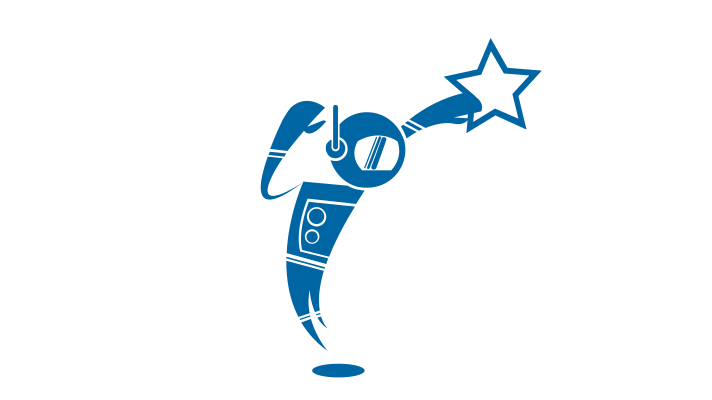
Heat treatment of metal alloys can be reduced to three simple processes: heating of raw material (semi-finished) to the desired temperature, maintaining it at the desired conditions necessary time and rapid cooling.
Full Answer
How does the earlier thermal history of alloy affect solution-heat treatment?
The earlier thermal history of alloy also effects the dissolution of the alloying elements during solution-heat treatment. For example, the rate of dissolution increases if the component has been given repeated solution heat treatment. Thus, the soaking time is decreased.
What are heat treatable and non-heat treatable alloys?
The system of designation deals separately for the non-heat treatable, strain hardening alloys on the one hand, and the heat treatable alloys on the other, such as: Strain – hardened only, as is indicated by the first suffix digit 1. The second digit indicates the amount of cold work (or strain hardening).
How does heat treatment work on super alloys?
For instance, some super alloys used in the aircraft manufacturing industry may undergo up to six different heat treating steps to optimise it for the application. In simple terms, heat treatment is the process of heating the metal, holding it at that temperature, and then cooling it back.
How do you choose the right heat treatment method?
Some heat treatment methods relieve stresses induced in earlier cold working processes. Others develop desirable chemical properties to metals. Choosing the perfect method really comes down to the type of metal and the required properties.
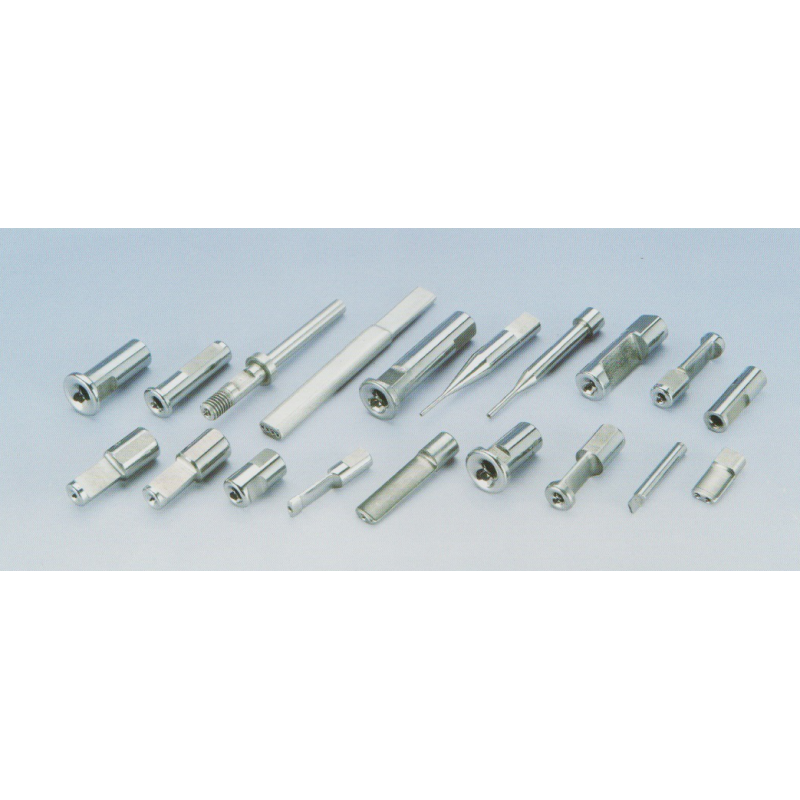
What is heat treatment of alloys?
The heat treatment of metals involves raising the temperature of an alloy, often through a prescribed thermal profile, to a defined temperature. The material is then held at this temperature for a period of time before being cooled either at a prescribed rate or under rapid quenching conditions to a fixed temperature.
What is the main heat treatment for Aluminium alloys?
