
The normal method of heating the ink is to pre-melt it and pour it onto a stencil made from steel mesh. The mesh has a controlled electric current passed through it, it heats up and maintains the ink in a fluid printing state. The system is so efficient that it is possible to print multiple colours on glass bottles at rates up to 7000 per hour.
Full Answer
What ink to use on glass or ceramic?
If you want true metallics on glass or ceramic you will have to use inorganic enamel (ink/colour). As well as the types of inks shown above; when using inorganic inks/enamels there is an option of using what is known as Thermoplastic Ink. This is an ink system that at ambient temperatures is a wax like solid.
What happens when glass-ceramic is heated?
If the glass-ceramic is subjected to a more intense heat treatment, this HQ s.s. transforms into a keatite-solid solution (K s.s., sometimes wrongly named as beta- spodumene ). This transition is non-reversible and reconstructive, which means bonds in the crystal-lattice are broken and new arranged.
How do you heat up ink?
The normal method of heating the ink is to pre-melt it and pour it onto a stencil made from steel mesh. The mesh has a controlled electric current passed through it, it heats up and maintains the ink in a fluid printing state.
What is the process of heat treating glass?
The process of heat-treating glass is taking annealed glass, cutting it to its desired size, transferring the glass to a furnace and heating it to approximately 1,150° F. Once at this temperature, the glass exits the furnace and is then rapidly cooled, or quenched.

What type of ink is used to print on glass?
ceramic inksTo achieve high-gloss gold and silver effects, the glass industry generally employs ceramic inks. These are expensive to purchase, and the firing process is energy-intensive and therefore costly. The attractive alternative: hot stamping with UV inks.
How is printing done on glass?
There are two methods for digital printing on glass: UV-curable printing, and digital ceramic printing. Digital UV printing technology uses organic inks and employs ultraviolet light to cure (dry) the ink on the glass surface. The technology enables unlimited color combinations.
Can screen printing be done on glass?
Screen-printed glass typically has acidic and moisture-resistant features that can preserve the colors for decades. Other advantages of screen printing on glass include the ability to print on various glass thicknesses, on unlimited sizes, 3D objects, and uneven surfaces.
Can speedball ink be used on glass?
The only issue with this method, because Speedball ink is not meant for glass, the print could chip and it would not be dishwasher or food safe. In conclusion, we found this method worked amazingly well for the screen printing portion of the process.
What is ceramic print?
Digital ceramic printing on glass is a technological development used for the application of imagery, pattern or text to the surface of flat glass. Like other printing on glass methods, it uses a form of printmaking.
How do you Personalise glass?
0:0011:19So I'm using Mod Podge here I'm using the matte I don't know if this would work with the gloss orMoreSo I'm using Mod Podge here I'm using the matte I don't know if this would work with the gloss or any of the other ones I'm sure it will but I just use the matte that's what I like. Now.
What are ceramic inks?
Ceramic inks are used in glass printing, ceramic tiles, and food container printing applications. These inks are available in various colors and shades such as black, brown, red, white, blue, maroon, and others. The demand for blue, black, and brown color ink is high.
Can you 3D print directly on glass?
3D printing directly on glass is possible and is popular with many users out there. Adhesion can be difficult on a glass bed, so it's recommended that you use adhesives to help your 3D prints stick to the glass and not warp around the edges. A good bed temperature is fundamental for 3D printing on glass.
What is silk printing on glass?
Silk-screen printed glass is a special kind of decorative glass made by printing a layer of ceramic ink on the surface of glass through the screen mesh for tempering or heat-strengthening process after. As a result silk-screen printed glass is durable, scratch-proof, solar shading and with anti-glare effect.
What is enamel ink?
59000 Series Enamel Plus Screen Ink is a glossy solvent-based enamel ink formulated to screen print on a wide range of hard-to-adhere-to surfaces such as glass, metal, wood and some plastics for outdoor signs and displays.
