
What are reducing conditions in pottery?
The soluble salts are hygroscopic, and as the relative humidity rises and falls, the salts repeatedly dissolve and crystallize. These salts eventually reach the surface of the pot, where extensive crystallization takes place causing exfoliation of the surface of the pot. Eventually, the pot will break as a result of internal stresses.
Does water affect the durability of pottery?
Here are some tips for changing the makeup of the glaze to avoid crazing: Increase the silica. Decrease the feldspar. Decrease any materials containing potash/soda. Increase the boric oxide. Increase the alumina. In addition to the above, thinning down the glaze may also help reduce or eliminate crazing. The thicker the glaze, the more liable ...
What happens to pottery after it has been fired?
The mesh is lightly molded against the inner or outer surface of the pot and allowed to cool, then the mesh shape is refined with scissors to be slightly larger than the hole it will fill. The edges of the mesh section are then dipped in warm water to soften them and the fill section is pressed into position on the B72-coated edges of the pot.
Why do pieces of pottery survive so long?
Mar 01, 2008 · A higher bisque temperature reduces the absorbency of the bisque pottery while lower temperatures increase absorbency. Gums such as CMC or Vee Gum CER (¼ to 2% based on the dry weight of the glaze) can be added to the glaze to slow down the drying time and increase the durability of the raw glaze surface.
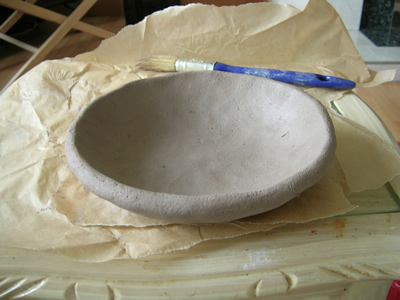
What is surface treatment in pottery?
What does the glaze do to the pots?
Why is it important to not put glaze on the bottom of your pot?
What happens if you put too much glaze on pottery?
What does glaze mean in ceramics?
Can you glaze pottery without a kiln?
What happens if you glaze the bottom of pottery?
What happens when you glaze the bottom of pottery?
Can you put underglaze on the bottom?
Why does glaze crack on pottery?
What does crazing look like on pottery?
Why is my glaze pitting?
Why do pots have glaze?
Most pots are glazed, ie they are covered by a thin coating of glass. This can be for aesthetic or for practical reasons, usually both. It is particularly important for pots holding food. The glaze usually has three main components:
What happens when clay is put in water?
If at this point the clay object is put into water it will disintegrate and can be returned into a workable state.
Why is the handle of the earthenware cup hot?
The water in both should be hot; the handle of the earthenware cup will also be hot, while that of the stoneware cup will be cold. Since microwave ovens heat water by causing water molecules to move faster, the hot handle on the earthenware cup indicates the presence of free, mobile water molecules.
What is the oldest thing made of clay?
The earliest known example of a pottery vessel was made around 18 000 years ago. 1 Since then, the craft of pottery has developed in all parts of the world, both for the practical purposes of making usable vessels for food and storage, and as expressions of the instinct for art and ritual. About 7000 years ago the Egyptians discovered the art of glazing their pots. Subsequently the Chinese steadily improved kilns and so it was possible to produce more and more highly decorated stoneware and porcelain.
What is the mineral used in pottery?
The important mineral in pottery is kaolinite, which contains 1:1 silicon to aluminium oxides. The crystal structure shows plate-like particles, which are stacked in layers linked by hydrogen bonds. It is through the structure, properties and transformations of kaolinite that we can understand the physical changes involved in the making of a pot. Although there are deposits of virtually pure kaolinite, in practice it is always used as part of a mixture with other minerals, either because it is dug out of the ground in an impure state and used directly or because it is blended with other minerals (eg feldspar and quartz) to achieve the desired properties. 2
How long has pottery been around?
The chemistry of pottery. Pottery vessels have been made for around 18,000 years. But how does clay extracted from the earth become a colourful pot, and what's the chemistry behind the process? The process of firing a pot creates crosslinks between the hydroxyl groups in the clay. Oxides of the first row transition metals are the main sources ...
What is flux in pottery?
fluxes, generally alkali or alkaline earth metal oxides, to lower the melting point of the mixture to the temperature of firing. 2. In addition, it is common to include transition metal oxides to provide colour to the glaze. A potter needs to consider three important properties of a glaze.
What is crazing in pottery?
Crazing is the effect on pottery which causes it to have a web of tiny cracks over its surface. These are not cracks in the actual structure of the pottery but actually an effect on the glazed part of the pottery. Although crazing is generally a surface affliction, it can weaken the integrity of your piece in time, ...
