
Once recrystallisation (static or metadynamic) is completed, the high temperature will favour austenite grain growth if the interpass time during hot working is long enough. The reason for this growth is the reduction of the internal energy obtained by decreasing the total austenite grain boundary area.
Full Answer
What happens to steel grains during a heat treatment?
As the temperature rises in a heat treatment furnace, strange transformations occur. In steel workpieces, the grain structure of the component changes size. Alternatively, new grains form. They undergo phase transformative processes. There’s carbon in the mix, too.
What happens to the grain size at austenitizing temperatures?
At these austenitizing temperatures, the grain uniformly changes size. Held for a predetermined period at this temperature, the steel is then cooled at room temperature.
What is grain growth in Materials Science?
In materials science, grain growth is the increase in size of grains ( crystallites) in a material at high temperature. This occurs when recovery and recrystallisation are complete and further reduction in the internal energy can only be achieved by reducing the total area of grain boundary.
What is ideal grain growth?
Computer Simulation of Grain Growth in 3D using phase field model. Click to see the animation. Ideal grain growth is a special case of normal grain growth where boundary motion is driven only by local curvature of the grain boundary. It results in the reduction of the total amount of grain boundary surface area i.e. total energy of the system.
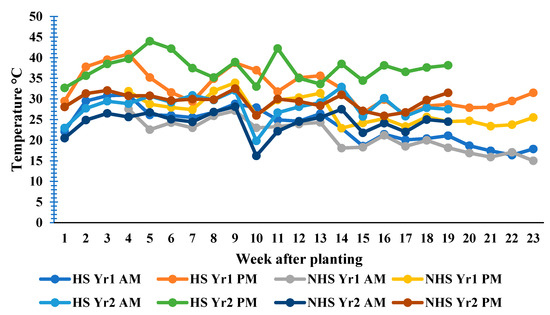
How does temperature affect grain growth?
From the results it is concluded that there is a relationship between temperatures interrelated heating, heating rate and holding time on the growth of austenite grain. The higher the temperature, the heating occur austenite grain size.
What is the driving force for grain growth during heat treatment?
The driving force for grain growth, being it continuous (normal grain growth) or discontinuous (abnormal grain growth), is the energy of the high angle boundaries. The main driving force for recrystallization to occur is the stored energy during straining in the form of crystalline defects.
What temperature does grain growth occur?
Then, there is an intermediate temperature region where significant grain growth takes place. The onset of this temperature region is commonly referred to as the grain-coarsening temperature (1050 °C in the present example).
Does heating reduce grain size?
Grain Size Effect: It has long been known that the properties of some metals could be changed by heat treating. Grains in metals tend to grow larger as the metal is heated. A grain can grow larger by atoms migrating from another grain that may eventually disappear.
What causes grain size to increase?
Control of Grain Size Larger grains reduce the strength and toughness of the material, and grains can grow for various reasons. For example, if the material is left at above recrystallization temperature for too long, the grains increase in size as diffusion occurs across the grain boundaries.
Does annealing increase grain size?
The final grain size depends on the annealing temperature and annealing time. For a particular annealing temperature, as the time at the temperature increases the grain size increases. For a particular annealing time, as the temperature increases the grain size increases.
What is the grain growth process?
Grain growth refers to an increase in the size of crystallites (grains) in a material at high temperatures. Grain growth is due to an alteration of the internal energy of the molecular structure of a given metal, ceramic or mineral.
What are the 3 stages of annealing?
There are three main stages to an annealing process.Recovery stage.Recrystallization stage.Grain growth stage.
What is recovery recrystallization and grain growth in heat treatment?
RECOVERY, RECRYSTALLIZATION, AND GRAIN GROWTH are microstructural changes that occur during annealing after cold plastic deformation and/or during hot working. These three mechanisms are sometimes referred to as restoration processes, because they restore the microstructural configuration to a lower energy level.
How does hot working affect grain structure?
Hot working improves the engineering properties of the workpiece because it replaces the microstructure with one that has fine spherical shaped grains. These grains increase the strength, ductility, and toughness of the material.
How does heat treatment effect microstructure?
The heating and cooling treatment of the steel specimens have a great effect on the phase of the microstructure of the steel specimen. The addition of alloys or coarsening of the austenitic grain structure increase the hardenability of steel.
Does grain size strengthening work at high temperatures?
The recrystallized grain size of ETP copper decreases with an increase in strain rate. This 'effect becomes more pronounced when the temperature is increased. The results also indicate that the recrystallized grain size increases with working temperature.
What is the purpose of dopants in sintering?
To mitigate this problem in a common sintering procedure, a variety of dopants are often used to inhibit grain growth.
What is discontinuous growth?