Can you screen print onto a mirror?
The amount of materials, inks, and machinery available to printers and their clients has expanded dramatically, and we're now able to create printed graphics on almost any kind of surfaces – including printing onto mirrored materials.
How do you print on glass candles?
0:091:59Next you want to use a photo editing program to layout your image to go around the candle. I use oneMoreNext you want to use a photo editing program to layout your image to go around the candle. I use one image and I repeated it so that it would go all the way around the candle. Next it's time to print.
How to heat up ink?
The normal method of heating the ink is to pre-melt it and pour it onto a stencil made from steel mesh. The mesh has a controlled electric current passed through it, it heats up and maintains the ink in a fluid printing state.
What temperature does thermoplastic ink need to be?
When the temperature is increased to 65-70 o C (sometimes higher) the wax liquefies and depending on its composition and temperature, will have a viscosity between 800 and 2000 Cp. Thermoplastic ink is particularly useful when printing multi-colours as when the warm ink contacts the cold ceramic or glass it hardens quickly so additional colours can be over-printed.
What ink do you use for metallics?
As well as the types of inks shown above; when using inorganic inks/enamels there is an option of using what is known as Thermoplastic Ink. This is an ink system that at ambient temperatures is a wax like solid.
What is thermoplastic ink?
This is an ink system that at ambient temperatures is a wax like solid.
Can UV ink be used for underglaze?
UV curing inks cannot be applied for under-glaze applications as the pigments would be destroyed by the firing of the glaze.
Can organic pigments melt glass frit?
Organic pigments would not withstand the temperatures to melt the glass frit in the ink but they require a fraction of the energy to cure.
Does a kiln have to pass through a lehr?
This method is also used on ceramics. In both cases the printed item has to pass through a lehr in the case of glass or a kiln if it is ceramic. Both a lehr and a kiln must be very carefully controlled regarding speed, with a lehr, temperature profile and internal atmosphere, otherwise colours will change and images distort.
What are glass-ceramics and how are they produced?
Glass-ceramics combine the properties of glasses with the benefits of conventional sintered ceramics.
What are the properties of glass-ceramics?
Properties of glass-ceramics. Glass-ceramics can range from highly crystalline to containing a more substantial glassy phase. As they contain crystalline phases and, therefore, also grain boundaries, glass-ceramics can range from transparent to opaque [1,2].
Is glass ceramic tough?
In general, glass-ceramics exhibit almost zero thermal expansion and high toughness. In addition, they are resistant to thermal shock and have a high impact resistance [2].
Optical measurement methods can help ceramic engineers optimize fast firing techniques
Figure 1. Measuring scheme of the non-contact double beam optical dilatometer.
Experimental Methods
Conventional thermal analysis techniques such as differential thermal analysis (DTA), differential scanning calorimetry (DSC) and thermogravimetric analysis (TGA) are not able to provide complete information about the sintering onset temperature or the sintering rate.
Optimizing the Sintering Process
The objective of the proposed experimental procedure is to optimize fast-firing processes by determining the optimal top firing temperature that provides full densification without swelling with the minimum processing time. The specimens are prepared with a laboratory press equipped with a steel die, which yields a 15 x 5 x 5 mm sample.
Pyroplasticity
Pyroplasticity, the gravity-driven viscous deformation of a ceramic material during firing, affects the productivity of a manufacturing plant. It determines the relationship between the thickness and the rate of deformation of the material as a function of firing temperature.
Conclusion
The optical, non-contact measuring approach is extremely effective for the optimization of industrial processes, making it possible to achieve reliable measurements of the thermal behavior in terms of sintering speed (measured as shrinkage), bloating, pyroplastic deformation speed and bending.
What is the best drying system for paint?
When discussing drying systems with your paint, ink or coating manufacturer, ask them if their drying recommendations are based on a convection system, infrared system, a combination infrared/convection system, or ultraviolet method. Typically, an infrared system or combination infrared/convection system will be more efficient than convection alone, providing faster dry times and shorter systems with lower operating costs.