Water is the most commonly used quenchant, and typically the most effective quenchant for aluminum alloys. Any forming that needs to be done to a solution heat treated part should be done very soon after quenching is complete.
What are the two types of heat treatments applicable to aluminum alloys?
A - Heat-Treatable and Non-Heat-Treatable are the two basic types of aluminum alloys. They are both widely used in welding fabrication and have somewhat different characteristics associated with their chemical and metallurgical structure and their reactions during the arc welding process.
What is the objective of heat treatment the metals and alloys?
The main objectives of heat treatment as follows: to increase strength, hardness and wear resistance (bulk hardening, surface hardening) to increase ductility and softness (tempering, re-crystallization annealing) to increase toughness (tempering, re-crystallization annealing)
What does heat treating do to aluminum?
During the forming process of some aluminum parts, our customers request heat treating processes to soften and remove stress from a part to avoid vibration issues and preserve the shape of the part.
What are several benefits of heat treatments especially tempering for aluminum alloys?
Preheating or homogenizing, to reduce chemical segregation of cast structures and to improve their workability. Annealing, to soften strain-hardened (work-hardened) and heat treated alloy structures, to relieve stresses, and to stabilize properties and dimensions.
How many types of heat treatment are there?
4 TypesWhat are the 4 Types of Heat Treating Processes? Common types of heat treating methods include annealing, hardening, quenching, and stress relieving, each of which has its own unique process to produce different results.
What is heat treatment?
Heat treatment is the process of heating metal without letting it reach its molten, or melting, stage, and then cooling the metal in a controlled way to select desired mechanical properties. Heat treatment is used to either make metal stronger or more malleable, more resistant to abrasion or more ductile.
Which furnace is used for heating Aluminium alloys?
Explanation: Aluminium alloys can be melted or heated directly or indirectly by fuel firing furnace. The heating can take place in a pot furnace, induction heating furnace, a crucible furnace or a reverberatory furnace.
What are the advantages of heat treatment?
WHAT ARE THE BENEFITS OF HEAT TREATMENT?It can change a material's physical (mechanical) properties and it aids in other manufacturing steps.It relieves stresses, making the part easier to machine or weld.Increases strength, making the material ductile or more flexible.More items...•
What is the importance of heat treatment?
Heat treating can improve wear resistance by hardening the material. Metals (including steel, titanium, inconel, and some copper alloys) can be hardened either on the surface (case hardening) or all the way through (through hardening), to make the material stronger, tougher, more durable and more resistant to wear.
What are some benefits of heat treatment of metals?
In a nutshell, the benefits of heat treatment of metals include: Increases strength, making the material ductile or more flexible. It introduces wear-resistant properties to the metal. Relieves stresses, making the part easier to machine or weld.
What are the different types of heat treatment for cast iron?
Cast iron (gray, ductile, alloy) undergoes the following types of heat treatment: annealing (at t 500-650 ), normalizing, quenching (continuous, isothermal surface), vacation, nitriding (grey cast iron), alifirova (pearlitic cast iron), chrome plating. All these treatments significantly improve the properties of the final products of cast iron: increase service life, eliminate the likelihood of cracking when you use the product, increase the strength and heat resistance cast iron.
What is heat treatment?
Heat treatment of metals and alloys is a major technological process, as in black and nonferrous metallurgy. Modern technologies have many methods of heat treatment, allowing to achieve the desired properties of each of the treated alloys. For each metal characterized by its own critical temperature, this means that heat treatment needs to be based on structural and physico-chemical characteristics of the substance. Ultimately, this will allow not only to achieve the desired results, but also largely to streamline production processes.
What is hardening metal?
Hardening – manipulation with the alloy, the purpose of which is to achieve a martensitic transformation metal that provides decreasing of plasticity of the product and increase its strength. Tempering, like annealing, involves heating metal in a furnace above the critical temperature to the quenching temperature, the difference consists in the greater speed of cooling, which occurs in the bath with the liquid. Depending on the metal, and even its shape use different types of quenching:
What is annealing in manufacturing?
Annealing-manufacturing process by which metals and alloys are heated to a defined temperature, and then with the oven, which was the procedure very slowly by natural cooling. As a result of annealing resolve the heterogeneity of the chemical composition of the substance, to remove internal stress, to achieve the grain structure and improve it as such, but also to reduce the hardness of the alloy to facilitate its further processing. There are two types of annealing: annealing the first and second kind.
Why is metal important to the economy?
Metal, as a raw material, needs to gain the desired performance properties, which can be achieved by exposure to high temperatures. Heat treatment of alloys in high temperatures changes the original structure of the substance, reallocates its components, converts the size and shape of the crystals. All this leads to minimize the internal stress of the metal and thus increases its physico-mechanical properties.