How to avoid crazing in glaze?
Here are some tips for changing the makeup of the glaze to avoid crazing: Increase the silica. Decrease the feldspar. Decrease any materials containing potash/soda. Increase the boric oxide. Increase the alumina. In addition to the above, thinning down the glaze may also help reduce or eliminate crazing. The thicker the glaze, the more liable it is ...
What causes glaze to crack?
Crazing generally occurs with age but there are other factors which cause immediate crazing which include: 1 Temperature and humidity changes which causes the glaze to crack 2 It can be caused by moisture getting into the glaze and forcing cracks in the glaze 3 It can be caused by being bumped or knocked repeatedly, causing small cracks in the glaze
How to avoid instant crazing?
To avoid instant crazing, experimentation with different recipes of glaze and clay will help you to understand what works for you and also adjusting the temperature and length of your firing cycle will help to avoid this occurrence if you control the parameters carefully.
How to reduce crazing?
Crazing can also be reduced by increasing the firing time and slowing down the cooling. One example of how to achieve this is to extend the last section of the firing section to a few hours so that the glaze expands slowly. This will also give the clay body the best chance to tighten and achieve a good glaze fit.
Why change the glaze makeup?
Changing the glaze. The aim of changing the glaze makeup is to reduce the expansion of the glaze (and therefore to stop it contracting as much on cooling). In simple terms, this means adding materials with low levels of expansion and decreasing materials with high levels of expansion. This can be a tricky process and may take some experimentation ...
Can silica crack clay?
Too much silica can cause more cracks however, and too little can make the clay difficult to glaze, so there is some experimentation required as to what works for you and your chosen finish.
What is reassembling pottery?
Reassembling broken pottery from archaeological excavations is a periodic feature of an object conservator's professional life. In past times pots have been reassembled with adhesives (such as unstabilized cellulose nitrate) which have deteriorated quite rapidly over a few decades to deform and become brittle—it is not safe to handle objects with such deteriorated adhesives since the adhesive joins can fail unpredictably. Other adhesives (such as early poly vinyl acetates) yellowed and caused staining of the pottery fabric. Some early restorers, in their desire to produce a beautiful result, zealously painted over original decoration and added handles to give what they thought was a pleasing appearance to the restored object. Over-restoration leads to a false impression of a pot, so we are careful when reassembling pottery to make restoration clearly distinguishable from the original and to use adhesives which have good aging properties, are reversible, and will show little color change as they age. In general, conservators are guided by the ideal of minimum intervention—intervene as little as possible.
What filler is used for low fire pottery?
In general, for low-fired archaeological pottery we use a cellulose-modified gypsum filler such as Polyfilla, often applied over a support mesh.
How many edges should a pottery sherd be held on?
In this case we adopt three basic principles: A pottery sherd should always be held on at least two edges. Fill materials must be reversible and isolated from the original pottery fabric. Fills should be appear different from the original pottery fabric both under visible light examination and when the pot is x-rayed.
How to prevent cracks in pottery?
Slow drying of leather-hard pottery or sculpture is often thought to prevent cracks. Many potters dry their work under plastic or water-saturated cloths wrapped in plastic. However, when this type of drying technique works, it is more likely due to even drying conditions. Pottery can be dried very fast if it is dried evenly. Slow drying often wastes time and can delay the onset of a crack that is already present due to improper selection of a clay body, incorrect forming technique or excessive use of water during the forming process.
Why is my pottery shivering?
For functional pottery, a nonabsorbent clay body will ensure strength and increase the potential for a stable glaze fit. Shivering occurs when the fired glaze chips off the clay body. Another less prevalent clay body/glaze mismatch is shivering, where the fired glaze chips off the clay body.
Why is firing a kiln faster?
While firing the kiln faster can cut energy costs, it can also leave the clay body and glaze immature. Decreasing the firing time can also produce less-durable pottery . Clay and glazes not only need an end point temperature for maximum strength and durability, they also require the appropriate time to reach that temperature. Any cost savings in fuel can be more than offset by functional pottery breaking or glaze surfaces being prone to abrasion and chemical attack from food/drink or everyday cleaning detergents.
What is glaze in pottery?
Glazes serve two basic functions. They produce smooth surfaces that can be easily cleaned, and they add an aesthetic quality to the pottery. Glazes can never be considered sealants. If the clay body is absorbent, liquids or solids can penetrate slight imperfections in the glaze layer.
What happens if an apprentice potter changes one variable?
If the apprentice potter changed one variable, he risked losing a whole kiln load of pottery. The uncertainty of results often called for reassuring myths and dogma. Some myths are related to various studio techniques that are handed down from misguided teacher to student or are transferred among potters.