How thick is a spandrel ink?
For obscuration panels such as spandrel, the coating thickness for a ceramic ink may be 4-5 mils and a silicone ink, 7-14 mils, depending on whether fallout protection is desired. These coatings are commonly applied with a roll coater or spray. For organic and other coatings used for interior decorative panels, coatings will vary from 1-5 mils, and are applied using a roll coater, spray or curtain coater. Coatings used on the back of mirrors to protect the reflective properties are often applied using a roll coater or curtain coater, as well.
What is the best ink for printing glass?
Ceramic inks are the most durable, but their colors are limited. Ceramic inks consist of three parts: the colored frit that melts into the glass, a resin that holds the frit in place prior to the firing process, and a liquid medium that allows the ink to be applied. Over the years, the mediums have evolved from fast-drying pine oil to more environmentally friendly watermiscible materials. As the mediums changed, the temperature required to dry the inks increased from about 225 degrees Fahrenheit to 325°F-350°F to achieve the green strength necessary to allow for further processing such as multiple printing and handling. Ceramic inks are also available with a UV medium that “dries” the coating in a matter of seconds, using ultraviolet energy. UV coatings tend to be more costly and are not as commonly used. The preferred method for drying ceramic inks is via infrared drying equipment. (See Fig. 1).
How does air drying work?
Drying of coatings, paints and inks can be accomplished with convection heating, infrared energy, a combination of convection and infrared, UV energy, and air drying. With convection, the air is heated, transferring energy to the surface of the coating. Infrared, like the heat from the sun, provides highly efficient electromagnetic energy directly from the heat source to the coating without heating the air between. Medium wavelength infrared energy is readily absorbed by glass, whereas short wavelength infrared will generally pass through the glass.
What is the thickness of ink on a screen printer?
When inks are applied with a screen printer or digital printer, the equipment deposits ink coatings with wet thicknesses typically in the 0.5-2.0 mils range.
What is thermosetting coating?
Thermosetting coatings—often used for protecting the backs of mirrors — require crosslinking of the components in the coating, which is best accomplished using infrared radiation. “Infrared radiation is a must for thermosetting crosslinking mirror backing paints,” explains Dino Fenzi, president of Fenzi S.P.A., a manufacturer of mirror backing paint, decorative inks/coatings and specialty sealants. “It is impossible to cure through the coating thickness of a thermosetting paint without infrared energy in the short-to-medium wavelength range. Improper curing will result in poor adhesion,” he says.
How to accelerate drying of organic ink?
To accelerate drying of organic and two-component inks, a ramp/ soak approach is commonly used. For example, if the critical temperature is 300°F, infrared alone or in combination with convection can quickly and safely bring the ink to 250°F. Then, lower energy infrared, combination infrared/convection or convection alone can slowly bring the ink to the critical temperature, minimizing the potential for damage. The ramp/soak approach will often reduce the overall drying time as well, shortening the length of the oven and reducing operating costs.
What is the key to engineering glass-ceramic material?
The key to engineering a glass-ceramic material is controlling the nucleation and growth of crystals in the base glass. The amount of crystallinity will vary depending on the amount of nuclei present and the time and temperature at which the material is heated.
When was glass ceramic first used?
This technology is not entirely new, as glass-ceramic ranges were first introduced in the 1970s using Corningware tops instead of the more durable material used today. These first generation smoothtops were problematic and could only be used with flat-bottomed cookware as the heating was primarily conductive rather than radiative.
What is bioinert ceramic?