In the latter, the changes occur heterogeneously and specific transformed and untransformed regions may be identified. Abnormal or discontinuous grain growth is characterised by a subset of grains growing at a high rate and at the expense of their neighbours and tends to result in a microstructure dominated by a few very large grains. In order for this to occur the subset of grains must possess some advantage over their competitors such as a high grain boundary energy, locally high grain boundary mobility, favourable texture or lower local second-phase particle density.
What is the difference between continuous and discontinuous grain growth?
Distinction between continuous (normal) grain growth, where all grains grow at roughly the same rate, and discontinuous (abnormal) grain growth, where one grain grows at a much greater rate than its neighbours.
What is the driving force for the total area of boundary to be reduced?
As a result, there is a thermodynamic driving force for the total area of boundary to be reduced. If the grain size increases, accompanied by a reduction in the actual number of grains per volume, then the total area of grain boundary will be reduced.
What happens when grain boundaries meet at angles other than 120 degrees?
When grain boundaries in a single phase meet at angles other than 120 degrees, the grain included by the more acute angle will be consumed so that the angles approach 120 degrees.
What is boundary movement?
Boundary movement is discontinuous and the direction of motion may change suddenly. One grain may grow into another grain whilst being consumed from the other side. The rate of consumption often increases when the grain is nearly consumed. A curved boundary typically migrates towards its centre of curvature.
How does polycrystalline material affect the microstructure?
The practical performances of polycrystalline materials are strongly affected by the formed microstructure inside, which is mostly dominated by grain growth behaviors . For example, most materials exhibit the Hall–Petch effect at room-temperature and so display a higher yield stress when the grain size is reduced (assuming abnormal grain growth has not taken place). At high temperatures the opposite is true since the open, disordered nature of grain boundaries means that vacancies can diffuse more rapidly down boundaries leading to more rapid Coble creep. Since boundaries are regions of high energy they make excellent sites for the nucleation of precipitates and other second-phases e.g. Mg–Si–Cu phases in some aluminium alloys or martensite platlets in steel. Depending on the second phase in question this may have positive or negative effects.
What happens when the temperature rises in a heat treatment furnace?
As the temperature rises in a heat treatment furnace, strange transformations occur. In steel workpieces, the grain structure of the component changes size. Alternatively, new grains form. They undergo phase transformative processes. There’s carbon in the mix, too. As those phase changes take place, the alloy-strengthening element becomes more soluble. The carbon diffuses, so the workpiece hardens. Here, this list of phase states should clarify the matter somewhat.
What temperature does steel ferrite melt?
Using between 750°C and 980°C (the temperature varies because of carbon content) of furnace heat, all of the steel ferrite is transformed into a harder, uniformly distributed pearlite structure.
What changes when grain structure is altered?
By the way, the electrical conductivity and magnetic parameters change when the grain structure is altered. Typically, however, the process targets mechanical hardenability, fatigue resistance, malleability and workability, and corrosion resistance, too.
Can ferritic steel diffuse carbon?
Body-centred ferritic steels can’t easily diffuse carbon. Infusing more thermal energy into the process, taking the temperature gradient up to that 750 to 980°C sweet spot, the grain structure transforms. Face-centred austenite allows the carbon to diffuse. Hard islands of cementite dissolve, and now the crucial moment has arrived. If the second half of the heat treatment process mirrors the first half, then the carbon will resurface while the steel assumes its ferritic microcrystalline structure once more. Obviously, that’s not the result we’re after. Taking control of that second stage, the cherry-hot steel is quenched in oil or water. Now, because of the sudden cooling, the carbon becomes locked inside the cubic grains.
Is martensitic steel brittle?
Produced after the high temperatures and quenching operations are complete, martensitic steels are super-hard but brittle until tempered. Austenitic processing changes the nickel-to-chromium ratio slightly so that the alloy gains a stronger corrosion resistance feature. They’re also non-magnetic. By the way, the electrical conductivity and magnetic parameters change when the grain structure is altered. Typically, however, the process targets mechanical hardenability, fatigue resistance, malleability and workability, and corrosion resistance, too. Magnetism and conductivity are important, too, of course, just not as process-integral as those mechano-chemical attributes.
Is magnetism a process-integral attribute?
Magnetism and conductivity are important, too, of course, just not as process-integral as those mechano-chemical attributes. At the end of the day, there are ingredients and heat treatment temperatures to manage. The ingredients are already inside a steel workpiece, or they’re added to a furnace’s atmosphere.
Most recent answer
FYI, here is an example of thermal activated transformation of cluster defects into dislocation.
All Answers (8)
This is quite clear: Temperature has more influence on grain growth than time. Temperature increase by 10-20°C often results in more than the 100-200 h additional time of the annealing. Of course, it is only for temperatures in the range of grain growth.
What is abnormal grain growth?