What temperature is pottery fired at?
While pottery fired at c/06 (1828ºF) to c/04 (1945ºF) can use food-safe commercial glazes, the underlying clay body is often porous, trapping organic material and creating the ideal surface for bacterial growth.
Is ceramic art a science?
The making of ceramic objects is, at best, part science and part intuitive art . In the past, the basic science of pottery production was somewhat hit or miss. Without an extensive understanding of the underlying theories concerning ceramic materials, potters were often left with myths and inaccurate information on forming techniques, glaze formulas and firing processes.
How to remove mineral deposits from art pottery?
For lighter mineral deposit staining a day or two of soaking the item in the vinegar is all that is necessary to the remove the mineral deposits. On art pottery that has extensive mineral deposit deposition extended soaking may be required. At times the extended soaking may take weeks to remove the deposits from your art pottery. On art pottery requiring extended soaking to remove lime or calcium buildup we often rub the problem deposits daily with a butter knife to breakup the deposits and thus allow the vinegar to better penetrate the buildup. For extended soaking, we also change the vinegar regularly. Obviously if doing this you must be very careful to avoid damage to your art pottery item.
What is the best way to remove darkened crazing from antique pottery?
Removing darkened crazing from antique art pottery: Hydrogen peroxide can typically be used to lighten darkened crazing on Roseville, Rookwood, Van Briggle, Weller, and other glazed art pottery. Over the years we have heard of numerous techniques for using peroxide to effectively lighten darkened crazing.
How to get vinegar smell out of art pottery?
After you have got the pottery as clean as you can, wash the vase with soap and warm water. You will then need to soak your art pottery in tap water until the vinegar smell is gone.
How to remove rust stains from pottery?
The most effective thing we have found to remove mineral deposits such as calcium, lime, and rust stains from art pottery such as Roseville, Van Briggle, Rookwood, Weller, and others is to soak the vase in full strength white vinegar.
How long does it take to remove calcium from pottery?
At times the extended soaking may take weeks to remove the deposits from your art pottery. On art pottery requiring extended soaking to remove lime or calcium buildup we often rub the problem deposits daily with a butter knife to breakup the deposits and thus allow the vinegar to better penetrate the buildup.
How long does it take to clean a vase with peroxide?
The process can take weeks and even months in some cases.
How to remove silver marks from pottery?
To use metal polish to remove marks from your art pottery, simply put a little bit of the Noxon on a rag and rub the silver marks. The rubbing process does typically take a considerable amount of elbow grease but is definitely worth the effort in bringing your art pottery back to factory fresh condition.
Why use premixed clay?
Use premixed clay to avoid exposure to large quantities of clay dust.
How many cases of lead poisoning were reported in British potters in 1897?
In fact, over 400 cases of lead poisoning were reported in British potters in 1897. Lead frits and good housekeeping greatly lowered the number of potters that had been poisoned by these highly toxic lead compounds. Frits are made of melted minerals and metal compounds that are sintered and ground into powder form.
What is the name of the disease caused by the inhalation of large amounts of silica during clay mixing?
There have been known cases of silicosis, or "potter's rot, from chronic inhalation of large amounts of free silica during clay mixing. Symptoms of silicosis include: shortness of breath, dry cough, emphysema, and high susceptibility to lung infections such as tuberculosis. The disease may take years to develop.
What is a glaze used for?
Glazes. Glazes used to color or finish clay pieces are a mixture of silica, fluxes and colorants. Common fluxes include lead, barium, lithium, calcium and sodium, and are used to lower the melting point of silica.
What minerals are used in a glaze?
Minerals containing these fluxes include certain feldspars, nepheline syenite, petalite, bone and plant ashes, whiting, and dolomite. An assortment of metal oxides or other metal compounds produce particular colors when fired. These are added in such small amounts to the glaze, that they aren't usually a great hazard.
What ventilation should be used for clay mixers?
All clay mixers should be equipped with local exhaust ventilation to remove fine silica dust particles from the air.
How to recondition clay for kickwheels?
Be careful of the moving parts on kickwheels. Recondition clay by cutting still-wet clay into small pieces, letting them air-dry, and soak in water. Finish green ware while still wet or damp with a fine sponge instead of sanding when dry. Do not sand greenware containing fibrous talc.
How to get drips off of a pot?
Resist the urge to wipe the drip with a sponge. Let the drip dry, then carefully scrape it off with a dental tool or metal rib. Use a small compact brush to wipe away glaze in areas you can’t reach with a sponge.
How to keep glaze from dripping?
