) Heat treating (or heat treatment) is a group of industrial, thermal and metalworking processes used to alter the physical, and sometimes chemical, properties of a material. The most common application is metallurgical. Heat treatments are also used in the ...
How does heat treatment work?
Prior to these defects in the crystal lattice structure of the metal are the main source of plasticity. The heat-treating process addresses these deficiencies in the steel by making the metal into a reliable solution with fine particles to strengthen the metal. Once this phase is achieved the solution is rapidly quenched to trap the particles in the solution.
What is heat treating?
Heat treating is a pre and post-manufacturing process which is used to change a number of properties of metals and their alloys. The primary use of heat treating is to make the metal suitable for a particular application.
What happens when ferrite is heated?
However, when the ferrite is heated up to high temperatures above 1333°F the structure changes from BCC to FCC, therefore allowing more carbon to be absorbed, this is called austenite. The austenite phase allows the cementite to dissolve into austenite if this is allowed to cool slowly the carbon will separate out of the ferrite and the structure will change back from FCC to BCC. The small pockets of cementite will reform within the ferrite and the steel will revert to having the same properties it did prior to being heated.
Why is annealing used?
Annealing is also used to make the metal more stable, allowing harder metals to be machined without the risk of cracking.
What is the process of tempered metal?
Tempering. Tempering is a process by which heat treating is used to increase resilience in iron-based alloys such as steel. The natural properties of iron-based metals make them very hard but also brittle, in fact, they may be too brittle for the most common uses.
Why is tempering metal important?
By tempering the metal, it’s hardness, ductility and strength can be changed to make it easier to machine. The metal is heated to a temperature just below the critical point as this will reduce the brittleness of the metal whilst still maintaining its hardness. A higher temperature is used to make a more ductile metal.
How does heat treatment affect metal?
Heat treating can affect a number of different aspects of the metal including strength, hardness, toughness, machinability, formability, ductility, and elasticity. It can also affect the physical and mechanical properties of metal to change the use of the metal or alter future work on the metal.
What is the purpose of heat treatment?
The purpose of heat treatment is to make a metal more useful by changing or restoring its mechanical properties.
What are the different types of heat treating?
The various types of heat-treating processes are somewhat similar because they all involve the heating and cooling ; they differ in the heating temperatures and the cooling rates used and the final results. The usual methods of heat-treating ferrous metals (metals with iron) are annealing, normalizing, hardening, and tempering. Most nonferrous metals can be annealed, but never tempered, normalized, or case-hardened.
What is the process of soaking metal?
After the metal is heated to proper temperature, it is held at that temperature until the desired internal structural changes take place. This process is called SOAKING. The length of time held at the proper temperature is called the SOAKING PERIOD, which depends on chemical analysis of the metal and the mass of the part. When steel parts are uneven in cross section, the soaking period is determined by the largest section.During the soaking stage, the temperature of the metal is rarely brought from room temperature to the final temperature in one operation; instead, metal is slowly heated to a temperature just below the point at which the change takes place and then it is held at that temperature until the heat is equalized throughout the metal. This process is called PREHEATING. Following pre-heat, metal is quickly heated to final target temperature. When apart has an intricate design, it may have to be preheated at more than one temperature to prevent cracking and excessive warping. For example, assume an intricate part needs to be heated to 1500°F (815°C)for hardening. This part could be slowly heated to 600°F (316°C), soaked at this temperature, then heated slowly to 1200°F (649°C), and then soaked at that temperature. Following the final preheat, the part should then be heated quickly to the hardening temperature of 1500°F (815°C).
How to cool metals?
To cool the metal, it can be placed in direct contact with a COOLING MEDIUM, either gas or liquid, or solid or any combination of these . The cooling rate depends on metal and the end properties. The rate of cooling depends on cooling medium as well; therefore, the choice of a cooling medium has an important influence on end properties.Quenching is the procedure used for cooling metal rapidly in oil, water, brine or other medium. Because most metals are cooled rapidly during the hardening process, quenching is usually associated with hardening;however, quenching does not always result in increased hardness; for example to anneal copper, it is usually quenched in water. Other metals such as air-hardened steels are cooled at a relatively slow rate for hardening.Some metals crack or warp easily during quenching while others suffer no effects; therefore, the quenching medium must be chosen to fit metal. Brine or water is used for metals that require a rapid cooling rate, and oil mixtures are more suitable for metals that need a slower rate of cooling. Generally, carbon steels are water-hardened and alloy steels are oil-hardened. Non-ferrous metals are normally quenched in water.
What is stage 2 in metal treatment?
Stage 2 – Soaking (holding) metal at a given temperature for a given time and cooling the metal to room temperature. Stage 3 – Cooling the metal to room temperature. steps in heat treatment.
What is the process of holding a metal at a certain temperature?
This process is called SOAKING. The length of time held at the proper temperature is called the SOAKING PERIOD, which depends on chemical analysis of the metal and the mass of the part.
How to achieve uniform temperature?
Uniform temperatures are attained by slow heating. The heating rate of a part depends on several factors. One important factor is the heat conductivity of the metal. A metal with a high-heat conductivity heats at a faster rate than one with a low conductivity. Also, the condition of the metal determines the rate at which it may be heated.
What are the steps of heat treating?
Heat treating processes require three basic steps: Heating to a specified temperature.
How much does heat treatment add to metal?
Heat treating adds about $15 billion per year in value to metal products by imparting specific properties that are required if parts are to function successfully. It is very closely linked to the manufacture of steel products: about 80 percent of heat treated parts are made of steel.
Why is aluminum alloy heat treated?