Biopassive (bioinert) ceramics are, as the name suggests, characterized by the limited interaction the material has with the surrounding biological tissue. Historically, these were the "first generation" biomaterials used as replacements for missing or damaged tissues. One problem resulting from using inert biomaterials was the body's reaction to the foreign object; it was found that a phenomenon known as "fibrous encapsulation" would occur, where tissues would grow around the implant in an attempt to isolate the object from the rest of the body. This occasionally caused a variety of problems such as necrosis or sequestration of the implant. Two commonly used bioinert materials are alumina (Al2O3) and zirconia (ZrO2).
Why are glass ceramics used in medical applications?
Glass-ceramics are used in medical applications due to their unique interaction, or lack thereof, with human body tissue. Bioceramics are typically placed into the following groups based on their biocompatibility: biopassive (bioinert), bioactive, or resorbable ceramics.
How long does it take for a glass hose to heat up?
The glass ceramic at 5 mm thick is able to withstand the pressure of a fire hose after 20–90 minutes (depending upon the grade of ceramic used) of heat in a furnace, and still allows 88% of visible light to transmit through its surface.
How is glass made?
Glass-ceramics are mostly produced in two steps: First, a glass is formed by a glass-manufacturing process. The glass is cooled down and is then reheated in a second step. In this heat treatment the glass partly crystallizes. In most cases nucleation agents are added to the base composition of the glass-ceramic.
What is glass ceramic?
Glass-ceramics are polycrystalline materials produced through controlled crystallization of base glass. Glass-ceramic materials share many properties with both glasses and ceramics. Glass-ceramics have an amorphous phase and one or more crystalline phases and are produced by a so-called "controlled crystallization" in contrast to ...
How does heat treat glass work?
The process of heat-treating glass is taking annealed glass, cutting it to its desired size, transferring the glass to a furnace and heating it to approximately 1,150° F. Once at this temperature, the glass exits the furnace and is then rapidly cooled, or quenched. Air is blown onto the glass surface on both sides simultaneously. This cooling process creates a state of high compression at the glass surfaces while the central core of the glass is in a compensating tension. The only physical characteristics of the glass that change are the improved strength and resistance to thermal stress and shock.
What is heat treated glass?
Heat-treated glass is a term used to describe glass that has been processed through a tempering furnace to alter its strength characteristics, provide greater resistance to thermal and mechanical stresses and achieve specific break patterns for safety glazing applications as compared to annealed glass. The process of heat-treating glass is taking ...
What is FT glass?
In a specification, the designation for fully tempered glass is commonly abbreviated as FT.
Why does tempered glass break?
Fully tempered glass may break without warning due to the expansion of nickel sulfide inclusions (NiS) present within float glass. To avoid the risk of spontaneous breakage in fully tempered glass, a common practice is to avoid the use of tempered glass whenever possible.
What happens to the glass when it is heat treated?
This inherent condition of heat-treated glass results in roller wave distortion and glass bow and warp. There is no industry standard for heat-treated glass roller wave
What are the physical characteristics of glass?
The only physical characteristics of the glass that change are the improved strength and resistance to thermal stress and shock. There are two kinds of heat-treated glass, heat-strengthened (HS) and fully tempered (FT).
What is the tolerance for a warp in glass?
Viracon’s tolerance for localized warp for rectangular glass is 1/32″ (0.8mm) over any 12″ (305mm). This is half of the ASTM C1048 requirement of 1/16″ (1.6mm) over any 12″ (305mm) span. Viracon’s tolerance for overall warp meets the ASTM C1048 table.
How to use ceramic frit ink?
When using ceramic frit based inks the glass is fired or tempered to fuse the inks with the glass. Due to the extreme temperatures of this process there is first a decomposition of organic additives and binders of the ink. Next there is a fusion of the frit to the substrate and pigments followed by the expulsion of voids to give a compacted structure. Lastly there is a formation of a surface with the desire properties. A successful firing of the glass and ceramic ink will result in a bubble free layer of constant thickness and homogeneous pigment dispersion within the glass.
Why do you need to fire ink?