Abnormal grain growth is a coarsening type of microstructure where some large grains grow unusually quickly in a matrix of fine grains with a very slow growth rate. In terms of microstructure, grain size distribution is bimodal, unlike in normal grain growth with a unimodal distribution. Sometimes, a distinction between normal and abnormal grain growth is ambiguous. Abnormal grain growth is characterized by fast growth of a few large grains in a matrix of fine grains of which the size change with annealing time is almost nil or at least negligible compared to that of the abnormal grains. Abnormal grain growth can also occur in high chemical in equilibrium, such as in the Y-SiAlON system. When the Y-β-SiAlON grains form from Y-α-SiAlON in an oxynitride glass, which is in equilibrium with Y-β-SiAlON, abnormally large grains can also form.
Why is grain growth important?
Abnormal grain growth is an important method of producing large-grained materials and contributes to the processing of iron–silicon alloys for electrical applications. However, avoidance of abnormal grain growth during high-temperature heat treatment is an important aspect of grain-size control in steels. For example, the austenite grain size of a steel is an important factor controlling the transformation characteristics and thus the resulting microstructure and mechanical properties. Steels containing strong carbide- or nitride-forming elements such as niobium, aluminum, titanium, or vanadium often exhibit abnormal grain growth of austenite during austenitizing treatment.
What are the advantages of SSCG?
One of the advantages of the SSCG method is that the net shape crystal growth is possible , because the melting of ceramic precursors does not occur during the crystal growth process. Figure 6.4 shows the growth of a ring-shaped BZT single crystal. First a ring-shaped BZT powder compact was prepared by uni-axial pressing of BZT powder and sintered. After the sintering the ring-shaped BZT ceramic was placed on the top of a (100) BZT single crystal seed and then heat-treated, as shown in Fig. 6.4 (a). Figure 6.4 (a) shows the growth of a BZT single crystal from the seed crystal to the ring-shaped ceramic. Since the shape of the growing BZT single crystal was the same as that of the BZT ceramic, ring-shaped BZT single crystals were successfully fabricated without mechanical machining of single crystal blocks after the crystal growth step, as shown in Fig. 6.4 (b). As another example of the net shape crystal growth, Figure 6.5 shows the growth of a PMN–PT single crystal from a PMN–PT ceramic which was mechanically machined in a 2–2 composite form before the crystal growth step. Instead of difficult machining of brittle PMN–PT single crystals, the sintered PMN–PT ceramics were diced as shown in Fig. 6.5 (a) and heat-treated for the crystal growth. By using this technique piezoelectric single crystals can be prepared in a 1–3 or 2–2 composite form, while avoiding the mechanical machining steps of brittle single crystals.
Why are sintering additives used?
Sintering additives are usually added to powders in an attempt to enhance the sinterability and to control the microstructure. Typical examples are the addition of Ni to W for improving sinterability, and of MgO to Al 2 O 3 for suppressing abnormal grain growth and improving densification. However, for the most part the roles of sintering additives are only known empirically and their mechanisms are not well understood. This chapter considers the point defects formed by the addition of sintering additives* in ionic compounds with low defect concentrations. For a low concentration of point defects, we may assume that the matrix atoms and point defects form an ideal solution with no interaction between defects. We may assume also that the concentration of matrix atoms is 1. In this case, we can easily estimate the concentration of point defects caused by dopant addition. Therefore, in the case of lattice-diffusion-controlled sintering, the estimation can explain the change in sinterability with dopant addition.
Why is thermal stability important in FSPed?
A prior knowledge of the time and temperature up to which the microstructure is stable is helpful to find the temperature range in which the FSPed material can be safely used or further processed for shaping or manufacturing. In order to evaluate the thermal stability, the processed nonequilibrium composites were subjected to thermal exposure for 10 minutes at different temperatures on the same area followed by EBSD of the exposed area. Results of Al–Ti composite are mainly presented here.
Why do grains grow faster during AGG?
During AGG, a few grains grow much faster than surrounding fine matrix grains so that the microstructure exhibits a bimodal distribution of grain size. Abnormal grains usually grow until they impinge each other. This suggests the possibility of single crystal growth by controlling AGG.
Why is grain size control important?
Grain-size control is important practically for the improvement of mechanical properties of steels. Grain growth is retarded by solute or impurity atoms and the second-phase particles. Since most commercial steels contain various precipitates such as cementite, MnS, AlN, and alloy carbides, the Zener pinning effect is most important during grain growth in austenite and ferrite. Although Zener’s model seems to be generally accepted and is frequently described in various articles, there have been surprisingly few quantitative data testing this effect, probably because of the difficulty of designing a suitable experiment. For example, to estimate the Zener limiting grain size for practical heat treatment purposes, various modified equations have been proposed as summarized in Table 1. Therefore, much more quantitative experimental data on R ¯ c, especially for the case of lower fv, are needed.