It is also a vital step in the manufacture of nonferrous products. For example, aluminum alloy automotive castings are heat treated to improve hardness and strength; brass and bronze items are heat treated to increase strength and prevent cracking; titanium alloy structures are heat treated to improve strength at high temperatures.
What is heat treated parts?
Heat treated parts are essential to the operation of automobiles, aircraft, spacecraft, computers and heavy equipment of every kind. Saws, axes, cutting tools, bearings, gears, axles, fasteners, camshafts and crankshafts all depend on heat treating.
What temperature do you need to quench a cryogenic process?
Some materials are cooled slowly in the furnace, but others must be cooled quickly, or quenched. Certain cryogenic processes require treatment at -120°F or lower . Quenching media include water, brine, oils, polymer solutions, molten salts, molten metals and gases.
Why is hard surface important?
It can make parts harder, to improve strength. It can put a hard surface on relatively soft components, to increase abrasion resistance. It can create a corrosion-resistant skin, to protect parts that would otherwise corrode. And, it can toughen brittle products.
What is heat treatment?
Heat treatment is a metal processing technique used to change the physical (sometimes chemical) characteristics of a material, heating and cooling the metal under strict control to improve its characteristics, performance, and durability. In general, heat treatment can soften metals to improve formability. It can harden parts to increase strength.
Why is heat treatment important?
In this type of heat treatment, depending on the type of material, the material is heated to the required temperature and held for a specific period of time before it is cooled slowly or quickly. This process improves the microstructure of the grain, making it more uniform and easier to process. It can also be used to improve the ductility of materials for further processing and reduce the potential stress of castings.
Why is annealing used in casting?
It can also be used to improve the ductility of materials for further processing and reduce the potential stress of castings. Annealing is also commonly used to reduce the hardness of materials , which helps to improve their workability. Suitable for ferrous and non-ferrous metals.
What is quenching medium?
The quenching medium includes water, brine, oil, polymer solution, molten salt, molten metal and gas. Each has specific characteristics that make it ideal for certain applications. However, 90% of parts are quenched in water, oil, gas or polymer. Heat treatment hardness VS temperature. The effect of carbon content on the hardness ...
What is the purpose of tempering?
Further heating and cooling cycles called tempering can be used to introduce a certain degree of ductility to the part, making it tougher and less likely to break under pressure. Tempering can harden parts.
What is the process of hardening a metal?
Case hardening. Case hardening or carburization is a thermochemical process in which alloying elements (mainly carbon or nitrogen) are added to the metal surface to a certain depth (shell), only the case hardens during this process.
What is induction hardening?
Induction hardening is usually used for steel and cast iron , and the surface of metal parts is hardened by induction heating and quenching. This process can increase the hardness and brittleness of the material, which also allows you to harden specific areas of the part without damaging the remaining parts.

What Is Heat Treatment?
Why Is Heat Treatment Important?
- Without heat treating metal, especially steel, metal parts for everything from airplanes to computers wouldn’t function properly, or might not even exist in the first place. Non-ferrous metalparts in particular would be much weaker. Aluminum and titanium alloys, as well as bronze and brass, are all strengthened through heat treatment. Many of these metals are used in the pr…
Solutions from General Kinematics
- General Kinematics provides optimal equipment in order to improve and boost productivity in the heat treatment process and other manufacturing processes. There are various steps when dealing with heat treating metals, General Kinematics provides equipment designed to aid in this process and to increase manufacturing productivity.
Overview
Heat treating (or heat treatment) is a group of industrial, thermal and metalworking processes used to alter the physical, and sometimes chemical, properties of a material. The most common application is metallurgical. Heat treatments are also used in the manufacture of many other materials, such as glass. Heat treatment involves the use of heating or chilling, normally to extre…
Specification of heat treatment
Usually the end condition is specified instead of the process used in heat treatment.
Case hardening is specified by hardness and case depth. The case depth can be specified in two ways: total case depth or effective case depth. The total case depth is the true depth of the case. For most alloys, the effective case depth i…
Physical processes
Metallic materials consist of a microstructure of small crystals called "grains" or crystallites. The nature of the grains (i.e. grain size and composition) is one of the most effective factors that can determine the overall mechanical behavior of the metal. Heat treatment provides an efficient way to manipulate the properties of the metal by controlling the rate of diffusion and the rate of cooling within th…
Effects of composition
The specific composition of an alloy system will usually have a great effect on the results of heat treating. If the percentage of each constituent is just right, the alloy will form a single, continuous microstructure upon cooling. Such a mixture is said to be eutectoid. However, If the percentage of the solutes varies from the eutectoid mixture, two or more different microstructures will usually form sim…
Effects of time and temperature
Proper heat treating requires precise control over temperature, time held at a certain temperature and cooling rate.
With the exception of stress-relieving, tempering, and aging, most heat treatments begin by heating an alloy beyond a certain transformation, or arrest (A), temperature. This temperature is referred to as an "arrest" because at the A temperature the metal experiences a period of hystere…
Techniques
Complex heat treating schedules, or "cycles", are often devised by metallurgists to optimize an alloy's mechanical properties. In the aerospace industry, a superalloy may undergo five or more different heat treating operations to develop the desired properties. This can lead to quality problems depending on the accuracy of the furnace's temperature controls and timer. These operation…
Furnace types
Furnaces used for heat treatment can be split into two broad categories: batch furnaces and continuous furnaces. Batch furnaces are usually manually loaded and unloaded, whereas continuous furnaces have an automatic conveying system to provide a constant load into the furnace chamber.
Batch systems usually consist of an insulated chamber with a steel shell, a hea…
See also
• Carbon steel
• Carbonizing
• Diffusion hardening
• Induction hardening
• Retrogression heat treatment