Firing is necessary in both methods in order for the ink to be permanently infused with the glass. Printing on glass with UV pinning and curable inks came about almost 60 years later. In this method of printing, ultraviolet waves are applied on the inks, drying them to the glass. This method was the first to enable the digital printing on glass ...
What is a glass printer?
The digital glass printer is a flatbed digital printer designed with print heads to jet ceramic inks directly onto the glass. The glass remains stationary while only the printer carriage sweeps across the print table. A key feature of the printer is drop fixation in which ink droplets are dried immediately to prevent drop gain. The fixation of the ink enables a single pass of the print carriage even when printing multi layer and multi color files. The drop fixation makes inline double vision printing possible. Double vision is creating a different vision depending on which side of the glass is being viewed it is achieved by printing different graphics one on top of the other. An inline dryer was developed for real time drying to occur and to maximize factory space. A smooth color switching system in included so machine operators can easily shift between print jobs and increase throughput. The high resolution print quality - up to 720 dpi - and the precision of the printers allow glass processors to print anything from fine, sharp, small elements to complex full color images on glasses up to 3.3X18 meters in size.
What is digital printing on glass?
At the most advanced level, digital glass printers, ceramic inks, and image processing software are fully integrated with one another and each contributes to the overall advancements in the digital printing on glass process. The three part system allows for control and flexibility over the application of the ceramic inks. Transparency and levels of translucency and opacity can be precisely manipulated. There is a high level of control over color matching, and multiple colors can be printed simultaneously. Unlike screen printing, digital ceramic printing on glass does not require screens and the files are stored digitally making printing of all sizes and replacement of any panel simple, in high resolution, full color.
What is digital ceramic printing?
Digital ceramic printing on glass is a technological development used for the application of imagery, pattern or text to the surface of flat glass. Like other printing on glass methods, it uses a form of printmaking. Digital ceramic printing on glass has allowed for new possibilities and improvements in flat glass decoration ...
What is development in ink?