Don’t brush glaze from the big glaze bucket. Pour a small amount into a cup , then briskly stir it occasionally to ensure that it stays properly mixed. Keep a large, damp sponge nearby to keep the brush handle clean. Stray drips often start with a handle full of glaze.
How to remove rough spots from bisque?
Use silicon carbide paper to remove any rough spots you missed before bisque firing. Place your work on a piece of foam to prevent chipping. After sanding, wipe with a damp sponge to remove all traces of sanding dust. Use a damp sponge instead of rinsing, which should be kept to a minimum. Wring the sponge thoroughly and rotate it so each area is only used once. I tend to use half a dozen or so of those orange round synthetic sponges during any given glazing session.
How to get glaze drips out of texture?
Use a stiff brush to help clean glaze drips out of texture.
Can you mix glazes?
Glazes must be well mixed. I use an electric drill with a Jiffy Mixer attached. If there is dry glaze caked on the sides of the bucket, sieve the glaze, then return it to a clean bucket.
What happens when you fire clay in a second kiln?
This second kiln firing causes a remarkable change in the clay and glaze. It completes the transformation of pots from a soft, fragile substance to one that is rock-hard and impervious to water and time.
What is the purpose of firing clay?
Firing clay transforms it from its humble, soft beginnings into a new, durable substance: ceramic. Ceramics are tough and strong and similar in some ways to stone. Pieces of pottery have survived for thousands of years, all because clay met fire. The temperature needed to transform soft clay into hard ceramic is extremely high ...
What is firing clay?
Firing is the process of bringing clay and glazes up to a high temperature. The final aim is to heat the object to the point that the clay and glazes are "mature"—that is, that they have reached their optimal level of melting.
What is ceramic glaze?
Glaze Firing. Ceramic glaze is an impervious layer or coating applied to bisqueware to color, decorate, or waterproof an item. For earthenware, such as fired clay pottery, to hold liquid, it needs a glaze.
Why is the kiln cooling slow?
After the desired temperature has been reached, the kiln is turned off. The cooling is slow to avoid breaking the pots due to stress from the temperature change. After the kiln is completely cool, it is opened and the newly created "bisqueware" is removed. 04 of 04.
What temperature does clay dehydrate?
When a kiln reaches about 660 degrees Fahrenheit, the chemically bonded water will begin to be driven off. By the time the clay reaches 930 degrees Fahrenheit, the clay becomes completely dehydrated. At this point, the clay is changed forever; it is now a ceramic material.
Can you fire clay in a kiln?
The temperature needed to transform soft clay into hard ceramic is extremely high and is usually provided by a kiln. You cannot fire pottery in a home oven because ovens do not get up to the high temperatures of more than 1,500 degrees Fahrenheit that you need for firing clay. 01 of 04.
How has pottery changed?
Pottery has changed a lot since the early days of hand-formed ceramic bowls and manual wheels. The biggest change within the past 100 years involves the kiln, another required tool of the pottery trade. Since potter’s wheels have been electrified, so too have kilns moved from gas to electric.
Why is pottery important?
By creating pots, they could then cook their food and improve nutrient intake from starchy plants and meat, the common foods located in the area . Because of its many utilitarian uses, pottery has been revered throughout history.
What is pottery?
Pottery is one of the oldest and most widespread of the decorative arts. As such, there is plenty to learn about the art form and the practice of creating gorgeous, functional pottery. Deneen Pottery has developed this guide to inform you about all of the different types of pottery. Let’s get started!
How long has pottery been around?
As one of the oldest human inventions, pottery has been around since before the Neolithic period, with objects dating as far back to 29,000 BC. While in the past, the pottery industry has served marginal niches, today’s pottery companies are thriving thanks in part to a resurgence in consumer demand for unique, ...
Why do people use pottery?
People will always have the same need for pottery that they’ve always had, whether it’s for utility or artistic functions. From a potters perspective, the need for pottery won’t be satisfied by manufacturers based in the U.S. Because of steep competition from low-cost imports, many domestic manufacturers are either outsourcing their manufacturing facilities to decrease costs or shutting down.
What is considered pottery?
To be considered pottery, a piece must be a fired ceramic ware that contains clay when formed. To create a piece of pottery, the potter must form a ceramic/clay body into a specific object, whether by hand built or wheel thrown techniques, and then heat it at a high temperature in a kiln to remove water from the clay.
What did the ceramists do?
From intricate painted designs that told the history of a Pharaoh’s reign to highly polished bowls and plates to elaborate animal figures , ceramists attained remarkable skill and ability that was never seen before, thanks to the invention of the potter’s wheel.