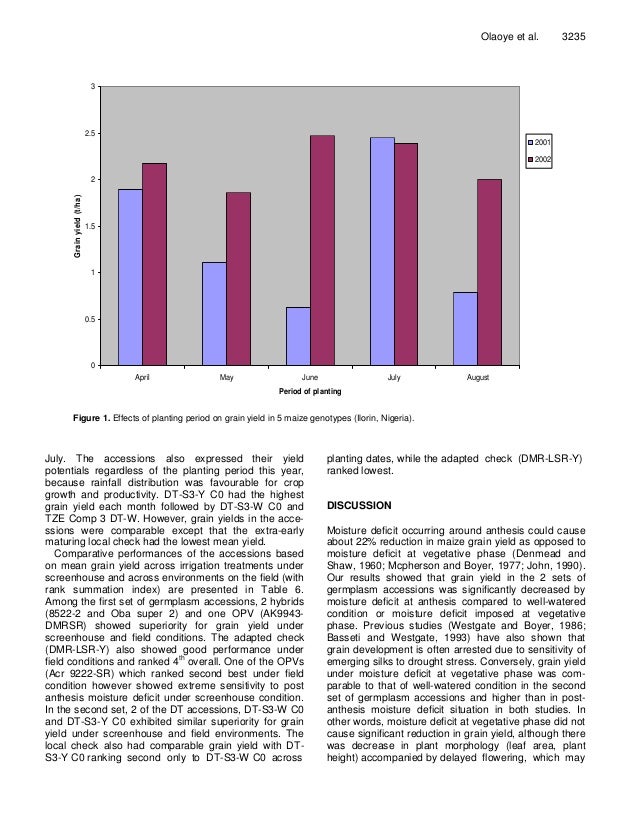
Overview
In materials science, grain growth is the increase in size of grains (crystallites) in a material at high temperature. This occurs when recovery and recrystallisation are complete and further reduction in the internal energy can only be achieved by reducing the total area of grain boundary. The term is commonly used in metallurgy but is also used in reference to ceramics and minerals. The behaviors of grain growth is analogous to the coarsening behaviors of grains, which implie…
Importance of grain growth
The practical performances of polycrystalline materials are strongly affected by the formed microstructure inside, which is mostly dominated by grain growth behaviors. For example, most materials exhibit the Hall–Petch effect at room-temperature and so display a higher yield stress when the grain size is reduced (assuming abnormal grain growth has not taken place). At high temperatures the opposite is true since the open, disordered nature of grain boundaries means t…
Rules of grain growth
Grain growth has long been studied primarily by the examination of sectioned, polished and etched samples under the optical microscope. Although such methods enabled the collection of a great deal of empirical evidence, particularly with regard to factors such as temperature or composition, the lack of crystallographic information limited the development of an understanding of the fundamental physics. Nevertheless, the following became well-established features of grain gro…
Driving force
The boundary between one grain and its neighbour (grain boundary) is a defect in the crystal structure and so it is associated with a certain amount of energy. As a result, there is a thermodynamic driving force for the total area of boundary to be reduced. If the grain size increases, accompanied by a reduction in the actual number of grains per volume, then the total area of grain boundary will be reduced.
A general theory of grain growth[6]
Recently, grain growth behaviors including normal, abnormal and stagnant behaviors can be interpreted by a general theory with a mathematical formula. According to this general theory of grain growth, normal grain growth only occurs in the polycrystalline systems with fully roughening grain boundaries, and abnormal and/or stagnant grain growth can inherently occur in the polycrystalline systems with non-zero GB (grain boundary) step free energy of grains.
Ideal grain growth
Ideal grain growth is a special case of normal grain growth where boundary motion is driven only by local curvature of the grain boundary. It results in the reduction of the total amount of grain boundary surface area i.e. total energy of the system. Additional contributions to the driving force by e.g. elastic strains or temperature gradients are neglected. If it holds that the rate of growth is proportional to the driving force and that the driving force is proportional to the total amount of …
Self-similarity
An old-standing topic in grain growth is the evolution of the grains size distribution. Inspired by the work of Lifshitz and Slyozov on Ostwald ripening, Hillert has suggested that in a normal grain growth process the size distribution function must converge to a self-similar solution, i.e. it becomes invariant when the grain size is scaled with a characteristic length of the system that is proportional to the average grain size .
Normal vs abnormal
In common with recovery and recrystallisation, growth phenomena can be separated into continuous and discontinuous mechanisms. In the former the microstructure evolves from state A to B (in this case the grains get larger) in a uniform manner. In the latter, the changes occur heterogeneously and specific transformed and untransformed regions may be identified. Abnormal or discontinuous grain growth is characterised by a subset of grains growing at a high …