The development of inks is a highly controlled production process to remove any variability in the final product. The consistency in a replication of the inks results in high compatibility with the entire color palette of inks.
When was silk screen printing invented?
Silk screen printing, where the ink is applied directly onto the surface of the glass through a mesh stencil, was patented in 1907. Screen printed transfers, where the image is transferred from a paper onto the glass, was patented in the 1930s by Johnson Mattey. Firing is necessary in both methods in order for the ink to be permanently infused ...
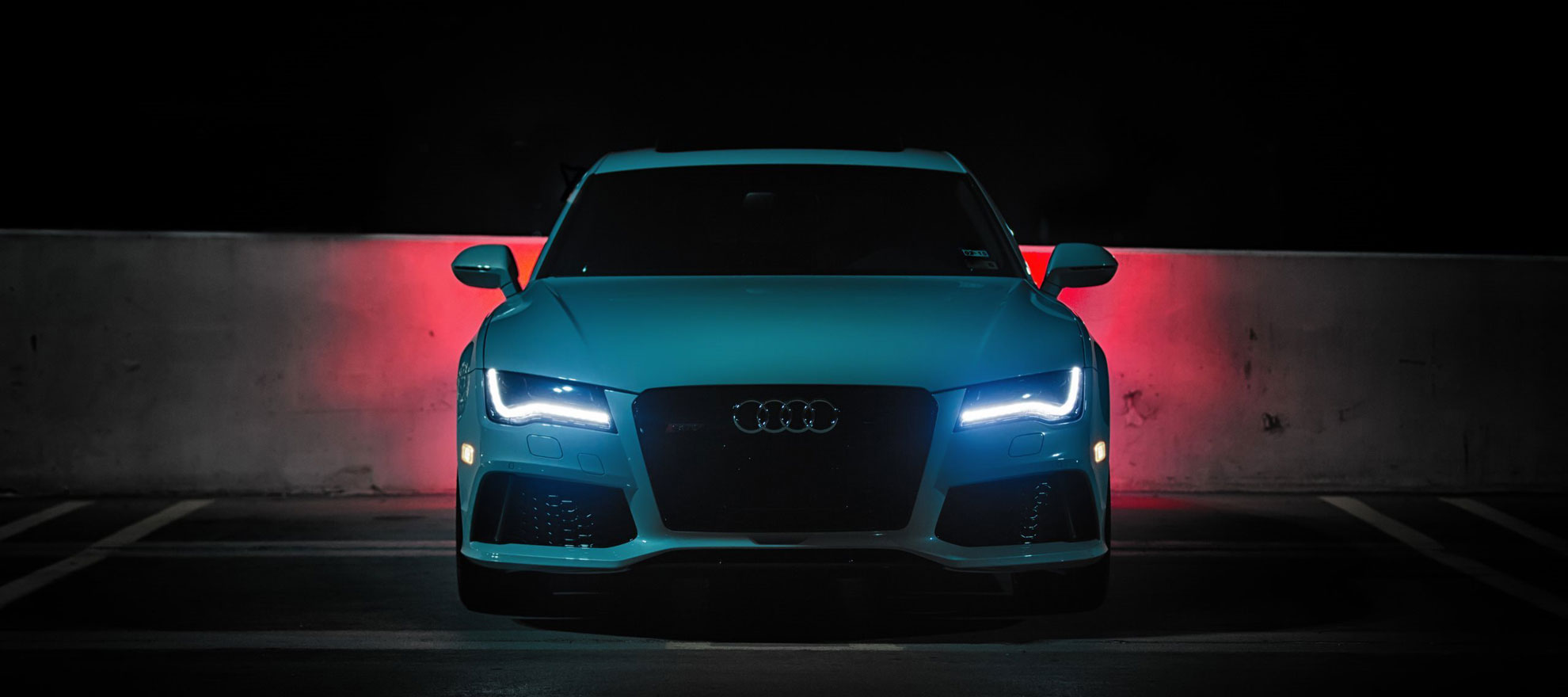
What Are Glass-Ceramics and How Are They produced?
Properties of Glass-Ceramics
Common Examples of Glass-Ceramics
- As well as the types of inks shown above; when using inorganic inks/enamels there is an option of using what is known as Thermoplastic Ink. This is an ink system that at ambient temperatures is a wax like solid. When the temperature is increased to 65-70oC (sometimes higher) the wax liquefies and depending on its composition and temperature, will h...
Applications of Glass-Ceramics
Further Reading
- Glass-ceramics can range from highly crystalline to containing a more substantial glassy phase. As they contain crystalline phases and, therefore, also grain boundaries, glass-ceramics can range from transparent to opaque [1,2]. Depending on the microstructure and the chemical composition of glass-ceramics, their properties can be tuned to meet demanding requirements. In general, gl…
Experimental Methods
- Glass-ceramics can be subdivided into two categories: oxide and non-oxide. Oxide glass-ceramics include silicate (SiO2), borate (B2O3), phosphate (P2O5) and germinate (GeO2) type materials. Non-oxide glass-ceramics include chalcogenide, halide and metallic type.
Optimizing The Sintering Process
- With their thermal and mechanical characteristics, glass-ceramics have a range of applications, including: 1. Cooktops (which you'll find in most modern kitchens) 2. Household appliances including toasters and clothes irons 3. Grills and BBQs 4. Smartphone screens 5. Infrared applications, such as in infrared heating elements 6. In high-temperature furnaces as an insulati…
Pyroplasticity
- If you would like to know more about glass ceramics, read this article: "Glass-ceramic for extreme conditions".
Conclusion
- Conventional thermal analysistechniques such as differential thermal analysis (DTA), differential scanning calorimetry (DSC) and thermogravimetric analysis (TGA) are not able to provide complete information about the sintering onset temperature or the sintering rate. The sintering process is best described by measurements of the dimensional change, a direct representation …