What is cryogenic alloy?
Heat treatment of the alloys at t below zero received the name of cryogenic . This technology is widely used in different industries as a complement to heat treatments with high temperatures, as it reduces the costs of thermal processes of hardening of products.
How does heat treatment work?
Heat treatment of metal alloys can be reduced to three simple processes: heating of raw material (semi-finished) to the desired temperature, maintaining it at the desired conditions necessary time and rapid cooling. Modern production uses several types of heat treatment, differing in some technological features, but the algorithm process in General everywhere is the same.
How to achieve higher hardness of carbon alloys?
The higher percentage carbon alloys can achieve a greater degree of hardness. The hardening process is achieved by heating an alloy to a predefined temperature and then quenching in oil, water, air or a special polymer quenchant. The temperature and quenching parameters are dependent on the type of steel being processed.
What are the processes that make an alloy hardened?
Carburising, nitriding, carbontriding and nitrocarburizing. In these processes the surface layers of the alloy are both hardened and strengthened by exposing the component to an enriched gaseous atmosphere of species carbon or nitrogen while the material is subjected to an elevated thermal profile prior to quenching.
What is homogenization in alloys?
This treatment is used prior to hot working processes and is performed to equalise temperatures throughout an alloy or to reduce the coring effect caused by the non-uniform chemical composition.
What is controlled atmosphere?
Controlled atmospheres are either used to reduce the effects of oxidization or to provide an enriching atmosphere for surface chemistry effects, on the component being treated. Heat Treatments are classified by their purpose:
How does heat treatment work?
The heat treatment of metals involves raising the temperature of an alloy, often through a prescribed thermal profile, to a defined temperature. The material is then held at this temperature for a period of time before being cooled either at a prescribed rate or under rapid quenching conditions to a fixed temperature.
What are the parameters and processes that can affect the composition and material properties of metal components?
The parameters and processes that can effect the composition and material properties of metal components include the following: Alloy type. Heating.
Why do we use heat treatment?
Heat treatments can be used to homogenize cast metal alloys to improve their hot workability, to soften metals prior to, and during hot and cold processing operations, or to alter their microstructure in such a way as to achieve the desired mechanical properties. Thermal treatments of metallic alloys are also used to alter the surface chemistry ...
1. Introduction
Metallic materials have widespread use in dentistry for clinical treatment and restoration of teeth.
2. Restorative dentistry and prosthodontics
Dental amalgams are prepared in the dental office by mixing particles of a silver-tin-copper alloy for dental amalgam that may contain other trace metals with liquid mercury.
3. Orthodontics
Orthodontic wires engaged in brackets that are bonded to teeth, after being deformed elastically during initial placement, provide the biomechanical force for tooth movement during unloading. There are four wire types in current clinical practice: stainless steel, cobalt-chromium, beta-titanium and nickel-titanium [ 24 ].
4. Endodontics
Traditionally, endodontic treatment was performed with stainless steel hand files and reamers to remove the injured or diseased dental pulp from the root canals of teeth.
What is steel alloy?
Steel alloys are types of steel which have had their properties enhanced through the addition of other elements, known as alloying elements. Depending on the elements alloyed with the steel, different beneficial properties can be obtained. Tempering is a heat treatment process which serves to further increase the beneficial properties of such alloys, specifically by increasing strength. It is typically used after other heat treatment processes which increase hardness, but cause the metal to become brittle. This heat treatment is extremely important for the manufacturing of parts which need to resist constant or repeated high-stresses.
Why is steel tempered?
As previously mentioned, steel can be hardened by earlier heat treatments, but this also causes it to become brittle. Tempering will retain (or improve, depending on the alloying elements) the hardness of the steel while reducing the brittleness.
What is tempered steel used for?
Tempered steel alloy parts are used for applications in which high stresses occur, or there is the constant threat of surface wear. This includes high-stress manufacturing machinery, various automobile industry applications, and parts such as keys, gears, and nuts & bolts.
What are the elements that make up steel?
These alloying elements include chromium (for stainless steels) manganese, nickel, silicon, aluminum, cobalt, molybdenum, and vanadium . Depending on the exact steel alloy in question, tempering is performed to achieve different properties and using slightly different methods.
What is the state of an alloy?
The state of the alloy in which the mechanical properties have been attained is designated by a system of temper nomenclature. It is in the form of assigning letters and digits as suffixes to the alloy number.
How long does it take to anneal a 3003 alloy?
The process consists of heating to 315 to 415°C for a time of few minutes to 3 hours (depending on alloy and thickness). The rate of heating is not important except in alloy 3003, where rapid heating is done to prevent grain growth. It is normally advisable not to raise the temperature higher than 415°C to avoid grain growth and oxidation.
What is the purpose of annealing aluminum?
The basic aim of full annealing is to increase the softness and ductility of the aluminium alloys . This heat treatment is meant if the hardening effects of the precipitation hardening heat treatment, or of cooling from the hot working temperature, are to be removed.
What are the elements that are used in wrought aluminum?
Alloying Elements: The most common alloying elements added to commercial wrought aluminium alloys, singly, or in combinations are copper, silicon, manganese, magnesium, zinc, chromium and nickel. Copper is added up to 5.5% to improve dynamic fatigue, elastic properties, strength and hardness but impairs ductility.
Why is aluminium considered a structural material?
Aluminium became a common structural material because of the following properties: 1. Light Weight: Aluminium weighs roughly one-third as much as most of the common metals, but is one and a half times as heavy as magnesium. It finds applications to reduce the weight of components and structures, particularly connected with transport, ...
Can aluminium be refrigerated?
The precipitation characteristics at room temperature vary from alloy to alloy. Thus, in such cases, the parts may be refrigerated after solution treatment, and before the ageing is done.
Is precipitation hardening based on preliminary tests?
Precipitation hardening of castings should be based on preliminary tests. The foundry practice effects lots of properties. The principles and procedures for wrought and cast products are similar. Soaking times for solution treatment of castings are much longer as castings have very coarse structures.
Tempering
The structure obtained by high temperature tempering is tempered sorbite. Tempering is generally not used alone. After the parts are quenched, the main purpose of tempering is to eliminate the quenching stress and obtain the required structure.
Annealing
The pearlite transformation occurs in the annealing process. The main purpose of annealing is to make the internal structure of the metal reach or close to the equilibrium state, in preparation for subsequent processing and final heat treatment.
What is tempering?
Tempering is a heat treatment process in which the quenched metal material or part is heated to a certain temperature, kept for a certain period of time, and then cooled in a certain way. Tempering is an operation that is performed immediately after quenching, and is usually the last part of the heat treatment of the workpiece.
What metals are heat treated?
Although ferrous metals account for the majority of heat treated materials, alloys of copper, magnesium, aluminium, nickel, brass, and titanium may also be heat treated. About 80% of heat treated metals are different grades of steel.
What is the most common heat treatment process?
The most common heat treatment process of all, hardening is used to increase the hardness of a metal. In some cases, only the surface may be hardened. A work piece is hardened by heating it to the specified temperature, then cooling it rapidly by submerging it into a cooling medium. Oil, brine or water may be used.
What is heat treatment?
Heat treatment is the process of heating and cooling metals, using specific predetermined methods to obtain desired properties. Both ferrous as well as non-ferrous metals undergo heat treatment before putting them to use. Over time, a lot of different methods have been developed. Even today, metallurgists are constantly working to improve ...
Why does the temperature of a metal change?
During the process, the metal part will undergo changes in its mechanical properties. This is because the high temperature alters the microstructure of the metal. And microstructure plays an important role in the mechanical properties of a material. The final outcome depends on many different factors.
What is a schedule in metals?
For that they develop new schedules or cycles to produce a variety of grades. Each schedule refers to a different rate of heating, holding and cooling the metal. These methods, when followed meticulously, can produce metals of different standards with remarkably specific physical and chemical properties.
What is holding metal?
Holding. During the holding, or soaking stage, the metal is kept at the achieved temperature. The duration of that depends on the requirements. For example, case hardening only requires structural changes to the surface of the metal in order to increase surface hardness.
What happens after soaking metal?
After the soaking stage is complete, the metal must be cooled in a prescribed manner. At this stage, too, structural changes occur. A solid solution on cooling may stay the same, become a mechanical mixture completely or partially, depending on various factors.
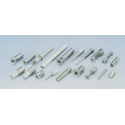
Purpose of Heat Treatment
Heat Treatment Method
- Heat treatment is defined as “the process of heating and cooling of solid steel article under carefully controlled conditions”. During heat treatment certain physical properties are altered without changes in chemical composition.
Heat Treatment Process
Causes of Heat Treatment Defects and Their Elimination and Prevention Methods
Heat Treatment Equipment and Materials
- Annealing treatment
The effect of annealing treatment is to eliminate the casting stress of the casting and the internal stress caused by machining, stabilize the shape and size of the processed part, and spheroidize part of the Si crystals of the Al-Si alloy to improve the plasticity of the alloy. The process is: heati… - Quenching
Quenching is to heat the aluminum alloy castings to a higher temperature (usually close to the melting point of the eutectic, mostly above 500 ℃), and hold for more than 2 hours to fully dissolve the soluble phase in the alloy. Then, it is quenched into water at 60-100℃ to make the c…